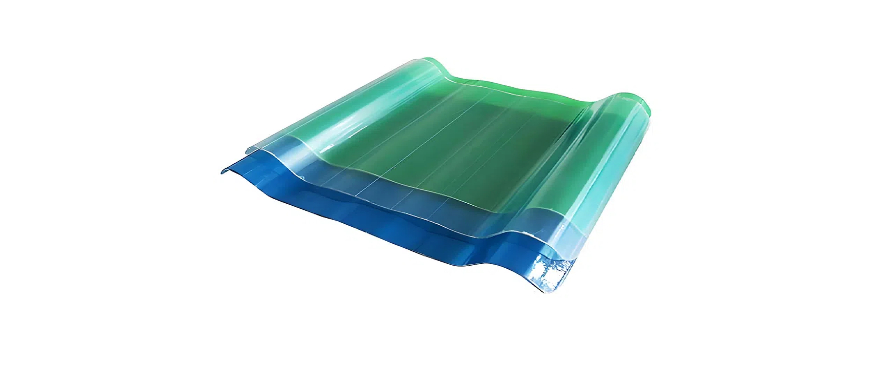
Fiberglass sheets are versatile materials widely employed in construction and design due to their strength, lightweight nature, and durability. These fiberglass sheet uses include applications in roofing, where they provide excellent weather resistance and insulation, contributing to energy efficiency. In commercial and industrial settings, fiberglass sheets are utilized for wall panels and partitions, offering a robust alternative to traditional materials. Additionally, fiberglass sheet uses extend to creating insulation barriers, enhancing thermal performance and soundproofing in residential buildings. Moreover, fiberglass sheet for exhaust is designed to withstand high temperatures, making it ideal for exhaust systems in vehicles and machinery, where it provides effective thermal insulation and protects against heat-related damage. Their resistance to moisture and chemicals makes fiberglass sheets ideal for environments prone to humidity or corrosive substances. Overall, fiberglass sheet uses highlight the material’s adaptability and practicality across diverse applications. Fiberglass sheet uses include construction, automotive, and industrial applications, offering strength, lightweight, and corrosion resistance for skylights, cladding, and more.
What Fiberglass Sheets Are and Their Manufacturing Process
Fiberglass sheets are versatile, durable materials made from woven or chopped strands of glass fibers bound together with a resin. These sheets have a variety of uses across multiple industries, ranging from construction and automotive applications to marine and aerospace industries. The production process of fiberglass sheets involves several steps, each critical to ensuring their strength, resilience, and functionality. This answer will explore what fiberglass sheets are, the materials involved, the stages of manufacturing, and the key factors that make them useful in modern building projects and industrial applications.
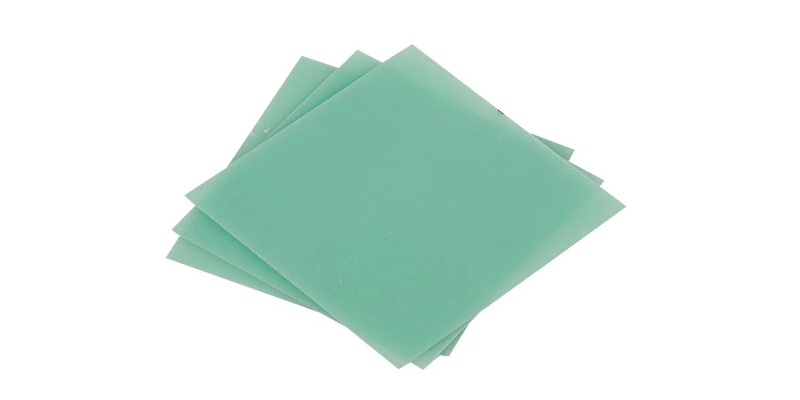
What is a Fiberglass Sheet?
Fiberglass sheets are thin, flat panels composed of woven or chopped strands of glass fibers embedded in a resin matrix. The unique properties of fiberglass—lightweight, strong, heat-resistant, and chemically resistant—make it a popular material for a wide variety of applications. It is often used in the construction, automotive, marine, and industrial sectors, where its durability and strength are highly valued. Fiberglass sheets can be customized for specific uses, with different types of glass fibers, resins, and thicknesses, making them versatile and adaptable to multiple industries.
The Materials Involved in Fiberglass Sheet Manufacturing
The primary materials used in the production of fiberglass sheets are glass fibers and resins. The glass fibers used can be in the form of continuous strands (woven) or chopped fibers. These fibers are typically made from silica-based sand and other raw materials that are melted down and spun into thin strands. The resin acts as the binder that holds the fibers together, providing structural integrity and enhancing the material’s strength and durability. Common resins used include polyester, vinyl ester, and epoxy. These materials combine to form the core structure of fiberglass sheets, which can then be further treated for various applications.
How is a Fiberglass Sheet Made?
The process of manufacturing fiberglass sheets involves several key steps, starting with the creation of the glass fibers and ending with the final sheet. Here’s an of the manufacturing process:
Glass Fiber Production
The first step in making fiberglass sheets is the production of glass fibers. Sand, along with other minerals, is melted in a furnace at extremely high temperatures, around 1,700°F (927°C). This molten glass is then pulled through small holes in a spinning device to form fine strands of glass. These strands are then collected and either woven into mats or chopped into shorter fibers.
Resin Application
Once the glass fibers are prepared, a resin is applied to bind the fibers together. The type of resin depends on the specific application of the fiberglass sheet. Polyester resin is commonly used for general purposes, while epoxy and vinyl ester resins are chosen for more demanding applications due to their superior strength and chemical resistance. The resin is typically applied by spraying or soaking the fiberglass fibers.
Curing Process
After the resin is applied, the fiberglass is placed in a mold or laid out flat. The material is then heated to cure the resin, hardening it and giving the fiberglass sheet its desired shape and durability. This process also ensures that the resin bonds effectively with the glass fibers, enhancing the sheet’s structural strength.
Finishing
Once the fiberglass has been cured, the sheet is removed from the mold and may undergo additional finishing processes. This can include cutting the sheet to the required size, smoothing the surface, and applying additional coatings, such as UV protection or flame retardants, to further improve the material’s properties.
Fiberglass sheet manufacturing involves a well-coordinated process of fiber creation, resin application, and curing, which results in a material that is ideal for a variety of industrial and construction applications. Whether used for strength, insulation, or protection, fiberglass sheets have become a go-to material across many sectors. Understanding the manufacturing process helps explain why fiberglass sheets are such an essential component of modern building projects and industrial applications, showcasing their strength and resilience.
Fiberglass Sheet Uses and Applications
Fiberglass sheets are increasingly popular in various industries due to their exceptional properties. The lightweight nature and strength of fiberglass make it a perfect material for construction, automotive, aerospace, and more. Before committing to a full purchase, reviewing fiberglass sheet samples can help users evaluate the material’s performance, ensuring it meets the specific needs of their project. Below are several key applications that illustrate the diverse fiberglass sheet uses.
Applications in Construction
Fiberglass sheets are commonly utilized in construction for roofing and wall panels. Their durability ensures a long lifespan, reducing the need for frequent repairs or replacements. The fiberglass sheet uses in roofing include providing a protective layer against harsh weather conditions. They offer superior insulation properties, which help maintain indoor temperatures and improve energy efficiency. In wall applications, fiberglass sheets can serve as both structural and decorative elements, providing an aesthetically pleasing finish while enhancing strength.
Insulation Properties
Another prominent application of fiberglass sheets is in insulation. Fiberglass insulation is renowned for its thermal resistance, largely attributed to fiberglass sheet thermal conductivity, which determines how effectively the material resists heat transfer. This property makes fiberglass sheet uses essential in both residential and commercial construction. Fiberglass sheets can be installed in attics, walls, and floors to significantly reduce energy costs by minimizing heat loss in winter and heat gain in summer. Additionally, their insulation properties, influenced by fiberglass sheet thermal conductivity, make them an excellent option as fiberglass sheet for partition, contributing to soundproofing and making them ideal for buildings located in noisy environments.
Chemical Resistance
Fiberglass sheets possess excellent chemical resistance, which expands their application in environments where exposure to harsh substances is common. Industries such as chemical processing and manufacturing benefit from fiberglass sheet uses due to their ability to withstand corrosive materials. Fiberglass sheets are used to line tanks and containers, ensuring safety and longevity. This chemical resistance makes fiberglass an ideal choice for laboratories and industrial settings where other materials may fail.
Lightweight Yet Strong
One of the significant advantages of fiberglass sheets is their lightweight nature, which simplifies transportation and installation. The fiberglass sheet uses are especially beneficial in projects where weight is a critical factor. This property allows for easy handling without compromising strength, making fiberglass sheets suitable for various structural applications. In high-rise buildings, for instance, the reduced weight contributes to overall structural efficiency and safety.
Environmental Benefits in Fiberglass Sheet Uses
Fiberglass sheets uses are often favored for their environmental benefits. Many fiberglass sheet uses involve recyclable materials, which contribute to sustainable building practices. When properly recycled, fiberglass can significantly reduce waste in landfills. This eco-friendly aspect makes fiberglass an attractive option for environmentally conscious builders and consumers. The ability to produce fiberglass sheets that meet strict environmental standards adds to their appeal in modern construction.
Fire Resistance
Fiberglass sheets are also recognized for their fire-resistant properties. They can withstand high temperatures, making fiberglass sheet uses crucial in applications where fire safety is a concern. In construction, these sheets can be used in fire-rated assemblies, enhancing the overall safety of buildings. This capability is particularly important in industrial settings where flammable materials are present, ensuring compliance with safety regulations.
Versatile Design Options
The versatility of fiberglass sheets extends to design. With the ability to mold and shape fiberglass into various forms, fiberglass sheet uses can be customized to meet specific project requirements. Architects and designers appreciate this flexibility, as it allows them to create unique and innovative structures. From curved walls to intricate roofing designs, fiberglass sheets can be tailored to enhance both functionality and aesthetics.
Impact Resistance
Fiberglass sheets offer excellent impact resistance, making them suitable for high-traffic areas and facilities that require durable materials. Their toughness ensures that they can withstand physical stress without cracking or breaking, which is particularly beneficial in schools, hospitals, and industrial facilities. The fiberglass sheet uses in these settings contribute to safety and longevity, reducing the need for frequent replacements.
Cost-Effectiveness
The cost-effectiveness of fiberglass sheets makes them a popular choice in various applications. While the initial investment may be comparable to other materials, the long-term benefits of durability and low maintenance make fiberglass sheet uses economically advantageous. Over time, the savings on repairs and energy costs can far outweigh the initial purchase price, making wholesale fiberglass sheets an attractive option for budget-conscious projects. Their longevity and resistance to environmental factors further contribute to their value, ensuring cost savings over the lifespan of the material.
Fiberglass Sheets in Automotive Applications
In addition to construction, fiberglass sheets find extensive use in the automotive industry. The lightweight yet strong characteristics of fiberglass make it ideal for producing body panels and components. Fiberglass sheet uses in automotive applications contribute to improved fuel efficiency and performance, as lighter vehicles consume less energy. The versatility of fiberglass allows for various shapes and designs, enabling manufacturers to innovate and enhance vehicle aesthetics.
Top FRP Cable Threading Pipe Suppliers You Should Know
Construction and Architectural Design
Fiberglass sheets have gained significant traction in construction due to their lightweight and durable nature. They can be used in architectural design to create aesthetically pleasing yet functional elements. Fiberglass sheets are often employed as skylights or decorative frp wall panels, allowing natural light to permeate indoor spaces while maintaining energy efficiency. Their resistance to weathering and UV light also ensures longevity in various environmental conditions, making them an ideal choice for outdoor applications.
Insulation Materials
Fiberglass sheet uses extend to insulation applications, where they provide excellent thermal resistance. Their inherent properties make them effective insulators in both residential and commercial buildings. By minimizing heat transfer, fiberglass sheets help regulate indoor temperatures, contributing to energy savings. Additionally, they offer soundproofing benefits, reducing noise pollution between rooms or from external sources. This dual functionality enhances overall comfort in living and working spaces.
Discover If Are Fiberglass Rods Used in Camping Chairs Cheap
Electrical Insulation about Fiberglass Sheet Uses
In the realm of electrical applications, fiberglass sheets serve as vital insulators. Their non-conductive nature ensures safety in electrical installations, protecting against short circuits and electrical fires. Fiberglass sheets can be manufactured in various thicknesses and densities to meet specific electrical insulation requirements. Industries rely on these materials for building electrical panels, housings, and insulative barriers, ensuring safe and reliable performance in various environments.
Marine Applications
The marine industry frequently utilizes fiberglass sheets due to their resistance to corrosion and moisture. These sheets can be found in boat construction and repair, where they contribute to the structural integrity of vessels while minimizing weight. Additionally, fiberglass sheets are used in creating marine interiors, such as fiberglass interior panels, as they can withstand harsh conditions without deteriorating. This versatility makes them an essential material for both commercial and recreational boating applications.
Automotive Manufacturing
Fiberglass sheets have also made a mark in the automotive sector. They are used in producing lightweight body panels and components, which can enhance fuel efficiency and performance. Their durability ensures that vehicles can withstand rigorous conditions while maintaining their aesthetic appeal. The use of fiberglass sheets in automotive design reflects the industry’s push towards innovation and sustainability, as lighter vehicles contribute to reduced emissions.
Aerospace Engineering
In aerospace engineering, fiberglass sheets play a crucial role in the construction of aircraft and spacecraft. Their lightweight properties are essential for optimizing fuel efficiency and performance. These sheets are used in various components, including fuselages and wing structures, providing strength without adding excessive weight. The ability to withstand extreme conditions makes fiberglass sheets an invaluable asset in aerospace applications, where safety and performance are paramount.
Chemical and Corrosion Resistance
One of the notable fiberglass sheet uses is their application in environments exposed to harsh chemicals. Their resistance to corrosion makes them suitable for lining tanks, pipes, and other fiberglass sheet uses in chemical processing plants. By preventing leaks and degradation, fiberglass sheets contribute to the safety and efficiency of industrial operations. This durability is crucial for maintaining the integrity of systems that handle corrosive substances.
Signage and Displays
Fiberglass sheets are widely used in signage and display applications due to their ability to be molded into various shapes and sizes. They provide a lightweight and weather-resistant option for outdoor signage, ensuring visibility and durability. Fiberglass sheet for signs are ideal for creating vibrant, long-lasting signs that can endure harsh environmental conditions. In retail environments, fiberglass sheets can be utilized for attractive displays that enhance product presentation. Their versatility allows for creative designs while maintaining structural integrity, making them a favorite among advertisers and retailers alike.
Sports and Recreation
The sports industry has also embraced fiberglass sheets for various applications. They are commonly found in the production of sporting goods such as surfboards, kayaks, and protective gear. The lightweight yet robust nature of fiberglass sheets contributes to better performance and user experience. Their ability to be shaped and molded makes them ideal for creating custom designs tailored to specific sports or activities, appealing to enthusiasts and professionals alike.
Sustainability in Manufacturing
An emerging trend in fiberglass sheet uses is their incorporation into sustainable manufacturing practices. As industries strive to reduce their environmental footprint, fiberglass sheets can be produced using recycled materials, contributing to a circular economy. Their longevity and durability further enhance sustainability, as fewer replacements are needed over time. This focus on eco-friendly practices aligns with global initiatives to promote responsible consumption and production.
Innovative Uses: Can You Reshape Fiberglass Rods Effectively
Types of Fiberglass Sheets and Fiberglass Sheet Uses
Fiberglass sheets come in a range of types, each designed to meet specific needs depending on the application, durability requirements, and environmental conditions. These types vary based on the form of the fiberglass, the resin used, and the intended application. Understanding the different types of fiberglass sheets and their respective uses is essential for selecting the right material for a given project. In this guide, we will explore the various types of fiberglass sheets, how they are made, and the industries and scenarios in which each type excels.
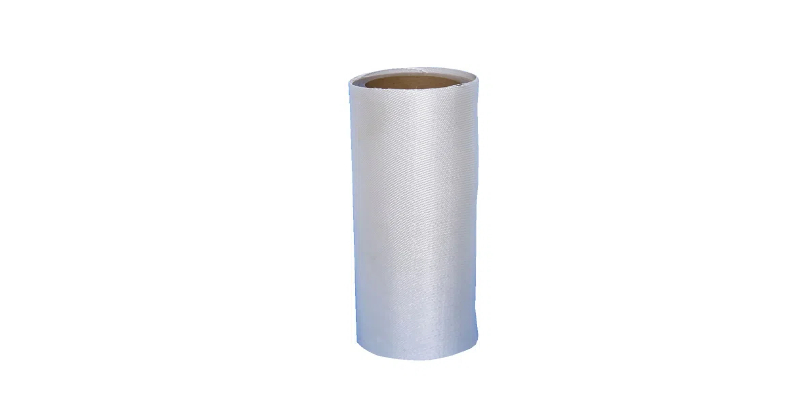
Woven Fiberglass Sheets
Woven fiberglass sheets are made by weaving glass fibers into a fabric-like structure, which is then impregnated with resin to form a rigid sheet. This type of fiberglass sheet is typically characterized by its high strength and durability, owing to the interwoven fibers. Woven fiberglass sheets are often used in situations that require enhanced strength and resilience, and they provide additional flexibility compared to other types of fiberglass sheets.
Primary Industries and Applications for Woven Fiberglass Sheets
Woven fiberglass sheets are commonly used in industries where strength and flexibility are key. They are frequently applied in automotive manufacturing for the creation of lightweight, durable components such as body panels, bumpers, and doors. In construction, woven fiberglass is used for applications like roofing and cladding, especially in areas requiring high impact resistance. Additionally, these sheets are essential in the marine industry for boat hulls and decks due to their strength and resistance to water corrosion.
Chopped Strand Mat (CSM) Fiberglass Sheets
Chopped strand mat fiberglass sheets are created by randomly cutting glass fibers into short lengths and bonding them together with a resin. This type of fiberglass sheet is less expensive to produce than woven fiberglass, but it still offers strength and durability. The random arrangement of fibers in CSM sheets provides good overall strength and excellent conformability, making them a versatile material for a variety of applications.
Primary Industries and Applications for CSM Fiberglass Sheets
Chopped strand mat fiberglass sheets are commonly used in automotive and construction industries. In automotive manufacturing, CSM fiberglass is used for producing molded parts like dashboards, fenders, and panels. In construction, it is utilized for making reinforced concrete forms, insulation materials, and wall panels due to its versatility and ability to conform to different shapes. These sheets are also used in marine applications for boat building and repairs, particularly for areas where high surface finish quality is less critical.
Uni-Directional Fiberglass Sheets
Uni-directional fiberglass sheets feature fibers aligned in a single direction, providing exceptional strength along that axis. These sheets are known for their superior tensile strength, which makes them ideal for applications requiring load-bearing capacity in one direction. The alignment of the fibers maximizes strength where it’s needed the most, making them particularly useful for high-stress applications.
Primary Industries and Applications for Uni-Directional Fiberglass Sheets
Uni-directional fiberglass sheets are primarily used in aerospace, automotive, and construction industries where directional strength is required. In aerospace, they are used in structural components such as aircraft wings and fuselage parts due to their lightweight yet strong properties. In the automotive industry, uni-directional fiberglass is used for parts such as high-performance vehicle body panels that need to withstand significant forces in specific directions. These sheets are also used in construction for reinforcing structures where directional strength and reduced weight are essential, such as in beams and load-bearing walls.
Polyester Resin-Finished Fiberglass Sheets
Polyester resin-finished fiberglass sheets are made by combining glass fibers with a polyester resin, offering a combination of strength and flexibility. The resin finish provides a smooth surface and enhanced durability, making these sheets resistant to environmental factors like UV radiation and weathering. Polyester resin-finished fiberglass sheets are generally used for both interior and exterior applications.
Primary Industries and Applications for Polyester Resin-Finished Fiberglass Sheets
Polyester resin-finished fiberglass sheets are widely used in construction for applications such as roofing, skylights, and exterior cladding. Their resistance to weathering and UV light makes them suitable for outdoor environments, especially in areas exposed to sunlight. They are also commonly used in automotive manufacturing for producing lightweight yet strong body parts, such as hoods and fenders. Additionally, these sheets are utilized in marine applications, including for boat covers and hulls, as they offer a combination of strength and protection against the elements.
Epoxy Resin-Finished Fiberglass Sheets
Epoxy resin-finished fiberglass sheets are known for their superior bonding strength, chemical resistance, and durability. These sheets are often chosen for their high-performance qualities, especially in demanding industrial applications. The epoxy resin provides excellent adhesion and moisture resistance, making these sheets ideal for environments where chemical exposure or extreme conditions are present.
Primary Industries and Applications for Epoxy Resin-Finished Fiberglass Sheets
Epoxy resin-finished fiberglass sheets are commonly used in marine, automotive, and industrial sectors. In marine applications, they are used for producing boat hulls and other watercraft components, as the epoxy resin enhances resistance to water and salt corrosion. In industrial settings, these sheets are used for creating strong, durable parts for machinery or equipment that will be exposed to harsh chemicals or high temperatures. Additionally, in the aerospace industry, epoxy resin fiberglass sheets are employed for parts requiring precise strength, durability, and weight reduction, such as aircraft components and structural reinforcements.
Fire-Retardant Fiberglass Sheets
Fire-retardant fiberglass sheets are treated with additives that make them resistant to flame and heat, significantly improving safety in high-risk environments. These sheets maintain the same strength and flexibility as standard fiberglass, but with added protection against fire hazards. They are often used in applications where fire safety is a top concern.
Primary Industries and Applications for Fire-Retardant Fiberglass Sheets
Fire-retardant fiberglass sheets are crucial in industries like construction, electronics, and automotive. In construction, these sheets are used for fire-resistant doors, panels, and insulation. In the electronics industry, they are often used in circuit boards and housing for electrical components that need to meet stringent fire safety regulations. In automotive manufacturing, fire-retardant fiberglass is used for components that may be exposed to high heat or flames, such as engine parts and undercarriages.
Fiberglass sheets come in a wide variety of types, each suited to different needs and environments. From woven sheets with enhanced flexibility and strength to fire-retardant sheets providing critical safety in hazardous environments, the wide range of fiberglass sheet options ensures that they can meet the demands of numerous industries. By understanding the unique characteristics of each type of fiberglass sheet, businesses can select the most appropriate material for their specific applications, ensuring optimal performance and reliability. Whether you’re in construction, automotive, marine, or aerospace, selecting the right fiberglass sheet type will significantly impact the success of your project.
Advantages and Disadvantages of Fiberglass Sheets and Their Impact on Fiberglass Sheet Uses
Fiberglass sheets are widely recognized for their versatility, strength, and durability, making them a preferred material in various industries such as construction, automotive, marine, and industrial sectors. However, like any material, fiberglass sheets come with their own set of advantages and disadvantages that influence how and where they are used. Understanding these pros and cons is essential for evaluating their suitability for specific applications. In the following sections, we will examine the key advantages and disadvantages of fiberglass sheets and explore how these factors affect their use across different industries.
Advantages of Fiberglass Sheets
Fiberglass sheets offer several benefits that make them suitable for numerous applications in various industries. These advantages play a critical role in determining their effectiveness and widespread use. From exceptional strength-to-weight ratios to resistance to environmental factors, fiberglass sheets provide essential qualities for many sectors. Let’s explore the most notable benefits of fiberglass sheets:
Strength and Durability
One of the biggest advantages of fiberglass sheets is their high strength and durability. Fiberglass is renowned for being strong yet lightweight, making it ideal for structural applications where both strength and reduced weight are necessary. The material can withstand considerable physical stress without cracking or breaking, making it suitable for demanding environments such as construction, automotive, and marine applications.
Resistance to Corrosion and Chemicals
Fiberglass sheets are naturally resistant to corrosion, moisture, and most chemicals, making them highly valuable for industries exposed to harsh environmental conditions. In marine applications, for example, fiberglass sheets are resistant to saltwater corrosion, making them ideal for boat hulls and decks. In the industrial sector, fiberglass sheets are used in environments where exposure to chemicals, oils, or harsh weather is a concern.
Insulation Properties
Fiberglass sheets provide excellent thermal and sound insulation. The material is commonly used in construction as an insulating layer in walls, roofs, and floors. Fiberglass insulation reduces heat transfer and helps regulate temperature within buildings, making it an energy-efficient option. Additionally, fiberglass sheets’ ability to dampen sound vibrations makes them useful in noise-reducing applications in commercial and industrial settings.
Lightweight and Easy to Handle
Despite its strength, fiberglass sheets are lightweight, making them easier to transport, handle, and install compared to heavier materials like metal or concrete. This characteristic is particularly beneficial in industries such as automotive manufacturing, where weight reduction is crucial for performance and fuel efficiency.
Disadvantages of Fiberglass Sheets
While fiberglass sheets are an excellent material in many respects, they also have a few drawbacks that must be taken into account when determining their suitability for specific applications. Understanding these limitations is important for ensuring that fiberglass sheets are used appropriately and safely. The following points highlight the primary disadvantages of fiberglass sheets:
Brittleness Over Time
Although fiberglass sheets are initially strong, they can become brittle over time, particularly if exposed to UV radiation. Prolonged exposure to sunlight can degrade the resin holding the glass fibers together, leading to weakening and increased fragility. This is an important consideration for applications in outdoor environments, such as roofing or cladding, where fiberglass sheets may need to be coated or protected to ensure long-term durability.
Potential Health Risks
Handling fiberglass sheets without proper protective equipment can result in skin irritation and respiratory issues. The fine glass fibers can become airborne during cutting or installation, leading to inhalation risks that may cause irritation to the lungs or throat. In addition, fiberglass particles can get under the skin, causing itching and discomfort. Adequate precautions, such as wearing gloves, long sleeves, masks, and goggles, are essential when working with fiberglass to minimize these health risks.
Difficulty in Repairing Damage
If fiberglass sheets become damaged, repairing them can be more difficult than other materials like wood or metal. Cracks or breaks in fiberglass often require specialized materials, such as resin, to patch up and restore their strength. This can make repairs more time-consuming and costly, particularly if large sections of fiberglass need to be replaced.
High Initial Cost
Fiberglass sheets tend to have a higher initial cost than some alternative materials like wood, plastic, or metal. While their durability and long lifespan offset this expense in many cases, the higher upfront cost may be a deterrent for some applications. For projects with tight budgets, cost-effectiveness may be a concern when opting for fiberglass sheets.
How Advantages and Disadvantages Affect Fiberglass Sheet Uses
The advantages and disadvantages of fiberglass sheets directly influence how they are utilized in various applications. Let’s take a closer look at how these factors play out in real-world uses:
Construction and Building Projects
In construction, fiberglass sheets are commonly used for roofing, cladding, insulation, and skylights due to their strength, durability, and resistance to environmental damage. However, the brittleness of fiberglass over time can affect its use for roofing and outdoor cladding, requiring protective coatings to prolong its lifespan. The potential health risks associated with exposure also require that workers take precautions during installation to ensure safety.
Automotive and Aerospace Industries
Fiberglass sheets are widely used in automotive and aerospace manufacturing due to their high strength-to-weight ratio, which contributes to fuel efficiency and overall performance. However, the brittleness of fiberglass and the challenge of repairing it can make it less ideal for certain components that might be subject to frequent wear and tear. Manufacturers often compensate by reinforcing fiberglass with other materials or applying protective coatings to prevent degradation.
Marine Applications
In marine industries, fiberglass sheets are favored for boat hulls and decks due to their resistance to corrosion and water damage. The long-lasting durability of fiberglass makes it suitable for harsh marine environments. However, the potential UV degradation of fiberglass can be mitigated with protective coatings to extend the lifespan of boats or watercraft. The material’s lightweight nature also contributes to improved fuel efficiency for vessels.
Industrial Settings
Fiberglass sheets are used in industrial applications for protective barriers, insulation, and electrical panels. The material’s resistance to chemicals and moisture makes it ideal for use in factories and manufacturing plants. However, in areas with high wear and tear, its brittleness and difficulty in repair can limit its practicality. Fiberglass sheets in such settings require regular inspections and maintenance to ensure they continue performing optimally.
Fiberglass sheets are highly versatile materials that offer numerous benefits, including strength, corrosion resistance, and insulation properties, making them valuable across multiple industries. However, their disadvantages—such as brittleness over time, health risks, and high costs—can influence how and where they are used. To maximize the benefits of fiberglass sheets, manufacturers and users must take appropriate precautions and consider the material’s limitations when selecting it for specific applications. Ultimately, understanding the advantages and disadvantages of fiberglass sheets allows for better decision-making, ensuring that they are used in the most suitable environments where their strengths can be fully utilized.
Key Considerations for Fiberglass Sheet Uses and Selection
Fiberglass sheets are widely used in various industries due to their strength, lightweight nature, and resistance to environmental factors. However, choosing the right fiberglass sheet requires careful consideration of multiple factors to ensure optimal performance, longevity, and cost-effectiveness. Different applications—such as construction, automotive, marine, and industrial manufacturing—demand specific material properties, including fire resistance, UV stability, chemical resistance, and mechanical strength. Selecting the wrong type of fiberglass sheet can lead to premature wear, structural failure, or increased maintenance costs.
In this guide, we will explore the main considerations when choosing fiberglass sheets, helping businesses, engineers, and manufacturers make informed decisions. These considerations include material composition, strength and durability, environmental resistance, transparency, fire and chemical resistance, and cost-effectiveness. Understanding these aspects ensures that the selected fiberglass sheet aligns with the specific requirements of the intended application.
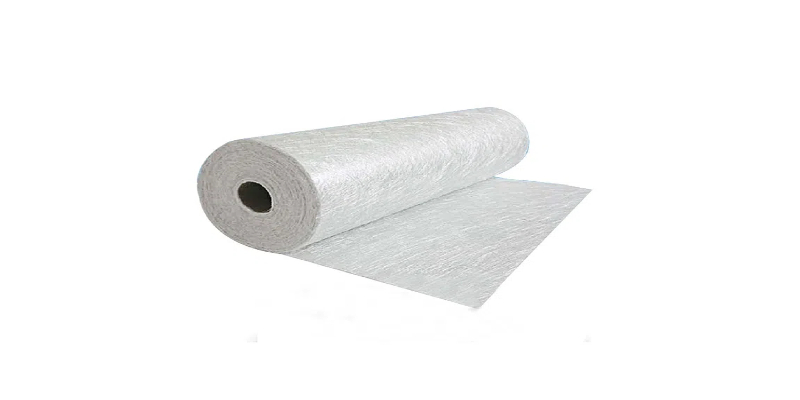
Material Composition – Understanding Resin and Fiber Types
Fiberglass sheets are made from glass fiber reinforcements embedded in a resin matrix. The type of resin used significantly impacts the sheet’s properties, including its flexibility, chemical resistance, and durability. Understanding the resin and fiber combination helps in selecting the right sheet for different environmental conditions and mechanical loads.
Key Considerations:
- Polyester Resin Fiberglass Sheets: Commonly used in construction and general-purpose applications due to their affordability and decent durability.
- Epoxy Resin Fiberglass Sheets: Offer superior mechanical strength and adhesion, making them ideal for aerospace, automotive, and high-performance applications.
- Vinyl Ester Resin Fiberglass Sheets: Known for their excellent corrosion resistance, these sheets are widely used in marine and chemical processing industries.
- Glass Fiber Variations: The type of glass fiber (e.g., E-glass for general use, S-glass for high strength, and C-glass for chemical resistance) affects the sheet’s performance characteristics.
Strength and Durability – Matching Load-Bearing Needs to Application
The mechanical strength of fiberglass sheets is crucial for ensuring structural integrity, especially in applications that experience high stress, impact, or vibration. The sheet’s thickness, reinforcement type, and fiber orientation all contribute to its overall strength.
Key Considerations:
- Load-Bearing Capacity: In construction and automotive applications, thicker sheets with multi-layer reinforcements provide better support for heavy loads.
- Impact Resistance: High-strength fiberglass sheets, reinforced with additional layers, are ideal for industrial machinery covers, vehicle panels, and aerospace components.
- Flexibility vs. Rigidity: Some applications require flexible fiberglass sheets for curved surfaces (such as boat hulls), while others need rigid sheets for structural support.
Environmental Resistance – Protection Against Weather and UV Exposure
Fiberglass sheets are often exposed to harsh environmental conditions, including extreme temperatures, UV radiation, and moisture. Choosing a sheet with the appropriate protective coatings or additives ensures longevity and sustained performance.
Key Considerations:
- UV-Resistant Coatings: Essential for outdoor applications like roofing, awnings, and marine structures to prevent yellowing and brittleness.
- Moisture and Water Resistance: Critical for marine and outdoor use, ensuring the sheet does not absorb water, weaken, or develop mold over time.
- Temperature Stability: High-temperature-resistant sheets are necessary for industrial environments where heat exposure is frequent.
Transparency and Light Transmission – Choosing Between Opaque, Translucent, and Transparent Sheets
Fiberglass sheets come in various levels of transparency, depending on the intended use. Some applications, such as skylights and greenhouses, require high light transmission, while others demand complete opacity for insulation and protection.
Key Considerations:
- Transparent Fiberglass Sheets: Ideal for skylights, greenhouse panels, and areas requiring natural lighting without compromising durability.
- Translucent Fiberglass Sheets: Commonly used in warehouses, factories, and commercial spaces where diffused light is preferred.
- Opaque Fiberglass Sheets: Suitable for industrial enclosures, automotive applications, and protective barriers where light transmission is not necessary.
Fire and Chemical Resistance – Ensuring Safety in High-Risk Environments
In environments where fire hazards or chemical exposure are concerns, selecting fiberglass sheets with fire-retardant or chemical-resistant properties is essential. These specialized sheets enhance safety and compliance with industry regulations.
Key Considerations:
- Fire-Resistant Fiberglass Sheets: Used in aerospace, power plants, and public buildings where fire safety standards must be met.
- Chemical-Resistant Fiberglass Sheets: Ideal for laboratories, chemical processing plants, and wastewater treatment facilities to withstand corrosive substances.
- Compliance with Safety Standards: Ensuring the selected fiberglass sheet meets industry-specific fire and chemical resistance regulations.
Cost-Effectiveness – Balancing Budget and Performance
While fiberglass sheets offer numerous benefits, selecting the right sheet also involves cost considerations. Higher-quality materials often come at a premium, but choosing a sheet that meets performance requirements without unnecessary over-specifications can help optimize costs.
Key Considerations:
- Initial Investment vs. Long-Term Durability: Investing in high-quality sheets may reduce maintenance and replacement costs over time.
- Application-Specific Selection: Avoid overpaying for high-performance sheets if the application does not require extreme durability or resistance.
- Bulk Purchasing and Supplier Selection: Buying from reputable manufacturers and considering bulk purchases can help lower costs.
Choosing the right fiberglass sheet requires a comprehensive evaluation of multiple factors, including material composition, strength, environmental resistance, transparency, fire and chemical resistance, and cost-effectiveness. Different industries and applications demand specific properties to ensure optimal performance, safety, and longevity. By understanding these key considerations, businesses and manufacturers can make informed decisions, ensuring that the selected fiberglass sheet aligns perfectly with the intended use case. This approach not only enhances efficiency but also maximizes the return on investment by selecting the most suitable fiberglass sheet for each unique application.
Choosing the Right Fiberglass Sheet Supplier
Finding a reliable and suitable fiberglass sheet supplier is a crucial decision for industries that depend on fiberglass for construction, automotive, marine, and industrial applications. The quality and performance of the fiberglass sheets you source directly impact the success of your projects. Whether you are looking for a supplier for large-scale industrial orders or smaller, specialized requirements, understanding what factors to prioritize can help you make an informed decision. In this guide, we will break down the key aspects to consider when selecting a fiberglass sheet supplier, from material quality to customer support and delivery efficiency.
Material Quality and Specifications
When choosing a fiberglass sheet supplier, the most important aspect to consider is the quality of the materials they offer. The fiberglass sheets should meet the specific standards and performance requirements of your application, whether it’s for construction, automotive, or any other industry. You should check if the supplier provides detailed product specifications, such as the type of glass fibers used (woven or chopped strands), resin type, thickness, and strength ratings.
A reputable supplier will offer fiberglass sheets that meet international standards for durability, fire resistance, and weathering. In industries like construction or aerospace, where high-performance materials are critical, ensuring that the supplier uses high-quality fibers and resins will directly affect the material’s reliability and longevity in the field.
Supplier’s Reputation and Experience
The reputation and experience of a fiberglass sheet supplier are essential when evaluating their ability to meet your needs. A well-established supplier with years of experience in the industry is more likely to offer superior products and a better understanding of the nuances of fiberglass sheet production. They should have a proven track record in supplying quality fiberglass sheets to similar industries or applications, whether it’s for residential, commercial, or industrial use.
Look for reviews, testimonials, or case studies that highlight their experience and reputation in your specific field. A supplier who has worked with similar projects will understand your requirements and be able to offer tailored solutions. Also, a good supplier will be transparent about their manufacturing processes, materials, and quality controls to ensure consistency and reliability.
Customization Options
Fiberglass sheet uses can vary greatly depending on the project, and many applications require customized solutions. Whether it’s the size, color, thickness, or coating of the fiberglass sheets, a supplier should be able to provide tailored products that meet your exact specifications.
Check if the supplier offers options for custom-cut fiberglass sheets, resin finishes, coatings, or specific strength and insulation properties. Customization is especially important for industries such as automotive or aerospace, where fiberglass sheets must be designed for particular structural needs or aesthetic purposes. Suppliers with flexible manufacturing processes can deliver specialized fiberglass sheets that provide optimal performance for your specific project requirements.
Lead Time and Delivery Efficiency
The timely delivery of fiberglass sheets is crucial, particularly for industries with tight schedules. When evaluating potential suppliers, make sure to inquire about their lead times for processing and shipping orders. A reliable supplier will have well-established delivery schedules and offer transparency regarding production and shipping timelines.
If you are working on a large-scale or time-sensitive project, it is essential to choose a supplier who can meet deadlines without compromising on the quality of the product. Also, consider the supplier’s ability to handle urgent or bulk orders in case you need additional sheets on short notice. Efficient delivery systems can minimize project delays and reduce the risk of running out of stock, ensuring that your fiberglass sheet supply chain remains uninterrupted.
Customer Support and After-Sales Service
Customer service plays a significant role in maintaining a positive business relationship with your fiberglass sheet supplier. A good supplier will offer comprehensive customer support, including guidance on product selection, technical assistance, and troubleshooting. For industries that rely heavily on precise specifications, such as construction or marine, having direct access to knowledgeable representatives is important for ensuring you are purchasing the right fiberglass sheets for your needs.
Moreover, consider the supplier’s after-sales services, such as warranty options, return policies, and technical support. Should any issues arise with the fiberglass sheets after purchase—such as defects, shipping damage, or installation guidance—having strong after-sales support ensures that any problems will be promptly addressed, reducing the impact on your project.
Price and Value for Money
Cost is an important factor when selecting a fiberglass sheet supplier, but it should not be the only consideration. While finding an affordable supplier is crucial, the price should reflect the quality, customization options, and service level offered. Cheaper fiberglass sheets may not provide the same performance or durability as higher-quality options, potentially leading to increased maintenance costs or early failure of materials.
Look for suppliers that offer a balance between cost and quality. Consider the long-term value of the fiberglass sheets—durable, high-performance sheets may cost more upfront but will save you money in the long run by reducing maintenance or replacement needs. Request quotes from multiple suppliers and compare their offerings to find the best deal without sacrificing quality or service.
Compliance with Industry Standards
Finally, ensuring that the fiberglass sheets you purchase comply with relevant industry standards is essential. In industries like construction, automotive, and marine, there are specific safety, environmental, and quality regulations that fiberglass sheets must adhere to. A reliable supplier will provide certifications or documentation showing that their products meet these regulations, including fire resistance, environmental impact, and health safety standards.
Compliance with standards not only ensures the safety and performance of the fiberglass sheets but also guarantees that they will be accepted by regulatory bodies for your specific project. A supplier who is proactive in maintaining certifications demonstrates their commitment to providing high-quality, compliant products.
When searching for a suitable fiberglass sheet supplier, it is crucial to consider several key factors, including material quality, reputation, customization options, delivery efficiency, customer support, and compliance with industry standards. These elements play a significant role in determining how well the supplier can meet your specific needs, whether for construction, automotive, or other industrial uses. By carefully evaluating these factors, you can ensure that you select a supplier who will deliver high-quality fiberglass sheets that will contribute to the success and longevity of your projects.
FAQs about Fiberglass Sheet Uses
Fiberglass itself is not universally banned, but there are concerns related to its health impacts, particularly with the fine glass fibers it contains. Inhalation of fiberglass dust can lead to respiratory issues and skin irritation, prompting regulatory bodies in some regions to impose restrictions on its use in certain applications. For example, products that release fiberglass particles into the air, such as some insulation materials, may be subject to stringent safety guidelines. Additionally, some specific formulations of fiberglass, particularly those involving hazardous resins or chemicals, might be restricted due to environmental concerns. The banning of certain fiberglass products often arises from a combination of health, safety, and environmental factors. To address these concerns, manufacturers are encouraged to develop safer alternatives or improve existing products to minimize the risks associated with fiberglass exposure while maintaining its beneficial properties.
Fiberglass paper is a specialized product made from fiberglass fibers that are processed into thin sheets. It is primarily used for insulation in various applications, including HVAC systems and buildings, where it provides excellent thermal resistance and soundproofing qualities. This type of paper is also utilized in electrical applications, serving as an insulator in transformers and capacitors due to its high dielectric strength. Furthermore, fiberglass paper can be employed in the manufacturing of composite materials, providing added strength and durability. In the automotive industry, it is used in sound-deadening applications, helping to minimize noise in vehicles. Additionally, fiberglass paper is beneficial in construction for creating barriers against moisture and vapors, enhancing energy efficiency. Its lightweight nature and resistance to heat make it a preferred choice in many industries that require reliable insulation solutions.
Fiberglass, a composite material made from fine glass fibers and resin, is mainly used in industries such as construction, automotive, aerospace, and marine. In construction, it’s commonly found in insulation, roofing materials, and reinforced concrete, providing excellent strength-to-weight ratios and resistance to moisture. In the automotive industry, fiberglass is utilized for making body panels and components, contributing to lighter vehicles that improve fuel efficiency. Aerospace applications also leverage fiberglass for lightweight parts in aircraft, enhancing performance and reducing fuel consumption. In marine settings, fiberglass is favored for boat hulls due to its resistance to water and corrosion. Additionally, fiberglass finds uses in electrical applications, such as insulators and circuit boards, thanks to its electrical insulation properties. Its versatility and durability make fiberglass an essential material across numerous sectors.
Fiberglass sheeting is a versatile material used in various industries due to its strength, durability, and lightweight properties. It is commonly used for roofing, cladding, and skylights in buildings, offering weather resistance and natural light diffusion. Industrial applications include protective barriers, wall panels, and equipment enclosures. In the automotive and aerospace industries, fiberglass sheets are used to manufacture vehicle body panels, aircraft interiors, and composite structures due to their high strength-to-weight ratio. They are also widely utilized in marine applications, such as boat hulls and decks, because of their corrosion resistance. Additionally, fiberglass sheets serve as an electrical insulator in circuit boards and switchgear panels, making them valuable in the electrical industry. Other uses include signage, greenhouse panels, and DIY projects where a strong, weather-resistant material is needed. Their adaptability across various industries makes fiberglass sheets a popular choice for both commercial and residential applications.
Fiberglass sheets have a broad range of applications across multiple industries. In construction, they are used for roofing, walls, and insulation panels due to their durability and thermal resistance. Industrial applications include protective coverings for machinery, chemical-resistant panels, and lightweight structural components. The automotive industry utilizes fiberglass sheets for car body panels, RV exteriors, and reinforced bumpers. Aerospace manufacturers use fiberglass for interior panels, ducts, and lightweight composite structures. Marine industries rely on fiberglass sheets for boat hulls, decks, and corrosion-resistant structures. Electrical applications include insulation panels, switchgear components, and circuit boards due to fiberglass’s non-conductive properties. They are also used in agriculture for greenhouse panels, storage sheds, and animal enclosures. In signage and advertising, fiberglass sheets serve as durable backdrops for billboards and displays. Their combination of strength, resistance, and versatility makes them an essential material in various sectors.
Yes, fiberglass sheets are highly waterproof, making them ideal for applications requiring moisture resistance. They are commonly used for roofing, marine structures, and outdoor panels due to their ability to withstand water exposure without deteriorating. The waterproof nature of fiberglass results from its composition—woven glass fibers embedded in a resin matrix, which creates a non-porous and sealed surface. This makes fiberglass sheets suitable for bathrooms, swimming pools, and water tanks where moisture resistance is crucial. However, over time, if the surface coating is damaged or worn out, water infiltration may occur, leading to potential weakening of the structure. To maintain waterproof integrity, protective coatings such as gel coats or sealants can be applied. In construction and industrial applications, fiberglass sheets are preferred over traditional materials like wood or metal because they do not rot, corrode, or absorb moisture, ensuring long-term durability in wet environments.
Yes, fiberglass can get under your skin, causing irritation, itching, and redness. Fiberglass consists of fine glass fibers that can break apart during handling or cutting, creating tiny, almost invisible shards. When these fibers come into contact with the skin, they can embed themselves, leading to discomfort and inflammation. Although fiberglass does not typically cause long-term health effects, exposure can be unpleasant. The irritation is usually mechanical rather than chemical, meaning it results from the fibers physically embedding into the skin rather than causing a chemical reaction. Washing the affected area with cold water and mild soap can help remove fiberglass particles. Avoid rubbing the skin, as this can push the fibers deeper. Wearing protective gloves, long sleeves, and a mask when handling fiberglass sheets can prevent skin contact. If irritation persists or if fiberglass gets into the eyes, medical attention may be necessary.
Yes, fiberglass is still widely used in residential construction due to its excellent insulating properties, affordability, and durability. Fiberglass insulation is one of the most common materials for home insulation, used in walls, attics, and basements to regulate indoor temperatures and improve energy efficiency. Fiberglass sheets are also used for roofing, siding, and skylights due to their weather resistance and lightweight nature. In addition to insulation and structural applications, fiberglass is found in plumbing systems, where it reinforces pipes and water tanks. Modern homes also incorporate fiberglass in doors, window frames, and bathtubs due to its strength and resistance to moisture. While newer insulation alternatives like spray foam and mineral wool are gaining popularity, fiberglass remains a dominant choice in home construction because of its cost-effectiveness, fire resistance, and ease of installation. Its continued use ensures efficient thermal performance and structural reliability in residential buildings.
Fiberglass does not fully break down in the body but can be expelled over time. When fiberglass particles enter the skin, they often remain embedded for a short period before the body naturally sheds the affected skin cells. If inhaled, fiberglass fibers can become trapped in the respiratory system, leading to temporary irritation. The body may gradually expel these fibers through mucus and coughing. However, prolonged or excessive exposure to airborne fiberglass dust could potentially cause respiratory issues, particularly in individuals with pre-existing lung conditions. Unlike materials such as asbestos, fiberglass does not persist indefinitely in lung tissue, and studies suggest it is less likely to cause severe long-term damage. Wearing protective equipment like gloves, masks, and goggles when handling fiberglass minimizes exposure. If irritation or respiratory symptoms persist after fiberglass exposure, medical consultation may be necessary to assess any potential complications.
Yes, fiberglass fibers that get embedded in the skin often fall out on their own as the body naturally sheds dead skin cells. However, the process may take a few days, during which the affected area can remain itchy or irritated. Washing the skin gently with cold water and mild soap can help remove loose fibers. Avoid scrubbing or using warm water, as this can open pores and allow fibers to penetrate deeper. If fiberglass particles remain stuck, adhesive tape can sometimes lift them from the skin. In cases where fiberglass is deeply embedded, tweezers may be needed to remove visible fibers. If the irritation persists or becomes infected, a doctor should be consulted. When inhaled, fiberglass particles may be expelled through mucus and coughing over time. To prevent exposure, wearing protective clothing and masks when handling fiberglass materials is highly recommended.
Fiberglass does not degrade easily and can last for decades if properly maintained. It is resistant to corrosion, moisture, and temperature fluctuations, making it an extremely durable material. However, prolonged exposure to UV radiation, extreme weather, or chemical exposure can weaken the resin binding the glass fibers, causing fiberglass sheets to become brittle and less effective over time. Fiberglass insulation, while long-lasting, can lose its effectiveness if it becomes compressed or contaminated with moisture. If stored incorrectly, fiberglass sheets may warp or lose their original strength. Protective coatings or resins can extend the lifespan of fiberglass products by preventing degradation. While fiberglass does not rot or rust like wood or metal, its performance can decline under certain conditions. Regular inspections and maintenance, such as reapplying protective coatings, can help preserve its integrity and ensure long-lasting performance in various applications.
Fiberglass insulation itself does not support mold growth because it is made of inorganic glass fibers. However, if it becomes wet, moisture can create an environment conducive to mold growth on surrounding materials such as wood, drywall, or dust trapped within the insulation. Wet fiberglass insulation also loses its thermal resistance, making it less effective at insulating a home. If insulation becomes damp due to leaks or flooding, it should be dried thoroughly or replaced to prevent mold growth and structural damage. In cases where moisture exposure is frequent, closed-cell spray foam or rigid foam insulation may be better alternatives, as they are more resistant to water absorption. To protect fiberglass insulation from moisture, proper vapor barriers and adequate ventilation should be installed. Regularly checking for leaks in roofs, pipes, and basements can also help prevent insulation from becoming a breeding ground for mold.
Yes, fiberglass particles that are inhaled can eventually leave the lungs. The body has natural mechanisms, such as mucus production and coughing, to expel foreign particles, including fiberglass fibers. Most inhaled fiberglass dust is trapped in the upper respiratory tract and expelled through coughing or swallowed and eliminated through the digestive system. However, prolonged exposure to airborne fiberglass particles can cause temporary respiratory irritation, including coughing, throat irritation, and shortness of breath. While fiberglass is less harmful than asbestos, excessive exposure should still be avoided. Wearing masks or respirators when working with fiberglass materials reduces the risk of inhalation. If someone experiences persistent respiratory symptoms after fiberglass exposure, medical evaluation is recommended. Long-term exposure to fiberglass dust, especially in poorly ventilated areas, can increase the risk of lung irritation, making protective measures essential when handling or cutting fiberglass sheets.
Yes, fiberglass is generally stronger than wood, especially in terms of tensile strength, durability, and resistance to environmental factors. Fiberglass sheets do not warp, rot, or degrade like wood when exposed to moisture, making them ideal for outdoor and marine applications. Additionally, fiberglass is resistant to pests, mold, and fire, giving it an advantage over wood in long-term structural applications. Its lightweight nature combined with high strength makes it a preferred material in construction, automotive, and aerospace industries. However, wood has advantages in flexibility and ease of repair, whereas fiberglass can become brittle over time if exposed to excessive UV radiation. While fiberglass excels in strength and durability, wood remains a cost-effective and traditional building material for structures requiring natural aesthetics. Choosing between fiberglass and wood depends on the specific application, environmental conditions, and budget considerations.
The choice between foam board and fiberglass depends on the intended application. Fiberglass sheets are stronger, more durable, and resistant to environmental damage, making them ideal for roofing, construction panels, and marine applications. They provide excellent impact resistance and structural integrity. Foam board, on the other hand, is lightweight and offers better thermal insulation, making it suitable for insulating walls, roofs, and HVAC systems. However, foam board lacks the mechanical strength of fiberglass and is more susceptible to damage from physical impact and prolonged exposure to moisture. Fiberglass is often preferred for applications requiring structural support and longevity, whereas foam board is commonly used for insulation purposes. If a project requires durability and resistance to harsh conditions, fiberglass is the better choice. If the main goal is insulation and lightweight handling, foam board may be more suitable.
Yes, having exposed fiberglass can be problematic, particularly in environments where people may come into direct contact with it. Fiberglass consists of tiny glass fibers that can become airborne or embed into the skin, causing irritation, itching, and discomfort. Inhaling fiberglass particles can lead to respiratory irritation, coughing, and throat discomfort. Exposed fiberglass insulation in homes, for example, can deteriorate over time, releasing fibers into the air and posing health risks. Covering fiberglass sheets with a protective layer, such as paint, resin coatings, or paneling, can help prevent exposure. In industrial settings, fiberglass panels are often laminated or reinforced with protective coatings to minimize fiber release. Proper handling, including wearing gloves, long sleeves, and masks, is essential when working with exposed fiberglass. If fiberglass is used in an area with frequent human contact, sealing or covering it is recommended to ensure safety and longevity.
Pros:
Strength & Durability: Fiberglass is strong, impact-resistant, and does not warp or rot like wood.
Water & Corrosion Resistance: Ideal for outdoor, marine, and industrial applications where moisture is a concern.
Lightweight: Offers a high strength-to-weight ratio, making it useful in construction, automotive, and aerospace industries.
Electrical Insulation: Fiberglass sheets are non-conductive, making them safe for electrical applications.
Versatile Applications: Used in roofing, wall panels, boats, aircraft, automotive parts, and insulation.
Cons:
Brittleness: Over time, fiberglass can become brittle, especially with prolonged UV exposure.
Irritation Risks: Handling fiberglass without protection can cause skin irritation and respiratory issues.
Higher Cost: Fiberglass sheets can be more expensive than traditional materials like wood or plastic.
Difficult Repairs: Unlike wood, fiberglass repairs require specialized resins and coatings.
Despite some drawbacks, fiberglass remains a preferred material in industries requiring strength, durability, and resistance to environmental damage.
Several coatings and materials can be applied to fiberglass sheets to enhance their durability and protect them from environmental damage. Gel coats are commonly used to provide a smooth, glossy, and UV-resistant finish, preventing fiberglass from becoming brittle over time. Paints and sealants, such as epoxy-based or polyurethane coatings, can be used to shield fiberglass from moisture, chemical exposure, and wear. For industrial applications, fiberglass-reinforced plastic (FRP) coatings are applied to increase strength and chemical resistance. In marine applications, marine-grade varnishes and anti-fouling coatings help protect boat hulls from water damage. UV-protective films can also be applied to fiberglass roofing and panels to prevent degradation from sunlight. Choosing the right protective layer depends on the specific environment and intended use of the fiberglass sheet, ensuring longevity and maintaining structural integrity in harsh conditions.
Fiberglass duct boards typically have a lifespan of 20 to 30 years when properly maintained. These duct boards, used in HVAC systems, offer excellent thermal insulation and noise reduction. However, their longevity depends on factors like exposure to moisture, air quality, and mechanical damage. If fiberglass duct boards are exposed to excessive humidity or water leaks, they can degrade faster and become a breeding ground for mold and bacteria. Regular maintenance, such as inspecting for signs of damage, keeping the ducts dry, and ensuring proper ventilation, can extend their lifespan. Unlike metal ducts, fiberglass duct boards do not rust, but they can lose their insulating properties if compressed or damaged. Over time, the binder holding the fibers together may weaken, leading to fiber shedding and reduced efficiency. In such cases, replacement or sealing with protective coatings may be necessary to maintain performance.
If fiberglass sheets or insulation become wet, they do not cure or regain their original strength on their own. While fiberglass itself does not absorb water, prolonged exposure to moisture can weaken the resin that binds the fibers, causing structural degradation over time. If fiberglass sheets are used in construction or marine applications, allowing them to dry and applying a resin sealant or waterproof coating can help restore some integrity. However, fiberglass insulation, once soaked, loses its thermal efficiency and should be replaced if it remains damp for an extended period. In cases where fiberglass resin is applied during manufacturing or repair, it must cure in dry conditions; excess moisture can prevent proper hardening and result in a weak, ineffective bond. To ensure fiberglass remains durable, it is essential to protect it from prolonged water exposure and apply protective coatings when necessary.
Yes, fiberglass sheets are significantly stronger than standard plastic. Fiberglass has a much higher tensile strength and is reinforced with glass fibers, making it more durable and impact-resistant. Unlike plastic, which can crack or deform under pressure, fiberglass retains its shape and structural integrity under heavy loads. This makes fiberglass sheets ideal for construction, automotive, marine, and aerospace applications. In comparison to thermoplastics, which soften under heat, fiberglass maintains stability at higher temperatures. It also resists corrosion, moisture, and UV damage better than many plastics. While fiberglass is slightly more brittle than some flexible plastics, its superior strength, durability, and heat resistance make it a preferred choice for demanding applications where plastic would fail.
Yes, fiberglass sheets are highly heat-resistant. They can withstand temperatures up to 1,100°F (593°C) before softening, depending on the resin type used. This makes them ideal for applications that require thermal insulation, such as roofing, automotive components, and industrial equipment. Heat-resistant fiberglass sheets are often used in areas exposed to high temperatures, such as engine compartments, furnaces, and aerospace structures. However, while the glass fibers themselves can tolerate extreme heat, the resin matrix binding them may degrade at lower temperatures. Fire-retardant or high-temperature resins can enhance heat resistance, making fiberglass sheets more suitable for demanding environments. Due to their heat-resistant properties, fiberglass sheets are preferred for applications where materials must endure high temperatures without significant structural compromise.
Fiberglass sheets are not entirely fireproof but are highly fire-resistant. Fiberglass itself has a melting point of around 1,100°F (593°C), making it much more heat-resistant than many other materials. However, the resin used to bind fiberglass fibers can be combustible at lower temperatures. To enhance fire resistance, manufacturers often use fire-retardant resins or coatings. Fire-resistant fiberglass sheets are used in construction, aerospace, and industrial applications where heat and flame exposure are concerns. Some variants meet strict fire safety standards and are used in protective barriers, insulation panels, and fireproof doors. While fiberglass sheets can withstand high temperatures, they should not be exposed to direct flames for extended periods without protective coatings. Choosing fire-rated fiberglass sheets ensures better protection in applications requiring flame resistance.
No, fiberglass is not as hazardous as asbestos. While both materials are used for insulation and construction, asbestos is highly toxic and known to cause lung diseases, including mesothelioma and asbestosis. Fiberglass, on the other hand, does not have the same long-term health effects. When cut or disturbed, fiberglass dust can cause temporary skin, eye, and respiratory irritation, but it does not stay in the lungs permanently like asbestos fibers. Fiberglass sheets are widely used in roofing, automotive, and marine applications because they provide strength and insulation without severe health risks. Unlike asbestos, which is strictly regulated and removed from buildings due to health concerns, fiberglass remains a safe and effective material when handled correctly. Using proper protective equipment when cutting fiberglass sheets can prevent irritation, ensuring safe use in construction and manufacturing industries.
Fiberglass is not classified as a carcinogen, but prolonged exposure to airborne fiberglass dust may pose health risks. Unlike asbestos, fiberglass does not remain in the lungs permanently. However, frequent inhalation of fiberglass particles may cause respiratory irritation, coughing, and discomfort. Workers handling fiberglass sheets in construction, automotive, or industrial settings should wear protective masks and ensure proper ventilation. Skin exposure to fiberglass fibers can cause itching and irritation, but these effects are temporary and subside once fibers are removed. While some studies suggest that excessive inhalation over long periods might contribute to lung issues, there is no conclusive evidence linking fiberglass to cancer. When used in sheets, fiberglass poses minimal risk, as fibers are encased in resin and unlikely to become airborne unless cut or sanded. Proper handling, protective gear, and workplace safety regulations help minimize any potential health risks associated with fiberglass exposure.
Proper disposal of fiberglass sheets depends on local regulations. Small pieces can be disposed of in regular trash, but larger sheets may require special handling. Fiberglass is not biodegradable, so recycling is the best option if facilities exist. Some recycling centers process fiberglass into new composite materials for construction or industrial use. If disposal is necessary, wrapping fiberglass in plastic sheets prevents fiber dispersion. When handling old fiberglass, wearing protective gloves, masks, and clothing is essential to avoid skin irritation and inhalation of loose fibers. In cases of large-scale removal, such as boat hulls or roofing panels, professional waste disposal services may be required. Fiberglass sheets used in construction and automotive industries should be disposed of responsibly to minimize environmental impact. By seeking eco-friendly disposal options, fiberglass waste can be repurposed rather than ending up in landfills.
Fiberglass sheets are incredibly strong and can withstand significant pressure without breaking. Their strength varies based on thickness, resin type, and reinforcement used. A standard fiberglass sheet has a tensile strength of about 20,000 to 50,000 psi (pounds per square inch), making it stronger than many metals of the same weight. This high strength-to-weight ratio makes fiberglass sheets ideal for structural applications in aerospace, automotive, and construction industries. Unlike metal, fiberglass does not corrode, making it an excellent material for outdoor and marine applications. Reinforced fiberglass sheets, such as those with carbon fiber or additional resin layers, can offer even greater durability and impact resistance. Their ability to withstand high loads while remaining lightweight makes them suitable for roofing, panels, and protective covers. Fiberglass sheets provide a balance of strength, flexibility, and durability, making them a preferred material in various industries.
The drying time of fiberglass depends on the type of resin used, temperature, and humidity. Polyester and epoxy resins, which bind fiberglass fibers together, typically take 2 to 12 hours to dry to the touch and 24 to 72 hours to fully cure. In warm, dry conditions, the drying process is quicker, whereas cold or humid environments slow it down. Fiberglass sheets used in construction or automotive applications often require full curing before they can bear loads or be painted. Some industrial applications use heat curing to accelerate the process, ensuring maximum strength in a shorter time. When installing fiberglass sheets for roofing, boats, or vehicles, allowing proper drying time ensures durability and structural integrity. If fiberglass sheets are not fully cured before use, they may remain soft, sticky, or prone to damage.
Yes, fiberglass sheets can weaken over time due to factors like UV exposure, moisture absorption, and mechanical stress. Though fiberglass is highly durable, prolonged exposure to direct sunlight can cause the resin to break down, leading to discoloration and brittleness. In humid or wet environments, unsealed fiberglass may absorb moisture, weakening its structural integrity. Additionally, mechanical wear from continuous pressure or impact can lead to cracks or delamination. However, with proper maintenance and protective coatings, fiberglass sheets can last for decades without significant degradation. Fiberglass sheets are widely used in construction, boat manufacturing, automotive applications, and industrial settings because of their strength and longevity. Regular inspections, refinishing, and protective measures such as UV-resistant coatings and water sealants can significantly extend the lifespan of fiberglass sheets, ensuring they remain structurally sound for years.
No, fiberglass sheets do not melt in hot water. Fiberglass is made from fine glass fibers bonded with resin, making it highly heat-resistant. While exposure to hot water may degrade the resin over time, the glass fibers themselves will not melt unless subjected to extremely high temperatures, well beyond boiling water. However, prolonged exposure to hot water can weaken the adhesive properties of the resin, reducing the sheet’s overall strength. This is why fiberglass sheets are commonly used in marine, roofing, and insulation applications, where exposure to moisture and temperature fluctuations is expected. To maintain the integrity of fiberglass sheets, they should be coated with water-resistant finishes or protective layers when used in environments with constant water exposure. Proper maintenance ensures durability, preventing the sheet from becoming brittle or weakened due to prolonged heat and moisture exposure.
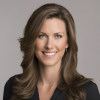
As the editor of GangLong Fiberglass, I have years of experience and in-depth research, focusing on cable tray products, fiberglass solutions, and grille systems. I incorporate years of industry insights and practical experience into every content, committed to promoting the progress of the industry. At GangLong Fiberglass, my commitment is reflected in every product, from innovative cable trays to durable fiberglass solutions and sturdy grille systems. As an authoritative voice in the industry, my goal is to provide valuable information to professionals and businesses and promote forward-looking solutions.