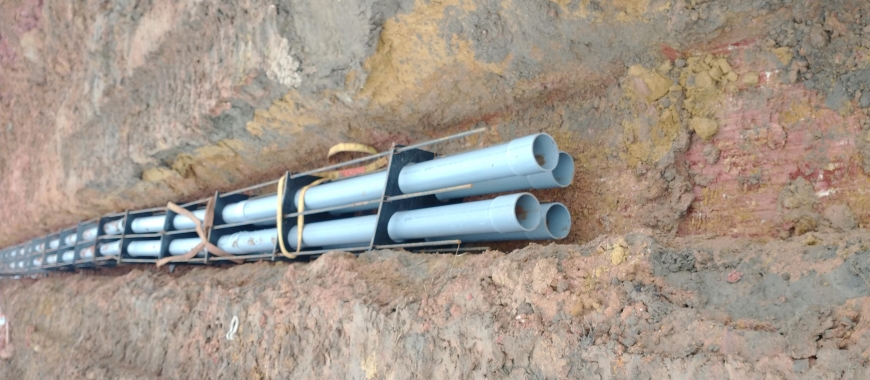
FRP (Fiberglass Reinforced Plastic) has become a crucial material in modern engineering and construction. It offers a unique combination of strength, durability, and lightweight properties. As industries evolve, the demand for innovative solutions grows, making FRP increasingly relevant. One notable application is the FRP cable threading pipe, designed to protect and facilitate the installation of cables in various environments, similar to the use of FRP cable tray systems that offer structural support and protection. Its excellent corrosion resistance and thermal insulation make it ideal for sectors like telecommunications and energy. With growing emphasis on sustainability and efficiency, FRP products continue to offer advantages over traditional materials. This innovative solution is transforming how we approach cable management in complex projects. The FRP cable threading pipe is lightweight, strong, corrosion-resistant, flame-retardant, and protects power and communication cables.
What is FRP Cable Threading Pipe
Manufacturers design the FRP cable threading pipe as a conduit to protect cables and streamline installation in various environments. This innovative solution combines the lightweight and durable characteristics of fiberglass with advanced engineering techniques. For instance, China FRP cable threading pipe has become a prominent choice in the industry due to its superior strength, corrosion resistance, and reliability. Here are key aspects of FRP cable threading pipe definition and primary function.
Key Features
FRP cable threading pipes, made from fiberglass reinforced with a resin matrix, offer a durable, lightweight solution for cable protection. These pipes are corrosion-resistant, easy to install, and provide excellent thermal insulation. Their longevity and ability to withstand harsh conditions make them ideal for industrial, commercial, and residential cable management.
Material Composition
Manufacturers use fiberglass and resin to construct FRP cable threading pipes, which offer high mechanical strength and low weight. This combination enhances the pipes’ durability while making them easy to handle and install. The resin provides flexibility, while the fiberglass ensures resistance to mechanical damage, creating a reliable and lightweight piping solution.
Corrosion Resistance
FRP cable threading pipes offer exceptional corrosion resistance, especially in environments exposed to moisture, chemicals, or saltwater. Unlike metal pipes, which rust, FRP pipes maintain their integrity in harsh conditions. This corrosion resistance ensures long-lasting performance, making them ideal for marine, chemical, and underground installations.
Thermal Insulation
FRP cable threading pipes have low thermal conductivity, providing excellent insulation for the cables. This insulation prevents overheating and protects electrical components from temperature fluctuations. It ensures efficient operation in environments with high thermal stress, such as power plants and industrial settings.
Smooth Interior
The smooth inner surface of FRP pipes reduces friction during cable installation. This allows cables to pass through with minimal resistance. It reduces cable damage risk, speeds up installation, and lowers labor costs. The process improves efficiency in various environments.
Versatile Applications
FRP cable threading pipes are adaptable for use in telecommunications, energy, and industrial applications. Their flexibility allows for both underground and overhead installations, making them suitable for a wide range of environmental conditions and project requirements, from outdoor construction to harsh industrial settings.
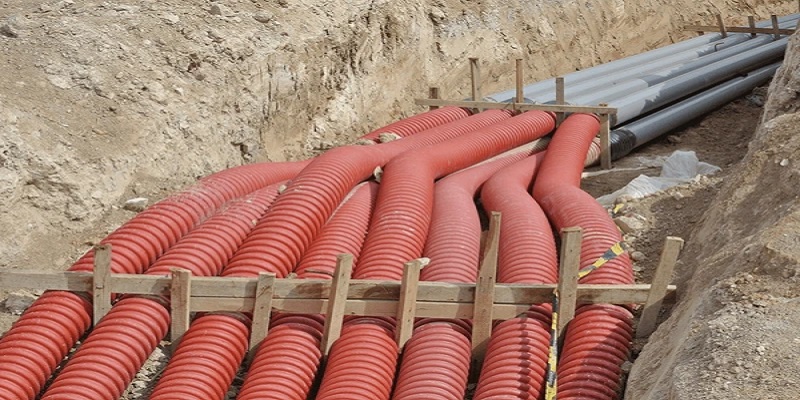
Elastomeric Coating: The Role of Fiberglass Tape
The Manufacturing Process of FRP Cable Threading Pipes
The manufacturing of FRP cable threading pipe involves a meticulous process that combines high-quality materials and cutting-edge technology to produce durable and reliable products suitable for various applications.
Step 1: Selection of Materials
The first step involves selecting the right type of materials. High-strength fiberglass and resins such as polyester or epoxy are the main components. The choice of materials affects the pipe’s final properties, including its strength, flexibility, and resistance to environmental factors.
Step 2: Cutting and Preparing Fiberglass
Manufacturers cut the fiberglass strands to the correct length and prepare them based on the specifications of the FRP cable threading pipe to be made. This preparation ensures that the fiberglass bonds properly with the resin to create a strong composite material.
Step 3: Immersion of Fiberglass
The cut and prepared fiberglass strands are immersed in a resin fiberglass bath tube. This step is crucial as it ensures that each strand of fiberglass is completely coated with resin, making it possible to achieve the desired degree of durability and resistance in the final product.
Step 4: Molding
Manufacturers thoroughly coat the fiberglass strands with resin, then wind them around a mandrel or pass them through an extrusion process, depending on the desired shape and thickness of the FRP cable threading pipe. This step forms the actual shape of the pipe.
Step 5: Curing Process
Once the resin-coated fiberglass is in place, the pipe undergoes a curing process. This involves heating the pipe in a controlled environment to harden the resin. Curing transforms the resin and fiberglass into a solid, robust structure, similar to a solid fiberglass pole, giving the FRP cable threading pipe its final strength and durability.
Step 6: Cooling
After curing, the FRP pipe is allowed to cool at a controlled rate. This stage is vital to prevent the formation of internal stresses that could weaken the pipe.
Step 7: Removal from the Mold
Once cooling is complete, manufacturers carefully remove the FRP cable threading pipe from the mold or mandrel. They must do this with precision to ensure the pipe maintains its shape and structural integrity.
Step 8: Finishing Touches
The last step involves finishing touches like cutting the FRP cable threading pipe to length, drilling holes if necessary, and conducting quality assurance tests. These tests assess the pipe’s strength, flexibility, and resistance to ensure it meets all required standards and CSI specifications FRP pipe.
Precautions in the Manufacturing Process of FRP Cable Threading Pipe
The manufacturing process of FRP cable threading pipes involves several critical steps, including material selection, mold design, curing, and quality control. Each phase plays a significant role in ensuring the pipes’ strength, durability, and overall performance.
Material Selection and Preparation
Choosing the right raw materials is crucial for durability and performance. The resin should suit the environmental conditions, like polyester for standard applications or vinyl ester for demanding ones. Manufacturers must use high-quality fiberglass reinforcement and distribute it uniformly. This ensures consistent mechanical properties and strength throughout the pipe.
Mold Design and Maintenance
Accurate mold design is essential to ensure that FRP pipes meet the required specifications. Clean and maintain molds before production to prevent contamination and defects. Proper mold dimensions and uniform pipe thickness are necessary to avoid inconsistencies. Inconsistencies can compromise the pipe’s strength and durability.
Environmental Control
The manufacturing environment plays a vital role in the quality of FRP pipes. Manufacturers must carefully regulate factors like temperature and humidity to prevent curing issues. Excessive humidity can affect resin bonding, while temperature fluctuations can cause incomplete curing or brittleness. Maintaining a clean, controlled environment ensures consistency and allows the resin to set correctly.
Curing and Post-Curing Process
Curing is critical to the pipe’s strength. Manufacturers must heat the resin at specific temperatures and times to ensure proper bonding with fiberglass. Inadequate curing results in soft, weak pipes, while over-curing causes brittleness. Post-curing may enhance the pipe’s thermal stability and resistance to impact, ensuring long-lasting durability, especially in high-stress environments.
Quality Control and Testing
Regular quality control checks, including visual inspection, mechanical testing, and environmental resistance tests, are essential. These tests ensure the pipes meet specifications for strength, corrosion resistance, and heat tolerance. Visual inspections identify surface defects. Mechanical tests, like flexural strength and impact resistance, confirm the pipe’s ability to withstand stress. Environmental tests, such as temperature cycling, verify performance under extreme conditions.
Finishing and Packaging
Once the pipes pass quality control, manufacturers complete a finishing process to enhance their surface quality and make installation easier. If needed, they apply protective coatings to provide additional resistance to UV light and chemicals. Proper packaging ensures protection during transportation. Manufacturers securely wrap and cushion the pipes to avoid scratches or deformation.
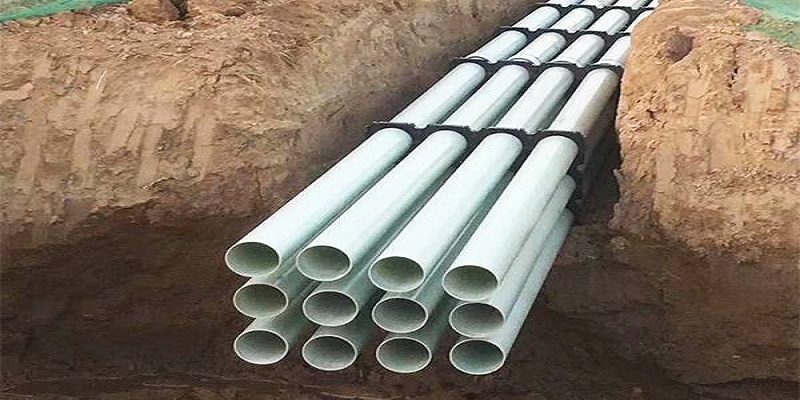
Applications of FRP Cable Threading Pipe
FRP cable threading pipes are widely used in various industries due to their unique properties. These pipes offer superior cable protection, durability, and installation efficiency. Their versatility makes them ideal for applications in sectors where high reliability and performance are essential, ensuring cable protection against environmental stressors, chemical exposure, and mechanical damage.
Telecommunications
FRP cable threading pipes protect fiber optic cables in both underground and overhead installations. These pipes ensure signal integrity and longevity by safeguarding cables from moisture, physical damage, and environmental factors. They are essential for maintaining the performance of communication networks and preventing disruptions in services due to cable wear and damage.
Energy (Power Generation & Renewable Energy)
In power generation plants and renewable energy sites like wind and solar farms, FRP pipes protect electrical wiring and control cables. Their resilience to harsh weather conditions, high temperatures, and chemical exposure ensures the continuous operation of energy systems, reducing the risk of damage and enhancing overall system reliability.
Construction
FRP cable threading pipes are widely used to manage electrical systems in residential and commercial buildings. These pipes provide a reliable conduit for cables, ensuring protection from environmental hazards. By meeting safety regulations and building codes, FRP pipes ensure safe and compliant installations while minimizing cable damage risks.
Oil and Gas
In refineries and offshore platforms, FRP cable threading pipes protect cables from extreme temperatures, chemicals, and moisture. These pipes maintain the integrity of electrical and communication systems, ensuring operational safety in harsh industrial environments. Their durability and resistance to corrosion make them ideal for demanding oil and gas applications.
Manufacturing
In manufacturing plants, FRP pipes help route electrical and control cables safely, preventing damage. These pipes contribute to maintaining operational efficiency by minimizing downtime caused by cable failures. Their resistance to environmental stressors helps ensure that electrical systems in industrial plants remain operational and safe over the long term.
Water Treatment
FRP cable threading pipes protect sensors and electrical components in water treatment facilities. By ensuring reliable monitoring and control of water quality, they contribute to maintaining public health and environmental protection. These pipes ensure that critical systems continue to operate smoothly despite exposure to harsh conditions and chemicals.
Fiberglass Columns Price at Home Depot: What to Expect
Wholesale FRP Cable Threading Pipe Exporter and Manufacturer
The global market for FRP (Fiberglass Reinforced Plastic) cable threading pipes is expansive, providing broad opportunities for exporters. These pipes, renowned for their strength, durability, and resistance to corrosion, are in high demand in various sectors, including telecommunications, power distribution, and industrial construction. Wholesale FRP cable threading pipe exporters play a pivotal role in bridging the gap between manufacturers and the international market, ensuring a steady flow of these essential components to regions where demand is highest.
Understanding the Export Market for FRP Cable Threading Pipes
The export landscape for FRP cable threading pipes includes a diverse range of markets, each with unique requirements and regulations. Among the notable players in this field is “GangLong Fiberglass,” a company that has established itself as a key figure in the global supply chain for FRP products. GangLong Fiberglass and similar exporters leverage their expertise and networks to meet the global demand efficiently. Three primary facets characterize the export market for these products:
- Global Demand Variability: The requirement for FRP cable threading pipes varies significantly across different regions, influenced by developmental projects, upgrades in infrastructure, and advancements in telecommunications and power distribution networks.
- Regulatory Compliance: Exporters must navigate the complex web of international standards and regulations. This includes ensuring that products meet the specific construction and material standards set by various countries and international bodies.
- Logistical Efficiency: The ability to manage logistics effectively, from production to delivery, is crucial. This includes optimizing shipping routes, managing customs clearance, and ensuring timely delivery to meet project deadlines.
Challenges and Considerations in Exporting These Products
Exporting FRP cable threading pipes involves navigating various challenges that can impact the success of international transactions and the satisfaction of global customers. Manufacturers and exporters must carefully address these hurdles to ensure smooth operations, compliance with international standards, and a strong market presence. Here, we expand on the challenges that exporters face and offer insights into how they can overcome them effectively.
Quality Assurance Across Borders
One of the biggest challenges in exporting FRP cable threading pipes is ensuring consistent product quality that meets both the manufacturer’s internal standards and the regulations of the importing country. Different countries may have varying technical standards, certifications, and quality expectations, which complicate the export process. To overcome this, exporters must stay up-to-date with international regulations and test and certify their products accordingly. Building a reputation for high-quality, compliant products is key to maintaining customer trust in international markets.
Cultural and Language Barriers
Exporting to international markets often involves overcoming cultural and language differences, which can pose challenges in communication and understanding client needs. Different business practices, negotiation styles, and consumer expectations across regions require exporters to adopt culturally sensitive approaches. To mitigate this, establishing local partnerships, employing bilingual staff, and conducting market research into the target culture can significantly improve communication and help in tailoring products and services to meet local preferences. Understanding the customs and etiquette of the target market can make a significant difference in building long-lasting business relationships.
Currency Fluctuations and Payment Risks
Exporters often face exposure to currency fluctuations when dealing in international markets. Exchange rate volatility affects profit margins and leads to unexpected costs, especially with large transactions. Additionally, international banking systems’ complexity and the risk of delayed or unsecured payments pose further challenges. To mitigate these risks, exporters can use strategies like currency hedging, work with international banks that understand the target country’s regulations, and require partial payments or letters of credit to secure financial transactions.
Shipping and Logistics Challenges
Shipping and logistics can be a significant obstacle in international trade. Exporters often face delays due to unforeseen circumstances like extreme weather, political instability, or disruptions in supply chains. Long distances between the manufacturing location and the destination country can lead to increased costs, delays, or even damage to products during transit. To address this, exporters should establish reliable logistics partnerships, insure shipments against damage, and maintain communication with transport providers to track the movement of goods. Having contingency plans in place for delays or shipping issues is also essential for maintaining customer satisfaction.
FRP Cable Threading Pipe Manufacturer
Innovative Material Compositions
Manufacturers differentiate themselves by developing unique resin formulas or composite materials. These innovations improve the performance of FRP cable threading pipes, including enhanced durability, chemical resistance, and environmental protection. Customizing materials allows manufacturers to offer pipes that provide superior protection for cables in various industrial applications, extending service life and improving overall performance.
Customization Capabilities
Offering custom-tailored solutions helps meet specific client needs. This includes providing custom dimensions, shapes, or enhanced physical properties for unique project requirements. Customization allows manufacturers to create pipes suited for extreme conditions like marine environments or underground installations, ensuring that the products perform efficiently under the specific demands of each application.
Sustainability Practices
Sustainability is becoming a key differentiator for manufacturers. By utilizing recyclable materials, adopting energy-efficient processes, and developing eco-friendly resins, manufacturers reduce environmental impact. FRP pipes made with sustainable practices contribute to a greener environment while providing durable and reliable cable protection, appealing to clients focused on sustainability in their projects.
Technological Advancements
Investing in modern manufacturing technologies helps improve precision and efficiency. Automation and quality control techniques enable manufacturers to produce high-quality FRP pipes with minimal defects. By staying ahead of technological trends, manufacturers optimize production, reduce waste, and offer products with enhanced performance characteristics, which lead to more reliable, cost-effective solutions.
Superior Installation Support
Manufacturers that provide comprehensive installation support stand out in the market. Offering guides, on-site assistance, and contractor training ensures that FRP pipes are installed correctly and function as intended. Providing strong installation support helps prevent installation issues and fosters long-term customer relationships, ensuring the reliability and longevity of the piping systems.
Certification and Testing
Achieving certifications from industry bodies such as ISO or UL builds trust with customers. These certifications ensure that FRP cable threading pipes meet high standards for quality, safety, and performance. Rigorous testing also verifies that the pipes can withstand harsh conditions, making them more reliable and reassuring clients about their performance and durability.
Explore The Benefits Of Fiberglass Pilings For Sale For Docks
Inspection and Maintenance of FRP Cable Threading Pipes to Ensure Longevity and Performance
Regular inspection and maintenance of FRP cable threading pipes are essential to ensure their long-term functionality and to maximize their service life. These pipes are used in challenging environments, where they are exposed to various physical, chemical, and environmental factors. Proper inspection allows early identification of potential issues such as cracks, corrosion, or improper installation, while timely maintenance ensures the pipes continue to operate at peak performance. This section will explore the essential steps and precautions involved in inspecting and maintaining FRP cable threading pipes to ensure they provide durable and reliable cable protection throughout their lifecycle.
Inspection of FRP Cable Threading Pipes
Inspection is the first step in identifying any potential problems with FRP cable threading pipes. Regular visual checks and more detailed assessments are necessary to detect any wear, damage, or signs of weakness that could compromise the performance of the pipes. By performing thorough inspections, any issues can be addressed promptly to prevent further damage.
Visual Inspection for Surface Damage
The most common inspection method is a visual examination of the FRP cable threading pipes. This involves checking the pipes for any surface damage, including cracks, scratches, abrasions, or deformations that may have occurred due to mechanical stress or environmental factors.
- Look for cracks or splits: Cracks along the length of the pipe can lead to structural failure, which might allow moisture or other damaging elements to affect the internal cables.
- Check for discoloration: Fading or discoloration can indicate UV degradation, which weakens the material.
- Inspect for signs of impact: Dents or dents from physical impacts should be noted, as they can compromise the integrity of the pipe.
Internal Inspection
Occasionally, a more thorough internal inspection may be required to ensure there are no internal flaws that could affect the pipe’s function. This might involve using cameras or other specialized tools to check for internal corrosion or blockages that could hinder the passage of cables.
- Check for corrosion or wear inside: In highly corrosive environments, internal corrosion could compromise the structural integrity of the pipe.
- Look for blockage: Make sure the pipe is free of debris or dirt that may obstruct the cables being threaded through.
Maintenance of FRP Cable Threading Pipes
Once any issues have been identified during the inspection phase, maintenance is essential to ensure the FRP cable threading pipes continue to perform optimally. Effective maintenance includes cleaning, repairing damage, and ensuring that all parts of the pipe system remain functional.
Cleaning the Pipes
Cleaning is an essential maintenance task that helps prevent build-up of dirt, debris, or chemicals that could weaken the pipe or cause issues when cables are threaded through.
- Use mild soap or detergent: A gentle cleaning solution should be used to wash the external surface of the pipes. Avoid harsh chemicals that could degrade the material.
- Avoid abrasive tools: Use soft cloths or non-abrasive brushes to avoid scratching the surface of the pipe, which could lead to weakened areas that are prone to further damage.
Repairing Surface Damage
If cracks or chips are found during the inspection, immediate repair is necessary to restore the integrity of the FRP cable threading pipes.
- Patch minor cracks: Small cracks can often be repaired using epoxy-based fillers designed for FRP materials. The repair compound should be applied carefully to ensure it forms a smooth, even surface.
- Reinforce damaged areas: In cases where the damage is more extensive, reinforcing the pipe with additional fiberglass cloth and resin may be required. This helps to restore the pipe’s strength and durability.
Preventative Maintenance
Preventative maintenance can also be performed to avoid future issues, extending the lifespan of the FRP cable threading pipes.
- Apply UV-resistant coatings: To protect against UV degradation, consider applying a protective coating that provides a barrier against sun exposure. This is especially important for outdoor installations where pipes are exposed to sunlight.
- Inspect seals and joints: Check any joints or seals for wear and ensure they are properly fitted to prevent leaks or damage to the pipe.
Precautions During Inspection and Maintenance
Proper precautions must be taken to ensure that the inspection and maintenance processes do not cause further damage to the FRP cable threading pipes. Understanding the specific characteristics of FRP materials is key to performing these tasks without compromising the pipe’s integrity.
Handling the Pipes with Care
Since FRP pipes are strong but can be brittle under certain conditions, it is essential to handle them with care during both inspection and maintenance.
- Avoid excessive force: Do not apply excessive pressure or impact while inspecting or cleaning the pipes, as this could cause cracks or structural damage.
- Wear protective gloves: Handling fiberglass material directly can lead to skin irritation, so it’s important to wear protective gloves during the process.
Avoiding Harsh Chemicals
Avoid using harsh chemicals or abrasive materials during the cleaning process, as they could degrade the FRP cable threading pipes. Instead, stick to mild cleaners specifically designed for use with fiberglass products.
- Use gentle cleaners: Always use cleaners that are compatible with FRP material, as harsh chemicals can break down the resin matrix and weaken the pipes.
Checking for Compatibility of Repair Materials
Always ensure that you use repair materials (such as fillers, resins, or coatings) compatible with the type of resin used in the FRP cable threading pipes if repairs are needed.
- Use manufacturer-recommended repair products: For optimal results, it’s best to use repair products recommended by the pipe manufacturer. This ensures compatibility and avoids introducing materials that may not bond well with the existing FRP structure.
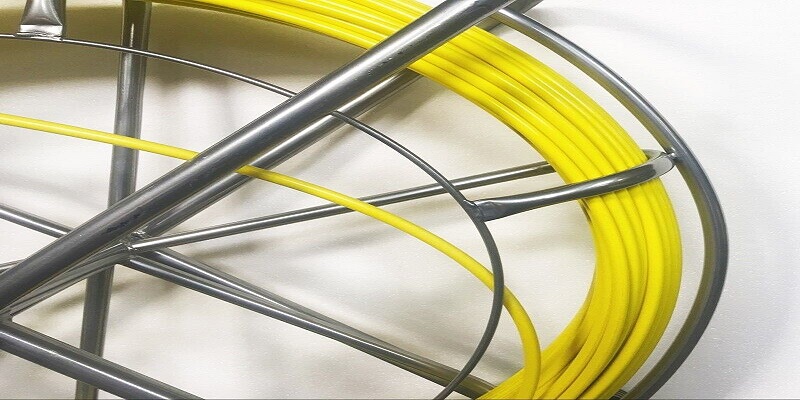
Why Choose FRP Cable Threading Pipes: Key Advantages for Cable Protection
FRP cable threading pipes, made from fiberglass-reinforced plastic, provide excellent protection for cables across various environments. These pipes offer significant advantages such as corrosion resistance, lightweight design, flame retardancy, and heat resistance. Similar to fiberglass reinforced plastic decking, which is known for its durability and resistance to harsh weather conditions, FRP cable threading pipes are built to endure challenging environments. Their durability, ease of installation, and safety features make them a preferred choice for industrial, commercial, and residential cable protection. Below, we’ll explore the benefits of FRP cable threading pipes and explain why they are a superior option for cable management in demanding environments.
Corrosion Resistance
FRP cable threading pipes offer outstanding resistance to corrosion, especially in environments exposed to moisture, saltwater, or chemicals. This ensures that the pipes and cables within remain protected from damage and degradation. Unlike metal pipes, which can rust over time, FRP pipes maintain their integrity, making them ideal for use in marine, industrial, or underground environments. Their corrosion resistance reduces maintenance costs and prolongs the lifespan of both the pipe and the cables it shields.
Durability in Harsh Environments
FRP pipes are highly durable, especially when exposed to harsh environmental conditions like moisture, chemicals, or extreme temperatures. Unlike metal pipes, which can rust and weaken over time, FRP cables resist environmental degradation, ensuring long-lasting protection. This durability makes them ideal for industrial, marine, and underground applications. With reduced wear and tear, FRP cable threading pipes help avoid frequent repairs or replacements, providing a cost-effective solution in the long run.
Ideal for Underground and Marine Applications
FRP cable threading pipes are perfect for underground and marine applications where corrosion is a major concern. The pipes’ corrosion-resistant properties ensure they can withstand exposure to saltwater, moisture, and chemicals, making them an ideal choice for electrical and communication cables in these harsh environments. Unlike metal pipes, which deteriorate in these conditions, FRP pipes maintain their performance, reducing the risk of failure and enhancing the reliability of cable systems in challenging settings.
Lightweight and Easy to Install
FRP cable threading pipes are significantly lighter than their metal counterparts, making them easier to transport, handle, and install. The lightweight nature of FRP pipes reduces the need for heavy lifting equipment, lowering labor costs and simplifying the installation process. Their easy handling also allows for quicker installation in tight or difficult-to-reach spaces. This reduces project time, helping contractors complete cable installations more efficiently while keeping installation costs low.
Flame Retardant and Electrical Insulation
FRP cable threading pipes offer excellent flame-retardant properties, making them a safe option for protecting cables in fire-prone areas. In the event of a fire, these pipes help to prevent the spread of flames through the cable system, improving overall fire safety. Additionally, FRP pipes are non-conductive, offering electrical insulation that protects against potential electrical shorts or shocks. This makes FRP pipes a reliable choice for environments where electrical safety is a top priority, such as in high-voltage or hazardous installations.
Heat Resistance
Manufacturers design FRP cable threading pipes to withstand high temperatures without compromising their structural integrity. This heat resistance is essential in environments like power plants, chemical processing facilities, or industrial machinery, where temperatures often fluctuate. FRP pipes prevent deformation, cracking, or weakening in high-temperature applications, ensuring long-term performance. They protect cables from overheating, helping to maintain the efficiency and functionality of electrical and communication systems even in extreme conditions.
Cost-Effectiveness
While the initial cost of FRP cable threading pipes may be higher than some alternatives, they offer significant long-term savings. Their corrosion resistance and durability reduce the frequency of repairs and replacements, lowering maintenance costs. Additionally, the insulating properties of FRP pipes help reduce energy loss, resulting in lower operational costs. Over time, the durability and minimal maintenance needs of FRP pipes make them a cost-effective investment for cable protection in various applications.
Challenges and Limitations of FRP Cable Threading Pipe
Despite the numerous advantages associated with FRP cable threading pipes, several challenges and limitations can arise. Understanding and addressing these challenges ensures the pipes maintain their intended performance in various environments. Below, we explore common issues and provide ways to mitigate their impact on projects using FRP cable threading pipes.
Brittleness
FRP cable threading pipes are durable but can be more brittle than metal pipes. This makes them vulnerable to cracking, especially when exposed to impact or mishandling. The lack of flexibility in FRP pipes compared to metal options can result in fractures under stress. Proper handling during installation is crucial to avoid this issue and ensure the pipes perform effectively without damage.
Thermal Conductivity
While FRP pipes offer good insulation, their thermal expansion rate is higher than traditional materials like PVC or metal. This difference can lead to stress or leaks when exposed to extreme temperature variations. In applications with fluctuating temperatures, it’s essential to use expansion joints or install the pipes in a way that accommodates the expansion and contraction to prevent damage.
Cost Considerations
FRP cable threading pipes tend to have a higher initial cost compared to PVC or metal pipes. This can create budgeting challenges, particularly for large projects with extensive piping requirements. Although the upfront cost may be higher, the durability, corrosion resistance, and minimal maintenance needs of FRP pipes can lead to significant long-term savings in terms of maintenance and replacement costs.
Fabrication and Repair Complexity
Fabricating or repairing FRP cable threading pipes requires specialized tools and knowledge, which may not be readily available on-site. This can lead to delays and higher costs if repairs or custom fabrications are necessary. Ensuring that the installation team is trained in handling FRP or employing specialized contractors can minimize downtime and help address any fabrication issues effectively.
UV Degradation
Prolonged exposure to UV radiation can degrade the resin in FRP pipes, compromising their structural integrity. Over time, UV exposure can weaken the material, leading to cracks or brittleness. To mitigate UV degradation, FRP pipes used in outdoor or exposed settings should be coated with UV-resistant finishes, or pipes should be chosen with UV-stabilized resins to maintain their strength.
Cable Protection and Installation Methods: FRP Cable Threading Pipe vs Alternatives
When installing and protecting cables in various environments, several solutions can be employed in addition to FRP cable threading pipes. While FRP pipes offer a range of benefits such as corrosion resistance, lightweight design, and heat insulation, other methods may be more suitable depending on the specific requirements of a project, such as cost, environmental conditions, or installation complexity. These alternative methods include PVC (Polyvinyl Chloride) conduits, metallic conduits, rigid electrical tubing (RET), and cable trays.
Method | Advantages | Disadvantages | Best Use Case |
---|---|---|---|
FRP Cable Threading Pipes | Corrosion-resistant, lightweight, heat-insulated | Not ideal for high-temperature environments | Heavy-duty, high-stress industrial applications |
PVC Conduits | Cost-effective, easy installation, non-corrosive | Becomes brittle over time, not suitable for high temperatures | Residential or light commercial applications |
Metallic Conduits | High strength, EMI shielding, fire-resistant | Heavy, prone to corrosion, conducts electricity | High-impact, EMI protection, high-pressure settings |
Rigid Electrical Tubing (RET) | Durable, fire-resistant, strong protection | Heavier, complex installation, prone to corrosion | Impact protection, fire-resistant areas |
Cable Trays | Flexible, good ventilation, easy access | Less physical protection, not ideal for harsh environments | Large commercial, easy cable management |
FAQs about FRP Cable Threading Pipe
FRP piping, or Fiberglass Reinforced Plastic piping, consists of a composite material made from a polymer matrix reinforced with fiberglass. This combination creates a lightweight yet strong and durable piping solution. FRP piping excels in corrosion resistance, making it ideal for transporting chemicals and other fluids in various industries, including oil and gas, water treatment, and construction. Additionally, FRP piping remains flexible, allowing it to withstand changes in temperature and pressure without losing structural integrity. Its smooth inner surface reduces friction losses, enhancing flow efficiency. Furthermore, FRP pipes come in various sizes and pressure ratings, making them suitable for a wide range of applications. As a result, more industries choose FRP piping for its longevity, low maintenance requirements, and environmental benefits compared to traditional materials.
FRP in cable refers to the use of Fiberglass Reinforced Plastic as a protective material for electrical and fiber optic cables. FRP offers several advantages, such as high strength, lightweight, and excellent resistance to corrosion and environmental factors. This makes FRP an ideal choice for cable management in various applications, including telecommunications, construction, and energy. The use of FRP cable threading pipes helps protect cables from physical damage and environmental exposure while maintaining their performance. Additionally, FRP’s non-conductive properties make it a safe option for electrical applications, as it minimizes the risk of short circuits or other electrical hazards. With its ability to endure harsh conditions, FRP enhances the longevity and reliability of cable systems, making it a preferred choice for engineers and project managers seeking durable solutions for cable installations.
The primary difference between FRP and PVC pipes lies in their materials and properties. FRP (Fiberglass Reinforced Plastic) pipes combine a polymer matrix with fiberglass reinforcement, giving them superior strength and durability. In contrast, PVC (Polyvinyl Chloride) pipes are made from a plastic polymer, making them lighter and easier to handle. While both types of pipes offer good corrosion resistance, FRP pipes excel in applications involving harsh chemicals and high temperatures, thanks to their enhanced structural integrity. Additionally, FRP pipes accommodate higher pressure ratings compared to PVC. PVC pipes, however, are often more cost-effective for standard plumbing applications and widely used in residential and commercial settings. Ultimately, the choice between FRP and PVC depends on the specific requirements of the project, including the environment, pressure demands, and chemical exposure.
People often use FRP (Fiberglass Reinforced Plastic) and GRP (Glass Reinforced Plastic) pipes interchangeably, but some distinctions are worth noting.Both types of pipes utilize fiberglass as a reinforcing agent; however, the terminology can differ based on regional preferences and specific applications. Generally, FRP refers to any composite material that incorporates fiberglass and resin, while GRP specifically emphasizes the glass fiber component. The primary difference lies in their manufacturing processes and the types of resins used. FRP pipes may use a variety of resin systems, such as vinyl ester or epoxy, providing flexibility for different applications, whereas GRP pipes typically use polyester resins. In terms of performance, both types of pipes offer excellent corrosion resistance and mechanical strength, making them suitable for transporting fluids in various industries. Ultimately, the choice between FRP and GRP will depend on project requirements, including chemical compatibility, temperature, and pressure ratings.
Several methods join FRP (Fiberglass Reinforced Plastic) pipes, with the choice depending on application requirements, pipe size, and environmental factors. The most common methods include:
Flanged Connections: This method attaches the pipe ends to flanges, which then get bolted together. Flanged connections suit systems requiring frequent disassembly or maintenance, providing a secure, leak-proof seal. They are commonly used in industrial settings.
Threaded Connections: The ends of the FRP pipes get threaded, allowing them to screw together. This method works well for smaller diameter pipes and is convenient for installations in tight spaces or where easy assembly is needed.
Butt Fusion: In butt fusion, manufacturers heat the ends of the pipes and fuse them together, creating a strong, seamless bond. This method creates high-strength joints and is often used for larger pipes in demanding environments.
Adhesive Bonding: Manufacturers bond the pipe ends together using specialized FRP adhesives. This method is simpler and generally used for applications with less pressure or stress.
FRP stands for Fiberglass Reinforced Plastic, a composite material that combines a plastic matrix with fiberglass reinforcement. Manufacturers embed fiberglass fibers, typically made from glass, into the plastic resin, which can consist of materials like epoxy, polyester, or vinyl ester. This reinforcement enhances the material’s strength, durability, and resistance to various environmental factors such as moisture, chemicals, and temperature extremes. FRP remains lightweight yet strong, making it a preferred material for a wide range of applications, including piping systems, construction, automotive parts, and electrical enclosures. FRP excels in harsh conditions where traditional materials like steel r wood might degrade, offering a longer lifespan and reduced maintenance costs.
While FRP (Fiberglass Reinforced Plastic) is a strong and durable material, it is not necessarily stronger than steel in terms of tensile strength. People know steel for its superior strength and ability to withstand high loads and stresses. However, FRP offers several key advantages over steel in specific applications, particularly in terms of weight-to-strength ratio. FRP is much lighter than steel, which makes it easier to handle, transport, and install, especially in large-scale systems like cable threading pipes or industrial piping networks. Additionally, FRP has excellent corrosion resistance, making it a better choice for applications exposed to chemicals, moisture, or saltwater environments, where steel would rust. The unique combination of strength, low weight, and corrosion resistance makes FRP cable threading pipes and similar systems highly effective in industries like oil and gas, marine, and construction, where weight, durability, and environmental resistance are critical factors.
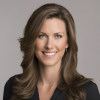
As the editor of GangLong Fiberglass, I have years of experience and in-depth research, focusing on cable tray products, fiberglass solutions, and grille systems. I incorporate years of industry insights and practical experience into every content, committed to promoting the progress of the industry. At GangLong Fiberglass, my commitment is reflected in every product, from innovative cable trays to durable fiberglass solutions and sturdy grille systems. As an authoritative voice in the industry, my goal is to provide valuable information to professionals and businesses and promote forward-looking solutions.