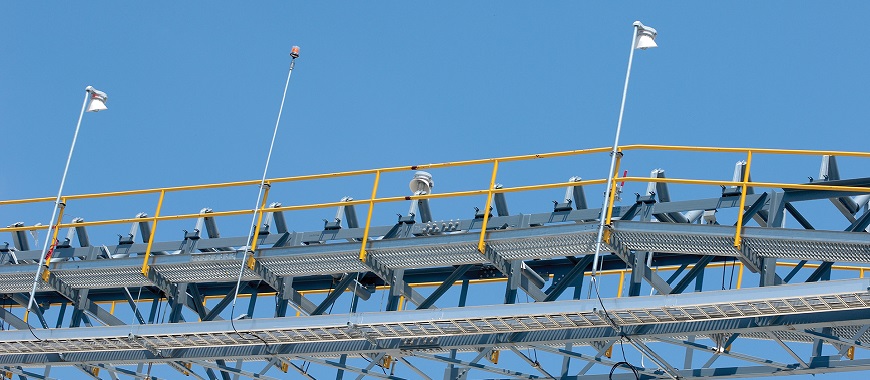
Cable tray segregation plays a crucial role in ensuring the safety and performance of electrical systems. It involves the organized separation of different types of cables within a cable tray, such as power cables, control cables, and communication cables. This segregation helps to prevent electrical interference, signal degradation, and potential safety hazards. Proper cable tray segregation is not just about keeping cables apart — it’s about ensuring that each cable type operates optimally without affecting the others. For example, power cables can generate electromagnetic interference (EMI) that could disrupt the functioning of sensitive signal cables, such as analog or digital control wires. By maintaining adequate segregation, it is possible to improve signal integrity, reduce the risk of equipment malfunction, enhance heat dissipation, and meet critical industry safety standards. Ultimately, cable tray segregation is essential to creating a safe, efficient, and reliable electrical installation.
What is Cable Tray Segregation?
Definition of Cable Tray Segregation
Cable tray segregation is a critical practice in cable management that involves physically separating cables within a cable tray based on their specific electrical characteristics. These characteristics include the cable’s function (e.g., power, control, or communication), voltage level, current-carrying capacity, and the type of signal transmitted. The goal of segregation is to create a clear distinction between cables that could otherwise interfere with one another, particularly when power cables are run alongside sensitive low-voltage control or data cables.
In cable tray systems, power cables and signal cables (e.g., analog, digital, or instrumentation cables) often coexist. Without appropriate segregation, electromagnetic interference (EMI) from power cables, which can carry high currents or voltages, may distort or degrade the signals in nearby cables. This interference can lead to data loss, communication errors, or even malfunctioning equipment. Therefore, segregating cables effectively ensures that each cable type performs optimally and reduces the risks of hazardous faults.
Purpose of Cable Tray Segregation
The purpose of cable tray segregation extends beyond just preventing physical tangling of cables—it aims to enhance the operational safety, performance, and lifespan of electrical systems. Power cables, especially those carrying large currents or high voltages, can emit strong electromagnetic fields that disrupt the signals in control or communication cables placed too close. This interference, also known as crosstalk, can cause signal distortion, data corruption, or even failure of critical systems, particularly in sensitive equipment like instrumentation or control systems.
To mitigate these risks, the segregation of cables within the tray ensures that cables with incompatible functions are physically separated. By doing so, the integrity of low-voltage control cables, data transmission cables, and instrumentation cables is preserved, ensuring they transmit signals without interference from high-power cables. Moreover, proper segregation prevents accidental short circuits or overloads by isolating cables with different voltage levels, making the installation safer.
In addition to reducing interference, segregated cable tray is essential for complying with industry standards such as the National Electrical Code (NEC) and the Canadian Electrical Code (CEC). These codes often mandate specific separation requirements, especially in environments with high voltage cables or sensitive electronic systems. By adhering to these requirements, companies can avoid violations that could lead to costly repairs, operational downtime, or safety hazards.
Segregation also aids in long-term system maintenance and troubleshooting. With clearly separated cables, maintenance teams can quickly identify and address issues without confusion or the risk of cross-wiring. Additionally, proper segregation allows for easier cable upgrades, expansions, or replacements, as cables are systematically organized based on their requirements.
Key Benefits of Cable Tray Segregation
- Prevention of Electromagnetic Interference (EMI): Isolating high-voltage power cables from low-voltage control and signal cables helps prevent the induction of unwanted electrical signals, maintaining clear data and control transmission.
- Improved Safety: Proper segregation reduces the risk of short circuits, accidental cross-wiring, or electrical faults that may arise from improperly placed cables with differing voltage levels.
- Enhanced Cable Lifespan: Minimizing electrical interference ensures that both power and signal cables remain free from the wear and tear caused by electromagnetic disruptions, thus increasing their operational lifespan.
- Compliance with Electrical Standards: Segregation ensures adherence to safety standards and codes, reducing the risk of regulatory fines and enhancing the safety of electrical installations in industrial and commercial environments.
- Easier Maintenance and Troubleshooting: Segregated cables are easier to manage, inspect, and maintain, allowing for quicker fault detection and more efficient troubleshooting. By incorporating decoduct cable trays, the process is further streamlined, as these trays provide a structured and organized pathway for cables. Their design ensures clear visibility and accessibility, making it simpler to identify specific cables, reduce downtime during maintenance, and enhance the overall efficiency of troubleshooting efforts.
- Facilitation of Future Upgrades: Proper cable organization through segregation allows for easy future expansion or modification of the system, without the need for re-cabling or substantial reconfiguration.
Cable tray segregation plays a vital role in ensuring the safety, performance, and longevity of electrical installations, especially in environments where multiple types of cables coexist within the same tray. By implementing effective segregation practices, you protect your systems from electrical interference and ensure optimal functionality across all types of cables.
Essential Features of Cable Tray Expansion Plates
Types of Cable Tray Segregation
Physical Separation in Cable Tray Segregation
Physical separation is one of the most commonly used methods for cable tray segregation. This approach involves the use of physical barriers or dividers within the tray to separate different types of cables, preventing them from coming into direct contact with each other. These dividers can be made from a variety of materials, including metal (such as aluminum, steel, or stainless steel) and non-metallic options like plastic or fiberglass. The choice of material depends on the specific needs of the installation, including environmental conditions, the type of cables involved, and the required durability.
By creating distinct, physically separated sections within the cable tray, physical separation ensures that high-power cables are kept away from low-voltage data and control cables. This isolation prevents a number of potential hazards, such as short circuits, signal interference, or accidental contact between cables of different voltage classes. For example, power cables running high-voltage currents can generate electromagnetic fields that may disrupt the signals in nearby sensitive data or control cables. Physical barriers within the tray serve to minimize this risk by keeping these cables apart.
Physical separation also helps to optimize the cable tray system’s organization and maintenance. With cables properly separated, it becomes easier to identify and replace faulty cables, expand the system, or troubleshoot issues without causing accidental disruptions to other cables.
Electrical Separation in Cable Tray Segregation
Electrical separation focuses on preventing electromagnetic interference (EMI) and other forms of electrical disruptions that can occur when cables carrying different voltages or signal types are installed too close together. In installations where both power and control cables are present, it’s essential to keep high-voltage cables at a safe distance from low-voltage cables, especially those used for sensitive applications like instrumentation or communication.
High-voltage power cables often emit electromagnetic fields due to the flow of large currents, which can induce voltage in nearby signal cables. This can result in signal distortion, data loss, or malfunctioning of equipment that depends on precise data transmission. Electrical separation is typically achieved in two ways: maintaining physical distance between cables or using shielding techniques such as metal barriers or conductive materials around sensitive cables.
- Maintaining Distance: One of the simplest forms of electrical separation is ensuring sufficient spacing between cables based on voltage level. This helps to reduce the electromagnetic coupling between the cables, thus protecting sensitive data transmission or control systems from interference. Electrical codes like the NEC (National Electrical Code) provide guidelines on the minimum distance between high-voltage and low-voltage cables to prevent such disturbances.
- Shielding: In environments where spacing is limited or electromagnetic interference (EMI) is particularly high, using shielding materials or metallic barriers around sensitive cables can effectively block the EMI from reaching them. For example, shielding cables with grounded metallic layers or using metal dividers within the tray can provide a further layer of protection for sensitive instrumentation or communication cables.
Electrical separation is especially crucial in mission-critical installations, such as control rooms, medical facilities, or industrial plants, where the integrity of signals and data is paramount to the system’s performance and safety.
Environmental Considerations in Cable Tray Segregation
Environmental factors play a significant role in determining the best method for cable tray segregation. These factors include ambient temperature, airflow, and the physical layout of the installation, which all influence how cables are spaced and separated within the tray. Effective segregation takes into account these environmental conditions to ensure that cables can operate efficiently and safely throughout their lifespan.
- Temperature and Airflow: In environments with high temperatures, such as power generation plants or manufacturing facilities, heat dissipation is a critical concern. Overheated cables can degrade faster and pose safety risks. Therefore, physical separation not only reduces electrical interference but also ensures that cables are spaced properly to allow for adequate airflow and cooling. Cable trays should be designed to maintain these airflow spaces, particularly when handling power cables that tend to generate more heat. For instance, power cables might require more space between them than low-voltage cables to support better heat dissipation.
- In environments with limited airflow or higher ambient temperatures, it may be necessary to incorporate additional cooling mechanisms, such as ventilation fans or air conditioning systems, to help regulate cable temperatures. Proper segregation of cables in such environments will not only help in cooling but also prevent overheating, which could lead to potential system failures or fire hazards.
- Corrosion Resistance: In environments with high humidity or corrosive elements (e.g., coastal areas, chemical plants), the materials used for cable trays and dividers must be selected carefully. Aluminum is often a preferred choice due to its excellent corrosion resistance, ensuring that the dividers and trays maintain their structural integrity over time. On the other hand, for extremely corrosive environments, non-metallic dividers made from fiberglass or other specialized materials may be used, as they are impervious to moisture and can withstand harsh chemicals.
- Electromagnetic Interference (EMI) Concerns: In certain industrial environments, EMI can be a significant concern, particularly in locations with high-power cables or electrical machinery. In these cases, additional measures such as non-metallic dividers, rubber isolation pads, or specialized EMI shielding may be employed to ensure that cables, especially those used for data and control, remain unaffected by external electrical noise.
Effective discreate cable tray depends on a combination of physical separation, electrical separation, and a thorough understanding of the environmental factors at play. By taking these factors into account, cable trays can be configured to ensure safe, efficient, and reliable operation, preventing potential interference or hazards in a variety of industrial, commercial, and residential settings.
Cable Tray Segregation and Separation Requirements
NEC (National Electrical Code) and CEC (Canadian Electrical Code): Compliance with the National Electrical Code (NEC) and the Canadian Electrical Code (CEC) is crucial when designing cable tray segregation systems. Both codes provide clear guidelines for ensuring that power cables and communication cables are segregated to prevent interference and maintain safety.
- NEC Article 392: This article stipulates that power cables should not be installed in the same tray as communication or signal cables unless proper segregation is provided. This segregation could include physical barriers or specific spacing to prevent power cables from affecting the sensitive data or control cables. The objective is to ensure that the electrical and signal systems operate independently without compromising each other.
- Distance Requirements: The NEC and CEC also outline minimum distance requirements between different types of cables. For instance, the distance between power cables and signal cables should be enough to prevent induced voltage from high-voltage cables, which could interfere with low-voltage signals. These distance requirements vary depending on the cable’s voltage class, insulation type, and the environment in which the cables are installed.
- Special Considerations: In hazardous environments, such as Class I, II, Division 1 or 2 locations, segregation requirements are more stringent. These areas require additional safety precautions, such as explosion-proof barriers or additional physical barriers, to prevent potential ignition or interference. These specialized requirements are designed to ensure safety in environments with increased risk of hazardous conditions, such as flammable gases or dust.
Segregation of Power and Instrumentation Cables
The segregation of power cables from instrumentation and control cables is critical to maintaining the performance and reliability of electrical systems, particularly in environments where signal integrity is paramount. High-voltage power cables, especially those that carry large currents, can generate electromagnetic interference (EMI), which can adversely affect nearby low-voltage control and instrumentation cables. This interference can lead to signal degradation, data corruption, or complete system malfunctions. For example, in industrial automation systems, a small fluctuation or distortion in control signals can lead to significant operational issues, such as incorrect process control, equipment failure, or even safety hazards.
Proper segregation of power and control cables is essential to mitigate this risk. In practice, this can be achieved by using physical separation techniques, such as barriers or dividers within cable trays, to ensure that power cables remain isolated from sensitive signal cables. For instance, when power cables are routed alongside instrumentation cables without adequate segregation, the magnetic fields created by the power cables can induce voltages in the nearby control cables, leading to cross-talk or loss of data integrity. This is particularly crucial in control systems that rely on precise measurements and real-time data, such as temperature, pressure, or flow sensors in manufacturing processes or automation systems.
The segregation of power cables is essential in ensuring the safety of the overall electrical system. The proximity of high-voltage power cables to instrumentation and control cables increases the likelihood of accidental short circuits or electrical faults, especially in cases of cable damage or improper installation. By keeping power cables physically separated from low-voltage cables, the risk of short circuits, electrocution, or fire hazards is minimized.
In environments like data centers, industrial plants, and control rooms, where communication and control systems are critical to daily operations, proper segregation techniques preserve the functionality of these systems and ensure that they operate without interruption. The integrity of signal transmission is particularly important in sensitive sectors like telecommunications, healthcare, and power generation, where a disruption could have serious consequences. Therefore, adhering to best practices in cable segregation not only helps to protect the equipment but also contributes to overall operational safety and efficiency.
The proper segregation of power cables from instrumentation and control cables is an essential aspect of electrical system design. It plays a fundamental role in preventing EMI, ensuring data integrity, enhancing system safety, and maintaining the long-term reliability of critical control systems. Whether achieved through physical separation, electrical shielding, or maintaining adequate spacing, cable segregation is a key practice that supports the effective operation of industrial and communication systems.
Insert Plate for Cable Tray: Enhancing Cable Tray Performance
Cable Tray Segregation and Divider Requirements
Material Considerations
- Aluminum Tray Dividers: These dividers are lightweight, corrosion-resistant, and ideal for general-purpose installations where EMI shielding is not a primary concern. Aluminum dividers are often used in environments with mild conditions, providing an effective and cost-efficient solution for cable segregation.
- Steel Tray Dividers: Steel dividers offer greater strength and durability, making them suitable for industrial environments where physical protection is required. Steel dividers are often used in areas where there is a risk of mechanical damage or in hazardous locations that require enhanced protection for cables.
- Non-metallic Dividers: In environments where EMI needs to be minimized, non-metallic dividers are commonly used. These materials do not conduct electricity, providing an added layer of protection against interference. Non-metallic dividers are also preferred in highly corrosive environments where metal dividers may corrode over time.
Divider Design
- Height and Placement: The design and height of dividers are important factors in maintaining adequate segregation in cable tray divider installation. Dividers should be tall enough to keep cables physically separated but also allow for airflow to ensure effective cooling. Proper placement of dividers can also help optimize space within the cable tray and maintain separation across various layers of cables.
- Adjustable Dividers: Adjustable dividers offer flexibility in adapting to future needs. As new cables are added to a system, adjustable dividers can be repositioned to accommodate changes in the installation. This reduces the need for complete re-installation and provides a more cost-effective solution for growing systems.
Practical Aspects of Cable Tray Segregation
Distance Between Instrument Cables and Electrical Cables
One of the critical aspects of cable tray segregation is maintaining the correct distance between instrument cables (e.g., DO, AI, AO, and DI cables) and electrical power cables. High-voltage power cables, particularly those carrying substantial currents, can generate electromagnetic fields that induce voltage or electrical noise in nearby signal cables. This induced noise can significantly degrade the performance of sensitive instrumentation or control systems. For example, it can cause data corruption, false readings, or loss of control in automation processes. Ensuring the appropriate distance between power and signal cables helps prevent these issues and ensures the reliable operation of electrical systems.
The required distance between instrument cables and electrical power cables depends on several factors, including the voltage of the power cables, the type of signal cables, and the environmental conditions where the cables are installed. Power cables with higher voltage levels typically require a greater separation distance from signal cables to reduce the risk of interference. Similarly, cables that carry low-voltage or low-current signals (such as instrumentation and control cables) are more susceptible to noise and require careful placement. Environmental factors, such as the presence of electromagnetic interference (EMI) sources, ambient temperature, and airflow, also play a role in determining the ideal segregation distance.
It is essential to follow industry standards and manufacturer recommendations when establishing these distances. Codes such as the National Electrical Code (NEC) and the Canadian Electrical Code (CEC) provide guidelines on the minimum separation distances between power and signal cables to ensure both performance and safety. By adhering to these recommendations, you can prevent signal degradation and ensure the integrity of data transmission across the system.
Segregation in Long Cable Runs
In long cable runs, which can extend over hundreds of meters, maintaining proper cable segregation becomes even more critical. The risk of signal degradation increases with the length of the cable run, as the electromagnetic interference from power cables can accumulate over distance. This means that long cable runs, especially those running alongside high-voltage power cables, need to be carefully managed to prevent power cables from inducing harmful noise or interference in signal cables.
For long-distance installations, ensuring that cables are physically separated and that the appropriate distance is maintained is essential for preventing interference. As the distance between cables increases, the likelihood of signal degradation or loss increases due to the cumulative effects of EMI. In these situations, it may also be necessary to incorporate additional shielding for the signal cables or use cables with higher resistance to electromagnetic interference (EMI). This ensures that the integrity of the signal is preserved, even over long distances.
In addition to physical separation, regulatory standards such as NEC 800.133 and other local electrical codes provide detailed guidelines for cable segregation in long runs. Compliance with these standards not only ensures the safety of the installation but also ensures that the electrical system performs as expected, without interference or degradation of signals.
The use of dedicated cable trays, dividers, and isolation pads designed for long cable runs can further help maintain the segregation between power and signal cables. These physical barriers ensure that cables remain securely separated, even in expansive installations. Additionally, proper airflow management, including ventilation and heat dissipation, should also be considered in long cable runs to prevent overheating of cables, which can further exacerbate the risk of interference.
By taking these precautions and ensuring proper segregation in long cable runs, you can maintain the reliability and performance of the electrical system over time, even in complex and expansive installations.
Cable Tray Segregation: Layering and Ship Configuration
Layered Cable Tray Systems
In certain installations, cables are arranged in multiple layers within the same cable tray, a method commonly referred to as layered cable tray systems. This approach is typically used to maximize space and organize cables effectively in confined or crowded installations. However, careful planning is essential to maintain cable tray segregation across all layers, particularly when dealing with cables of varying functions, voltage levels, and susceptibility to electromagnetic interference (EMI).
When layering cables in a tray, the general rule is to position power cables in the lower layers of the tray, with signal and control cables placed above them. This arrangement helps minimize the risk of EMI, as power cables—particularly those carrying high voltages or large currents—can generate significant electromagnetic fields. By keeping power cables at the bottom, with signal cables above, the separation reduces the potential for power cables to induce noise or disturbances in the sensitive signals carried by the control and instrumentation cables.
Additionally, layered cable tray systems help improve the overall organization of cables, making it easier to trace individual wires, inspect them, and make future modifications or additions. Proper spacing between cables in each layer ensures that each cable is given enough room for heat dissipation, reducing the risk of overheating. Excessive heat build-up in tightly packed cables can lead to insulation degradation, potential short circuits, or fire hazards.
For optimal cable tray segregation, it’s essential to incorporate dividers or physical barriers between layers. These dividers can be made of metal, such as aluminum or steel, or non-metallic materials designed to minimize EMI. The dividers not only keep cables separated but also facilitate airflow, further enhancing the system’s ability to manage heat. Maintaining this careful separation and organization across all layers ensures the long-term performance and safety of the installation.
Ship Configuration
A ship configuration, also known as a stacked cable tray layout, refers to a method where cables are arranged vertically within a single cable tray, often referred to as a “stacked” configuration. This method is commonly used in environments with limited horizontal space but ample vertical space. The stacked cable tray design optimizes physical space, supporting large numbers of cables, but it presents challenges related to cable tray segregation.
In a ship configuration, the cables are stacked in layers, often with several different types of cables in the same tray. To ensure proper cable tray segregation, each layer of cables must be carefully planned, taking into account the type of cable, its function, and its voltage level. The risk in this configuration is that cables in different layers may inadvertently interfere with each other if proper separation isn’t maintained. For example, high-voltage power cables placed too close to low-voltage control cables can cause electromagnetic interference, leading to signal degradation or malfunction.
To address this, dividers or barriers are crucial in a ship configuration. These physical separations help maintain the integrity of cable tray segregation, preventing cables from touching or coming too close to each other. Dividers can be strategically placed between each layer of cables, effectively isolating power cables from sensitive instrumentation or data cables. This segregation reduces the risk of electrical noise or cross-talk between different cables and ensures that each type of cable functions correctly.
Additionally, proper spacing between layers is essential in a ship configuration to allow adequate airflow and prevent overheating. Heat can accumulate in stacked configurations if ventilation isn’t carefully planned, which could cause cables to deteriorate or even lead to dangerous conditions. Dividers not only help maintain cable tray segregation, but they also facilitate airflow, helping to maintain optimal temperature conditions for the cables.
While a ship configuration can optimize space in installations where room is limited, it requires meticulous planning to ensure proper cable segregation. The use of dividers, careful layering, and appropriate spacing is essential for ensuring that the installation is both safe and effective, preventing interference and maintaining system performance.
Step-by-Step Guide to Cable Tray Barrier Installation
The Role of Cable Tray Isolators in Segregation
Cable Tray Isolators: A Key Component in Effective Segregation
Cable tray isolators are specialized devices designed to enhance cable tray segregation by providing an additional layer of protection between cables. These isolators are particularly useful for preventing cross-talk and electrical interference between power and signal cables.
- Function of Cable Tray Isolators: Cable tray isolators work by physically and electrically isolating cables of different types or voltage levels within the tray. By doing so, they reduce the risk of electromagnetic interference (EMI) and prevent the unintended induction of electrical noise or signals between cables.
- Types of Cable Tray Isolators: Isolators come in various materials and configurations, such as plastic or rubber isolators, to suit different installation requirements. Some isolators are designed to be installed between specific cables, while others may be placed along the entire length of the cable tray to provide uniform isolation.
- Applications: Cable tray isolators are particularly useful in environments where sensitive communication or control signals need to be protected from high-voltage cables, ensuring that the integrity of the signals is not compromised by electrical noise.
Cable Tray Isolation Pad: Enhancing Cable Tray Segregation
What is a Cable Tray Isolation Pad?
A cable tray isolation pad is an advanced solution used to further improve cable tray segregation by providing a protective barrier between cables, reducing the risk of electrical interference and mechanical damage. This isolation pad helps protect cables from physical damage caused by friction and minimizes the risk of short circuits caused by cable wear.
- Function of Cable Tray Isolation Pads: The primary function of a cable tray isolation pad is to provide a cushioning effect between cables of different types or voltages. By installing these pads, cables can be better insulated from each other, preventing contact that might cause short circuits or signal degradation. The pads also help reduce noise interference, particularly in environments with high electromagnetic interference (EMI).
- Material and Design: Typically made from durable materials like rubber, silicone, or non-conductive polymers, cable tray isolation pads are designed to withstand the rigors of industrial environments. These materials are chosen for their insulating properties, as well as their ability to resist wear and environmental factors like heat or moisture. Some pads may have additional features, such as grooves or channels, to accommodate different cable sizes and enhance airflow within the tray.
- Applications of Cable Tray Isolation Pads: These pads are especially beneficial in areas where high-voltage cables are installed alongside sensitive low-voltage or signal cables. By creating a barrier between the cables, isolation pads help preserve the integrity of the system, ensuring that the sensitive signals are not affected by electromagnetic fields or power line noise. Cable tray isolation pads are also valuable in installations requiring compliance with strict safety standards, particularly in high-risk environments like power plants, factories, or hazardous locations.
Benefits of Cable Tray Isolation Pads
- Reduced Electrical Interference: By keeping high-voltage and low-voltage cables physically separated, isolation pads reduce the potential for electromagnetic interference (EMI), ensuring stable operation of the electrical system.
- Protection Against Physical Damage: Isolation pads act as a cushion, preventing cables from rubbing against each other, which can cause wear or lead to short circuits.
- Improved Safety: By enhancing cable separation and reducing the chance of electrical faults, isolation pads contribute to the overall safety of the installation.
- Enhanced Durability: With their robust construction, cable tray isolation pads increase the lifespan of cables, reducing the need for frequent replacements or repairs.
FAQs about Cable Tray Segregation
The spacing between cable trays is an important consideration in the design and installation of electrical systems to ensure proper functionality, safety, and compliance with standards. According to industry best practices, the distance between parallel cable trays should be sufficient to allow for easy cable installation, maintenance, and proper airflow for heat dissipation. The National Electrical Code (NEC) and other industry standards often provide guidance on this matter.
Typically, the minimum distance between cable trays ranges from 6 inches to 12 inches, but this distance may vary based on the specific installation environment, such as whether the cables are exposed to high temperatures, or whether they contain sensitive signal cables that require additional separation. The spacing is also affected by the overall load of the cables, as heavier cable trays may require more clearance to prevent strain on the tray system.
It’s important to remember that the spacing between trays should also allow for adequate support of the trays themselves, ensuring that the weight of the cables does not cause the trays to sag or become unstable. Cable tray manufacturers often provide specifications for recommended spacing based on tray size and load.
Cable segregation refers to the practice of separating different types of cables within a cable tray or duct, based on factors such as their function, voltage, and sensitivity to electromagnetic interference (EMI). This is particularly important in installations where power cables, control cables, and communication cables are used in the same area, as improperly segregated cables can cause signal degradation, safety hazards, or electromagnetic interference between the cables.
For example, power cables that carry high voltages should not be placed next to low-voltage signal cables, as the electromagnetic fields from the power cables can induce noise into the signal cables, leading to system malfunctions. Similarly, cables carrying sensitive data or low-level signals (such as AI, AO, or DO cables) should be kept separate from high-voltage power cables to prevent electrical noise or cross-talk.
Cable segregation is not only essential for maintaining the integrity of the electrical system but also plays a key role in adhering to safety standards such as the National Electrical Code (NEC) and Canadian Electrical Code (CEC), which provide guidelines on the separation of power and signal cables. Proper segregation helps prevent safety hazards, ensures the longevity of the installation, and maintains the performance of the system.
The spacing of cable tray rungs is crucial for the proper support of cables within the tray system. Rung spacing refers to the distance between each horizontal support bar (or rung) that runs across the cable tray. The spacing must be optimized to prevent cable sagging, ensure easy cable management, and allow sufficient ventilation and airflow.
Typically, the spacing for cable tray rungs is between 6 to 12 inches, though it can vary depending on the type of tray, the weight of the cables, and local installation standards. For example, ladder cable trays, which are commonly used in industrial applications, often have rungs spaced around 9 inches apart. This is ideal for providing adequate support for cables, while also ensuring airflow for heat dissipation.
In some cases, the spacing may be smaller or larger depending on the size and weight of the cables being installed. Heavier or larger cables might require closer rung spacing to provide additional support and prevent sagging, while lighter cables may allow for wider rung spacing.
It’s essential to follow the manufacturer’s specifications for rung spacing to ensure the cable tray system is both structurally sound and compliant with safety standards.
The maximum support spacing for cable trays refers to the distance between each support point or hanger that holds the tray in place, ensuring that the tray remains stable and capable of supporting the weight of the cables. The support spacing is determined by several factors, including the size of the tray, the weight of the cables, the material of the tray, and the type of installation environment.
In general, the maximum support spacing for cable trays ranges from 5 to 10 feet, depending on the tray’s size and load capacity. For example, smaller trays with lightweight cables may be supported at larger intervals, such as 10 feet, while larger trays or trays with heavier cables may require support at intervals of 5 feet or less to prevent sagging and ensure the tray’s structural integrity.
Manufacturers often provide detailed specifications for the maximum support spacing for their cable trays, and it’s crucial to adhere to these guidelines to prevent tray damage, cable wear, or potential safety issues. Additionally, factors such as the location of the installation, exposure to environmental conditions (e.g., high heat, vibrations), and the type of cables used should be considered when determining the appropriate support spacing.In some high-load or hazardous environments, closer support spacing may be required to maintain stability and meet local building codes or electrical standards. It’s always best to consult with an engineer or follow manufacturer recommendations for optimal tray support spacing.
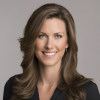
As the editor of GangLong Fiberglass, I have years of experience and in-depth research, focusing on cable tray products, fiberglass solutions, and grille systems. I incorporate years of industry insights and practical experience into every content, committed to promoting the progress of the industry. At GangLong Fiberglass, my commitment is reflected in every product, from innovative cable trays to durable fiberglass solutions and sturdy grille systems. As an authoritative voice in the industry, my goal is to provide valuable information to professionals and businesses and promote forward-looking solutions.