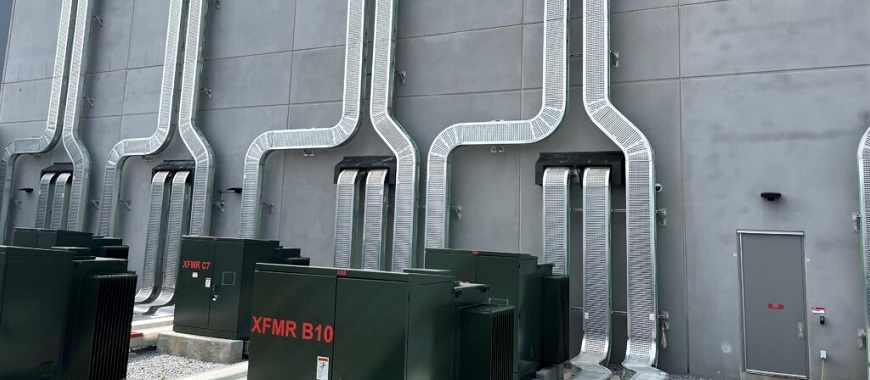
GangLong Fiberglass cable tray containment organizes and secures cables, ideal for 12A/12B commercial, data center, and solar installations. This comprehensive system of trays, supports, and accessories provides a dedicated pathway to route, protect, and neatly organize electrical, telecommunications, and data cables in both commercial and industrial environments, guarding against physical damage, overheating, and fire hazards while optimizing space; it also facilitates maintenance and future upgrades, ensures compliance with standards like the NEC by improving airflow and minimizing electromagnetic interference through clear separation of power and data lines, and ultimately enhances system reliability, extends cable lifespan, and reduces costly replacements.
Why Cable Tray Containment Matters
Cable tray containment is the backbone of robust electrical and telecommunications systems, offering integrated trays, brackets, and accessories that define clear pathways for power and data cables. By minimizing installation errors, optimizing airflow, and accommodating modular reconfiguration, this solution enhances heat dissipation, safety, and accessibility. Constructed from corrosion-resistant materials, it supports maintenance, expansion, and compliance with industry standards worldwide.
Organized Cable Routing
By offering predefined pathways and divider accessories, cable trays prevent cables from becoming tangled or overlapped. This structured routing not only keeps high-voltage power lines and low-voltage data cables neatly separated but also makes it far easier for installers and technicians to label, trace, and re-route individual conductors. The end result is a system that scales gracefully—adding new circuits or reassigning existing ones can be completed quickly without disrupting the entire network.
Robust Physical Protection
Cables in exposed industrial or commercial environments face risks ranging from accidental impacts (for example, moving equipment) to environmental challenges like moisture, dust, and temperature extremes. Packaging cable tray in sturdy, weather-resistant crates ensures sections arrive intact and ready for installation. Fiberglass or metallic trays then form a rigid barrier that absorbs shocks and shields conductors from abrasion, UV exposure, and corrosive substances. This protection greatly reduces the likelihood of insulation damage, short circuits, and unplanned downtime caused by cable failures.
Enhanced Safety and Reduced Hazards
Properly installed cable tray systems ensure adequate spacing between conductors, which helps prevent heat buildup and lowers the chance of electrical arcing. Keeping cables off floors and out of walkways eliminates trip hazards for personnel. In addition, separation of power and data cables within the same tray—using dividers or separate compartments—minimizes electromagnetic interference (EMI), leading to safer, more reliable operation of sensitive equipment.
Simplified Maintenance and Future Upgrades
When cables are laid out in an accessible tray system, routine inspections become a matter of visual checks rather than invasive disassembly. Technicians can easily pull out or add individual cable runs, test sections of the network, and replace damaged segments without shutting down entire areas. This agility translates into shorter service windows and lower labor costs, particularly in mission-critical facilities like data centers where uptime is paramount.
Code Compliance and Risk Mitigation
Adhering to standards such as the National Electrical Code (NEC) isn’t just a regulatory checkbox—it directly impacts operational safety. Cable trays designed and installed per NEC guidelines ensure correct support intervals, grounding practices, and conductor separation, all of which reduce fire risk and electrical faults. By meeting or exceeding these requirements, organizations protect both personnel and equipment, while also avoiding potential fines or insurance complications associated with non-compliant installations.
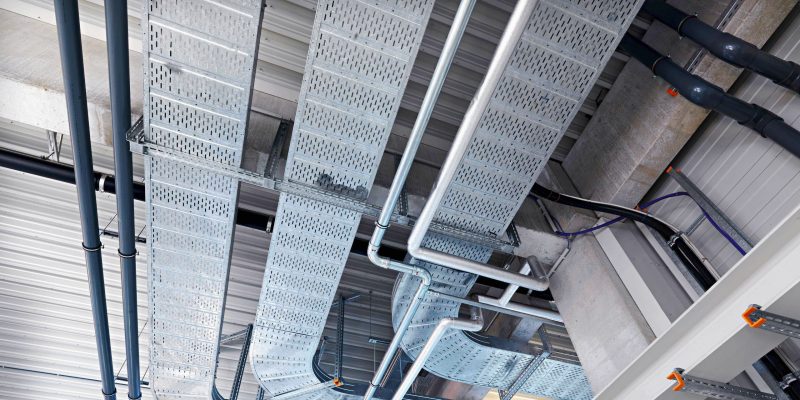
Efficient Cable Tray Sealing System for Industrial Applications
Overview of Cable Tray Containment Types
Effective cable tray containment management systems provide solutions for organizing and protecting power and data cables in commercial and industrial environments. By choosing materials and designs—solid-sided trays for protection or ladder-style systems for heat dissipation—engineers can optimize performance, ensure compliance, and simplify maintenance. This overview compares key containment options, their applications, and benefits to guide infrastructure decisions.
Containment Type | Construction / Materials | Typical Applications | Key Features / Benefits |
---|---|---|---|
Ladder Tray | Carbon steel (galvanized or powder-coated), stainless steel; two side-rails with open rungs | Medium- to heavy-duty power/control runs in data centers, factories | Excellent heat dissipation; high load‐capacity; easy access |
Perforated Tray | Carbon steel or aluminum alloy; bottom and sidewalls with punched holes | General electrical wiring in commercial buildings, panels, control rooms | Good ventilation; supports small cables; cleaner appearance |
Solid-Bottom Tray | Carbon steel or stainless; fully closed bottom | Dust- or moisture-sensitive areas (chemical plants, food processing) | Full protection against contaminants; adds mechanical shielding |
Wire-Mesh Basket | Welded galvanized or stainless steel wire mesh | High-density small-cable runs (telecom rooms, LAN closets) | Ultra-lightweight; very flexible; rapid installation |
Covered Tray | Any tray type with snap-on/hinged PVC or metal cover | Where splash, dust or rodent protection is required (outdoors, warehouses) | Encloses cables without need for conduit; easy access via cover |
Cable Raceway / Duct | Rigid PVC, steel or aluminum extrusions; often with snap-on covers | Surface-mount wiring in offices, labs, control panels | Neat appearance; simple add-on/flex extensions; good segregation |
Conduit (optional) | Steel or PVC tubing (rigid or flexible) | Final terminations, exposed walls, hazardous areas | Total mechanical protection; meets stringent fire/impact codes |
Choosing Between Duct Back vs Cable Tray Systems
Key Components of a Cable Tray Containment Kit
Cable Tray Systems Overview
A typical electrical containment tray kit consists of modular components that can be assembled to meet specific cable management needs. These systems are versatile, customizable, and can be adapted to different building layouts and cable management requirements. The major components of a cable tray system include trays, brackets, supports, covers, and connectors.
- Modular System: Includes trays, supports, and brackets that can be customized for a variety of applications.
- Versatility: Flexible configurations for different environments, from simple cable runs to complex installations.
- Easy Installation: Can be installed with minimal effort and adapted to any building structure.
Cable Tray Containment Kit Features
A comprehensive cable tray containment kit contains:
- Tray Sections: Available in different sizes and materials to suit specific cable management needs.
- Connectors: To join tray sections and create custom layouts.
- Bends & Reducers: To change the direction of the trays or accommodate different cable sizes.
- Junction Boxes: Used for transitioning between different types of trays or connecting multiple systems.
- Accessories: Include cable cleats, firestops, grounding solutions, and other safety features.
Choosing the Right Cable Tray Kit
When selecting a cable tray containment kit, it’s essential to consider:
- Material: Steel, aluminum, fiberglass—each offers different durability, resistance, and weight capacities.
- Load Capacity: Ensure the system can support the required number of cables.
- Environmental Conditions: Consider factors like moisture, temperature extremes, and exposure to chemicals.
- Safety Requirements: Make sure the system complies with industry standards and is suitable for the type of installation.
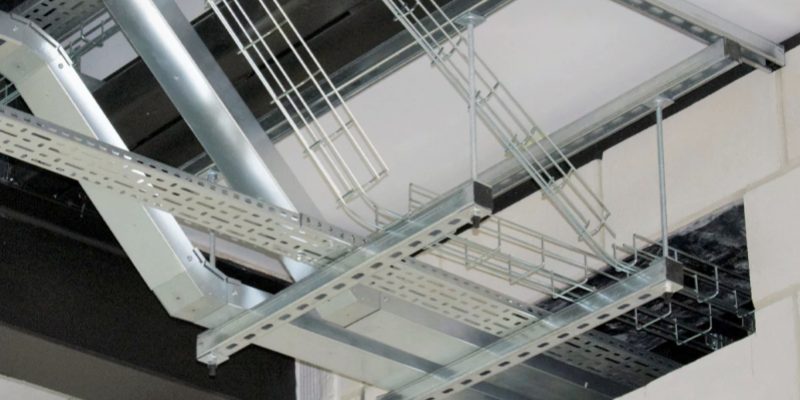
Leading Cable Tray Manufacturers
GangLong Fiberglass Cable Tray Systems
At GangLong Fiberglass, we manufacture high-grade fiberglass cable tray containment solutions tailored for commercial and industrial applications. Our product line includes solid-bottom, ventilated, and ladder-style trays—each engineered to streamline cable routing, improve heat dissipation, and resist corrosion, UV exposure, and chemical attack. Designed for quick installation and easy future expansion, our trays keep power and data cables neatly organized and fully protected. Backed by rigorous in-house testing and compliance with NEC, IEC, and IEEE standards, we deliver unmatched durability, safety, and performance—even in the harshest environments.
Product Range: Steel, Aluminum, and Fiberglass Trays
GangLong offers a comprehensive range of cable trays, including fiberglass, steel, and aluminum options. Each material is carefully selected to meet specific needs based on factors such as environmental conditions, load capacity, and cost-effectiveness. Fiberglass trays, in particular, are ideal for corrosive environments, as they are resistant to chemical damage, moisture, and extreme temperatures, making them a preferred choice for industries that require high corrosion resistance. Steel trays offer exceptional strength and support, while aluminum trays provide a lighter, more cost-effective alternative without sacrificing durability.
Applications: Telecommunications, Industrial Manufacturing, Power Distribution
GangLong cable tray systems are designed for use across a variety of sectors, including telecommunications, industrial manufacturing, and power distribution. In the telecommunications industry, these trays help manage vast networks of wiring, ensuring that cables are routed safely and efficiently. In industrial manufacturing plants, where cables are subjected to heavy-duty use and environmental stress, GangLong trays provide robust protection to minimize the risk of cable damage. For power distribution systems, their trays ensure safe and organized routing of high-voltage cables, reducing the risk of overheating and electrical failures.
Benefits: Durability, Customization, and High Safety Standards
The benefits of GangLong’s fiberglass cable tray systems are numerous:
- Durability: GangLong trays are built to withstand the toughest conditions, from extreme temperatures and humidity to exposure to chemicals and UV rays. This makes them an ideal choice for both indoor and outdoor installations.
- Customization: GangLong understands that every project has unique requirements. They offer customizable solutions, allowing businesses to tailor their cable tray systems based on the layout, load capacity, and environmental factors specific to their industry.
- High Safety Standards: GangLong places a strong emphasis on safety, designing their cable tray systems to meet or exceed international safety standards. This includes fire-resistant coatings, effective grounding solutions, and optimized cable spacing to prevent overheating and electrical hazards.
GangLong’s fiberglass cable tray systems offer a combination of strength, flexibility, and reliability, making them a preferred choice for industries looking to ensure the safe, efficient, and long-lasting management of their cable infrastructure. Whether you are working in telecommunications, power generation, or manufacturing, GangLong provides the ideal solution for your cable containment needs.
Key Benefits of a Free Standing Cable Tray System
How to Select the Best Cable Tray Containment System
Determining the Right Tray for Your Project
When selecting the best cable tray containment system, consider:
- Cable Type: Different cables (power, data, control) may require different tray designs and materials.
- Location: Is the system installed indoors or outdoors? This affects material choice and design.
- Environmental Factors: Consider temperature, humidity, and exposure to chemicals.
- Compliance: Ensure the system meets the safety requirements outlined by NEC or other local regulations.
For projects that require both functionality and design flexibility, decoduct cable tray systems are an excellent choice. These trays are versatile and can be adapted to various cable types and environmental conditions, making them suitable for both indoor and outdoor installations.
Load Capacity and Cable Tray Sizing
Properly sizing a cable tray is critical for preventing overheating and damage to cables. Use NEC fill values to determine the optimal tray size and ensure that trays are not overfilled. Clearance requirements should also be adhered to for safe installation.
- Ensure Proper Sizing: Avoid overloading trays to prevent safety hazards.
- Follow NEC Standards: NEC guidelines help ensure that cable trays are filled correctly, reducing fire risks and maintaining system integrity.
Aesthetic and Space Considerations
Cable trays should be selected with space and design in mind, especially in commercial environments. Compact or low-profile systems can blend into the overall design without compromising functionality.
- Design Considerations: Choose trays that match the aesthetics of the building, especially in visible areas.
- Space Efficiency: Use slim or modular trays that take up less space without sacrificing capacity.
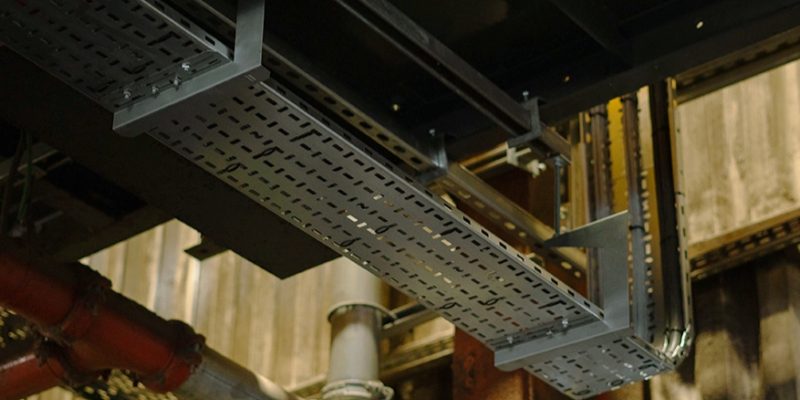
FAQs about Cable Tray Containment
Cable containment refers to the system of physical enclosures and supports used to route and protect electrical cables in buildings, industrial facilities, and other infrastructures. These systems are essential for organizing and managing cables while ensuring safety and efficiency in electrical installations. The primary components of a cable containment system include cable trays, ladders, baskets, and conduits, which help to separate, support, and shield cables from physical damage, heat, and environmental factors.
Cable containment is crucial in preventing the risk of fire, improving cable access for maintenance, and reducing the risk of electrical failures. The systems can be customized depending on the type of cables, environmental conditions, and space constraints, ensuring that cables are installed in an efficient, organized manner.
Cable containment systems also play an important role in compliance with safety standards like the NEC (National Electrical Code), which regulates the installation of electrical wiring and components in commercial and industrial buildings. Proper cable containment ensures a longer life for the cables and minimizes the need for frequent replacements.
Tray cable is designed for use in cable trays, but it does not necessarily need to be installed within conduit, depending on the environment and the type of tray system used. Tray cable (also known as Type TC cable) is specifically rated for installation in open, accessible spaces like cable trays, ladders, and raceways, without the added protection of conduit. However, there are certain conditions under which conduit may be necessary.
For example, tray cable might need to be enclosed in conduit when it is installed in areas that are exposed to harsh environmental conditions, such as extreme moisture, chemicals, or physical impact. This is especially true in hazardous locations or areas where the cable might be subject to mechanical damage or interference.
In general, whether tray cable needs to be in conduit will depend on several factors including:
Environmental conditions: In outdoor or wet locations, conduit may be required for extra protection.
Building codes: Local electrical codes, like the NEC, may mandate conduit in certain installations for added safety.
Type of installation: For cables running through walls, ceilings, or floors, it may be necessary to use conduit for additional protection.
Ultimately, while tray cable can often be used without conduit, it’s essential to follow safety guidelines and local building codes when determining the appropriate installation method.
Installing cable trays involves several critical safety procedures to ensure both the safety of the workers and the long-term effectiveness of the system. The following guidelines are commonly followed during installation:
Follow Manufacturer Instructions: Always adhere to the manufacturer’s guidelines for installation, including proper spacing, support, and bending of trays.
Use Personal Protective Equipment (PPE): Workers should wear appropriate PPE, such as hard hats, gloves, safety glasses, and steel-toed boots, to protect against injury during installation.
Ensure Proper Support: Cable trays should be adequately supported to prevent sagging or potential damage. This includes using appropriate brackets, hangers, and supports according to the weight and size of the cables to be contained.
Avoid Overloading: Overloading cable trays can lead to overheating, which is a significant fire risk. Always ensure that the tray is installed with adequate clearance and that the total fill does not exceed the recommended limits, as outlined by the National Electrical Code (NEC).
Maintain Clearance: Adequate clearance around the tray is crucial to ensure proper airflow and prevent heat accumulation, which could damage cables or lead to fire hazards.
Grounding and Bonding: Cable trays must be properly grounded and bonded to prevent electrical hazards, including potential shock or arcing. This is especially important in industrial settings where high-voltage cables are used.
Fire Protection: For installations passing through fire-rated walls or ceilings, ensure that appropriate firestops are installed to prevent the spread of fire through the trays.
Inspection: Once installed, cable trays should be inspected to ensure all components are secure, and cables are properly routed, with no signs of wear or damage.
Following these safety procedures ensures that cable tray systems are installed correctly, reducing the risk of electrical hazards and ensuring compliance with safety codes.
Calculating cable containment involves determining the appropriate size of the cable tray or containment system to accommodate the total volume of cables while maintaining proper spacing, airflow, and safety. This calculation takes into account several factors:
Cable Type and Size: The type of cables being routed, their diameters, and insulation types play a key role in determining the required space in the tray. For example, large power cables will require more space than smaller data cables.
Tray Dimensions: The width, height, and depth of the tray should be considered when calculating capacity. Trays are available in various sizes, and selecting the right dimensions ensures cables fit comfortably while leaving enough space for future expansion.
Fill Capacity: The National Electrical Code (NEC) provides guidelines for the maximum fill capacity of cable trays. The maximum fill is typically a percentage of the tray’s cross-sectional area—usually around 50% for a single layer of cables. This allows for sufficient airflow and reduces the risk of overheating.
Airflow Requirements: Proper ventilation is essential to prevent heat buildup, especially in environments with high cable density or where cables are transmitting high-voltage power. Ensure there is adequate airflow space around the cables in the tray.
Environmental Conditions: Environmental factors such as temperature, humidity, and the potential for mechanical damage also affect the type of tray and clearance required for safe cable containment. In wet or hazardous environments, you might need to choose trays with extra protection or corrosion resistance.
Regulatory Compliance: Ensure the installation complies with local codes and industry regulations. This includes following the NEC’s guidelines for spacing, grounding, and fire safety.
To calculate the appropriate size and type of cable containment system, you can use specialized software or manual formulas based on the above factors. It’s always best to consult with an experienced electrician or engineer to ensure your calculations meet safety standards and provide sufficient capacity for the system’s long-term needs.
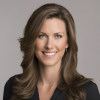
As the editor of GangLong Fiberglass, I have years of experience and in-depth research, focusing on cable tray products, fiberglass solutions, and grille systems. I incorporate years of industry insights and practical experience into every content, committed to promoting the progress of the industry. At GangLong Fiberglass, my commitment is reflected in every product, from innovative cable trays to durable fiberglass solutions and sturdy grille systems. As an authoritative voice in the industry, my goal is to provide valuable information to professionals and businesses and promote forward-looking solutions.