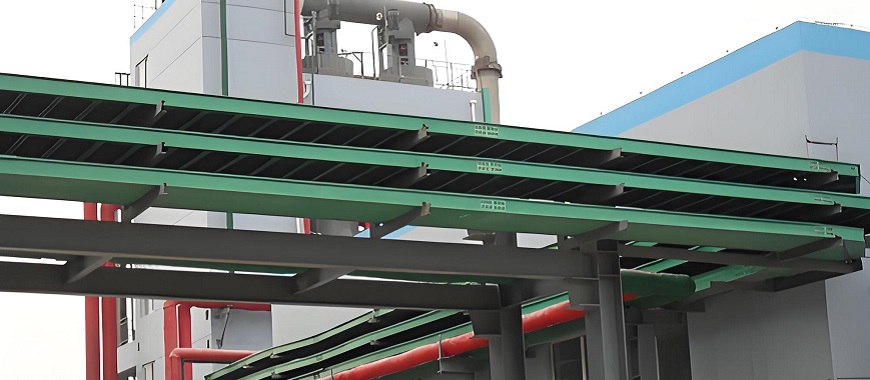
Cable tray and support systems are essential for managing and securing electrical and communication cables within various types of buildings and infrastructure. These systems provide a structured framework to support cables, ensuring they are organized, protected, and easily accessible for maintenance. In industrial, commercial, and residential installations, cable tray systems help in routing and supporting cables, making them crucial for both safety and efficiency.
By using cable tray, the risk of cable damage is minimized, and the overall safety of the installation is enhanced. These systems also allow for easy future upgrades and modifications without disrupting the entire setup. Cable tray and support systems are designed to meet the diverse needs of electrical professionals, ensuring that cables are securely held in place while being properly ventilated and protected from potential hazards. GangLong Fiberglass provides series cable tray and support systems, including mesh trays, ladders & ducts for cable management solutions.
Types of Cable Tray and Support Systems
Cable tray systems offer a reliable, scalable, and code-compliant solution for managing power, data, and control cables across a wide range of environments. Whether installed overhead, along walls, or under raised floors, cable trays serve both as structural support and as organized pathways for routing essential wiring. Choosing the right type of cable tray is key to ensuring safety, efficiency, and long-term performance. Below is an overview of the most commonly used cable tray and support systems types:
Ladder Cable Tray
Ladder cable trays consist of two side rails connected by rungs, forming a strong, open framework for supporting cables. This design allows for excellent air circulation, which helps to prevent overheating in high-power applications. The open structure also makes cable placement, inspection, and maintenance fast and easy. Ladder trays are widely used in industrial settings, power generation facilities, and heavy-duty infrastructure projects where durability, airflow, and accessibility are critical.
Wire Mesh Cable Tray (Basket Tray)
Wire mesh cable trays, also known as basket trays, are constructed from steel wire mesh and are designed for lightweight cable runs. Their open-grid structure provides excellent ventilation and makes routing changes simple. These trays are easy to cut and shape on-site, making them highly adaptable for complex layouts. They’re ideal for commercial buildings, data centers, and telecommunications rooms where flexible routing and airflow are priorities without the need for heavy support structures.
Solid PVC Cable Routing System
Solid PVC cable trays are designed with enclosed bottoms and sidewalls to provide stable, even support for delicate or bend-sensitive cables like fiber optics. Their smooth interior prevents cable sagging and avoids sharp bends that could damage sensitive lines. These trays are commonly used in telecom environments, cleanrooms, or any installation requiring maximum protection and a dust-resistant pathway. PVC trays are non-metallic, lightweight, and corrosion-resistant, making them safe and easy to install.
Enclosed Cable Tray
Enclosed cable trays feature solid sides and bottoms that fully protect enclosed cables from environmental hazards such as dust, moisture, and chemical exposure. They are ideal for areas where cable cleanliness, security, and long-term protection are essential. These trays are frequently used in chemical processing facilities, outdoor applications, and food-grade environments where open systems are unsuitable. Enclosed trays also reduce electromagnetic interference when used with sensitive cabling.
Fiberglass Cable Tray
Fiberglass cable trays are made from fiberglass-reinforced plastic (FRP), offering excellent resistance to corrosion, UV exposure, and harsh chemicals. As non-conductive systems, they eliminate the need for grounding and provide a safer option in electrical or corrosive environments. Lightweight yet durable, fiberglass trays are widely used in offshore, wastewater treatment, and chemical facilities. They offer a long service life and maintain structural strength even in extreme conditions.
Modular or Cope Cable Tray
Modular or Cope cable trays are composed of interlocking components that enable fast assembly and easy reconfiguration. This design provides excellent flexibility, especially in environments where infrastructure frequently changes. Their adaptability makes them ideal for data centers, research labs, or dynamic industrial systems. These trays support quick layout modifications without replacing entire runs, saving time and labor costs while maintaining clean, secure cable routing.
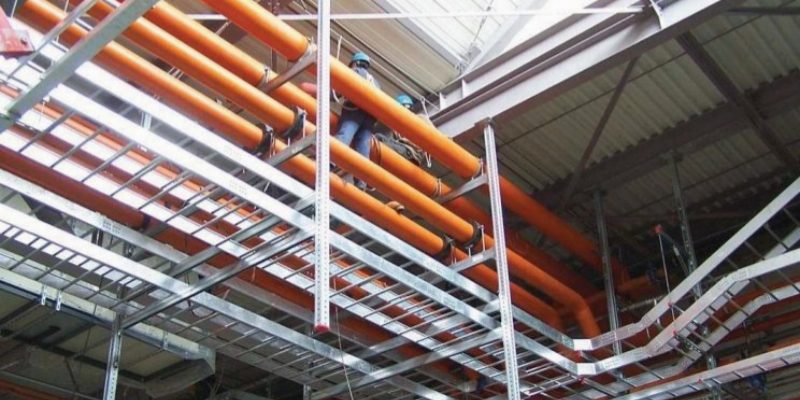
The Role of Trinity Cable Tray in Modern Electrical Systems
Cable Tray and Support Systems: Support Typeses
Choosing the right support type is essential to ensure the stability and durability of cable tray and support systems. Here are some of the most common support types:
Universal Supports
- Description: Universal supports are adaptable and can be used with a variety of tray sizes and configurations, including movable cable tray systems. They provide flexibility in cable tray installation.
- Features: These supports are easy to adjust, durable, and can be mounted in various ways to suit different types of installations.
- Applications: Universal supports are frequently used in both industrial and commercial applications where flexibility is key.
Strut Supports
- Description: Strut supports are made of steel and are designed to support cable trays on elevated surfaces or in open spaces.
- Benefits: These supports offer excellent strength and stability, making them ideal for heavy-duty applications.
- Ideal Uses: Strut supports are common in large-scale industrial facilities or areas where maximum cable support is needed.
Beam Mount Brackets
- Description: Beam mount brackets are used to attach cable trays directly to beams or ceiling structures.
- Features: These brackets are adjustable to fit different beam sizes and provide strong, secure support for cable trays.
- Applications: Beam mount brackets are typically used in factories, warehouses, and other industrial settings where overhead installations are required.
Hold Down Clamps
- Description: Hold down clamps are designed to secure cables within the trays, preventing them from shifting or moving during installation or after setup.
- Benefits: They help ensure the cables remain organized, reducing the risk of damage and keeping the installation neat and stable.
- Ideal Uses: Hold down clamps are essential in high-vibration environments, such as manufacturing plants, where movement could potentially cause cable damage.
Comprehensive Guide to B Line Cable Tray Barrier Features
Cable Tray and Support Systems: Industrial Cable Tray Systems
Industrial cable tray and support systems are built to withstand harsh conditions while managing large volumes of cables. These systems are crucial in industrial settings where cable and Wire management is essential for safety and efficiency.
Heavy-Duty Cable Trays
- Description: Heavy-duty cable trays are designed for large-scale installations that require the support of high-capacity cables.
- Benefits: These trays are durable and can support large cables, making them ideal for electrical, telecommunication, and data systems.
- Features: Heavy-duty trays can be installed on walls, ceilings, or floors, with materials that can endure industrial environments, such as exposure to chemicals or extreme temperatures.
- Applications: These trays are commonly used in industrial plants, large commercial buildings, and manufacturing facilities where heavy-duty cable management is needed.
Material and Finish Options
- Description: Cable trays come in a variety of cable tray material types, such as steel, aluminum, and fiberglass, with several finish options like powder-coated or galvanized coatings.
- Benefits: Different materials are chosen based on environmental conditions like moisture, chemical exposure, or temperature extremes. For example, galvanized steel provides extra durability against corrosion.
- Applications: Choosing the right material ensures the performance cable tray system performs optimally and lasts longer in the environment it’s installed in.
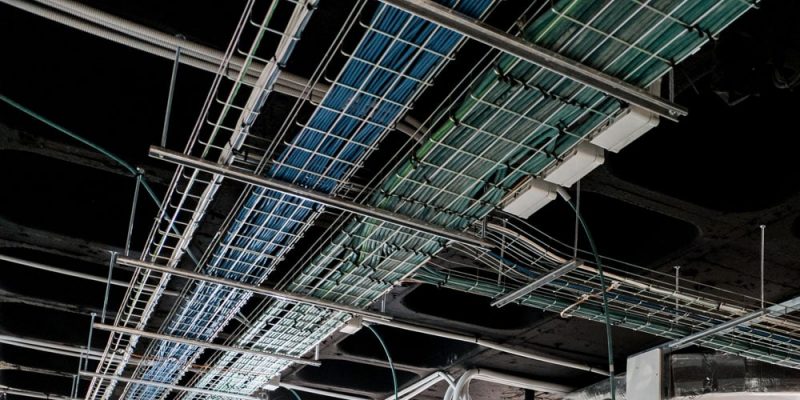
Cable Tray and Support Systems: Cable Tray Electrical Applications
Cable tray and support systems are essential in electrical installations, offering structured pathways for routing and protecting cables. They improve organization, reduce mechanical stress, and support future upgrades or maintenance. Their open design allows easy access and better airflow, helping to extend cable life and maintain system efficiency in commercial, industrial, and data center environments.
Functionality
Cable trays support and organize electrical wiring, preventing tangles, damage, and bending stress. By lifting cables off structural surfaces, they improve safety and accessibility while extending cable lifespan. The open design allows for easy maintenance, faster troubleshooting, and effective heat dissipation, especially in dense cable installations like control rooms or telecom spaces.
Standards Compliance
Cable tray systems must comply with standards such as NEC and IEC, which define material use, tray sizing, and installation practices. Following these regulations ensures safety, minimizes fire risk, and guarantees system reliability. Proper compliance also helps meet inspection requirements and avoid costly code violations in both local and international installations.
Electrical Safety
Cable trays enhance electrical safety by supporting proper grounding or providing non-conductive options like fiberglass trays. These systems help prevent electrical shocks, shorts, and equipment damage. Grounded trays safely manage fault currents, while FRP trays eliminate conductivity, making them ideal in high-risk or corrosive environments where insulation and protection are critical.
Enhanced Installation Efficiency and Maintenance
Compared to conduit systems, cable trays simplify installation and reduce labor. Their modular design allows quick layout changes and easy cable routing. During maintenance, open access enables fast identification and repair without disturbing surrounding systems, minimizing downtime and keeping facilities running efficiently with minimal disruption.
Tips for Calculating How Many Cables Fit in a Tray
Choosing the Right Cable Tray and Support Systems
Selecting the appropriate cable tray and support systems is a critical decision in any electrical or communication infrastructure project. The right system not only ensures safety and regulatory compliance but also enhances performance, supports future scalability, and reduces long-term maintenance costs. A well-chosen cable tray system adapts to environmental challenges, installation complexity, and operational demands. Below are the key factors to consider when selecting the most suitable solution for your project:
Load Capacity
Load capacity is one of the most important technical considerations when choosing a cable tray. The system must support the cumulative weight of the installed cables, as well as accommodate future additions. Underspecifying the load capacity can lead to sagging trays, damaged cables, or even complete system failure. When assessing capacity, consider cable type (e.g., power, control, fiber optic), tray span, and the total number of cables. Engineers should refer to published load charts and allow for a safety margin to ensure structural integrity over the system’s lifespan.
Tray Size and Dimensions
Selecting the right tray width and depth is essential to maintaining cable integrity and ensuring ease of access. An undersized tray may cause cables to be tightly packed, leading to overheating, wear, or difficulty during maintenance. On the other hand, oversizing may waste valuable space and increase installation costs. Consider the number and size of cables, the complexity of cable routes, building layout, and available installation space. A properly sized tray should also maintain a recommended fill ratio, allow sufficient airflow for heat dissipation, and support efficient cable routing for future upgrades.
Material Type and Durability
Material selection directly impacts the tray’s durability, corrosion resistance, and suitability for the installation environment. Common materials include galvanized steel, aluminum, fiberglass-reinforced plastic (FRP), and stainless steel. Galvanized steel is strong and economical; ideal for dry indoor settings. Aluminum is lightweight and corrosion-resistant; suitable for outdoor and cleanroom applications. FRP is non-conductive and corrosion-resistant; ideal for chemical plants, water treatment facilities, or marine environments. Stainless steel is extremely durable with high resistance to corrosion, heat, and chemical exposure; ideal for demanding industrial environments, although it comes at a premium cost. The operating conditions—such as humidity, temperature extremes, chemical exposure, or electromagnetic interference—should drive your material choice.
Support System Compatibility
Cable trays rely on a properly matched support system to maintain structural alignment and prevent stress on the tray and cables. Support types include wall-mounted brackets, trapeze supports, floor stands, and ceiling-hung suspension systems. Choose between fixed and adjustable supports based on the environment and flexibility needed. Adjustable supports are useful in dynamic environments where layout changes may be required, while fixed systems offer greater stability. Supports must be spaced correctly to avoid tray sag and ensure consistent cable alignment.
Accessibility and Maintenance
Ease of maintenance is often overlooked during design but can significantly impact long-term performance and operating costs. Select cable tray designs that allow straightforward access to cables for inspection, upgrades, or fault resolution. Options such as hinged covers, removable lids, and open-top designs provide better accessibility. Planning for service access not only reduces downtime during repairs but also improves the speed and safety of maintenance procedures, especially in mission-critical systems such as data centers or control rooms.
Compliance with Industry Standards
A quality cable tray system must comply with relevant codes and industry standards to ensure safety and legality. These include the National Electrical Code (NEC), Underwriters Laboratories (UL) listings, and International Electrotechnical Commission (IEC) standards. These frameworks specify acceptable materials, load ratings, grounding requirements, and installation practices. Ensuring compliance mitigates the risk of system failure, protects personnel, and simplifies the permitting and inspection process. Non-compliant installations may result in legal liabilities or costly retrofits.
Environmental Considerations
Environmental conditions heavily influence material choice, design, and installation techniques. In areas with high humidity, salt spray, corrosive gases, or extreme heat, specialized materials like stainless steel or FRP are often required. For outdoor installations, UV-resistant coatings or weatherproofing measures are critical to prevent material degradation. In high-risk environments such as refineries or processing plants, fire-rated trays or non-combustible materials may be mandated. Careful evaluation of the physical environment ensures that the tray system will maintain its integrity and functionality over time.
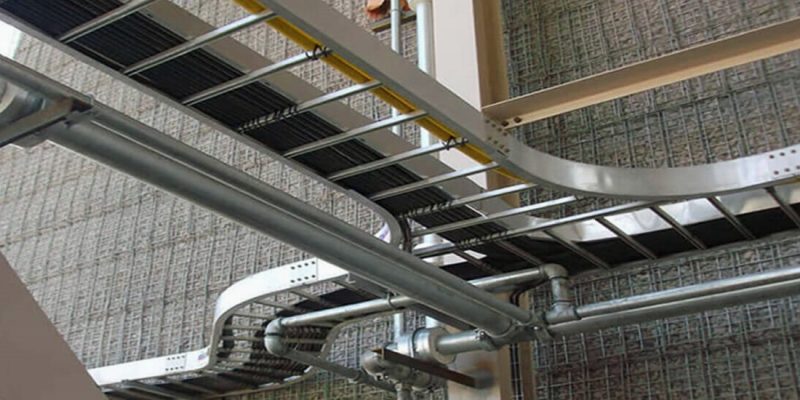
FAQs about Cable Tray and Support Systems
Cable tray systems rely on various types of support to maintain their stability and functionality. The most common support types include universal supports, strut supports, beam mount brackets, and hold down clamps.
Universal Supports are versatile and can be adjusted to accommodate different tray sizes and configurations. They are durable and compatible with various mounting options, making them suitable for both industrial and commercial applications.
Strut Supports are heavy-duty supports made from steel, ideal for elevated installations. They provide excellent stability, especially in large-scale installations where additional strength is required.
Beam Mount Brackets are designed to attach cable trays directly to beams, ensuring secure overhead installations. These brackets are adjustable and can be used in factories or warehouses where high, secure support is necessary.
Hold Down Clamps are used to secure cables within the tray, preventing them from shifting. This is particularly important in environments with high vibration, such as manufacturing plants, where cable movement could lead to damage or disorganization.
Each support type plays a key role in ensuring the stability, safety, and longevity of cable tray systems in various settings.
The frequency with which a cable tray should be supported depends on several factors, including the size of the tray, the weight of the cables, and the installation environment. As a general rule, cable trays should be supported every 5 to 10 feet (1.5 to 3 meters) along their length. However, specific installation guidelines and codes, such as the National Electrical Code (NEC) or local building regulations, should always be followed to determine the exact support intervals for a given installation.
In certain environments where heavier cables or longer trays are used, additional support may be needed more frequently. For instance, industrial applications that involve heavy-duty cable trays carrying large cables might require more frequent supports to prevent sagging or stress on the tray. Additionally, environmental factors such as vibrations, temperature fluctuations, and exposure to moisture can also influence how often a tray should be supported.
Proper support ensures that the tray and cables remain secure, minimizing the risk of damage and ensuring the long-term functionality of the system.
Cable tray systems are structural frameworks designed to support and organize electrical cables and communication wires within buildings or industrial facilities. These systems are typically composed of trays, supports, and accessories that collectively allow cables to be routed, protected, and easily accessible for maintenance or future expansion. Cable trays come in various designs, including ladder trays, enclosed trays, wire mesh trays, and solid-bottom trays, each serving different needs based on the application and environment.
Cable tray systems help maintain the organization of wiring, which can improve safety by preventing tangling or accidental damage. They also promote efficient airflow around cables, reducing the risk of overheating. Moreover, cable tray systems simplify the installation of new cables or the replacement of existing ones without requiring extensive rewiring.
These systems are commonly used in industrial, commercial, and residential installations where reliable cable management is essential. By providing a structured and secure method for managing cables, cable tray systems help ensure the safety, reliability, and longevity of electrical systems.
A cable support system is a framework designed to securely support, suspend, or route cables and wires in various installation environments. These systems play a crucial role in maintaining the integrity of electrical and telecommunication systems by ensuring that cables are properly secured, organized, and protected from potential damage.
Cable support systems can include cable trays, cable ladders, cable raceways, brackets, clamps, and other accessories. The purpose of these systems is not only to support the weight of the cables but also to provide pathways for easy cable routing, promote ventilation, and allow for future cable additions or modifications. They are essential for reducing the risk of cables becoming damaged due to bending, vibration, or exposure to environmental factors.
In addition to cable trays, support systems may also involve specific hardware for mounting and securing cables to ceilings, walls, or other structural elements. Proper installation of a cable support system ensures compliance with safety standards and enhances the overall efficiency and longevity of electrical systems.
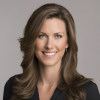
As the editor of GangLong Fiberglass, I have years of experience and in-depth research, focusing on cable tray products, fiberglass solutions, and grille systems. I incorporate years of industry insights and practical experience into every content, committed to promoting the progress of the industry. At GangLong Fiberglass, my commitment is reflected in every product, from innovative cable trays to durable fiberglass solutions and sturdy grille systems. As an authoritative voice in the industry, my goal is to provide valuable information to professionals and businesses and promote forward-looking solutions.