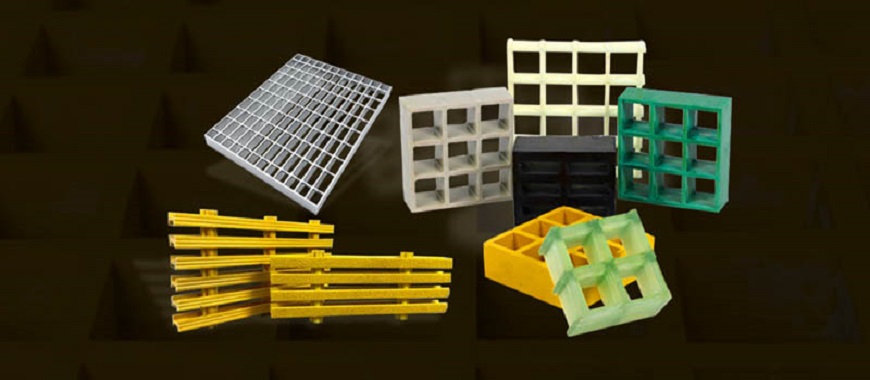
FRP grating material, or Fiber-Reinforced Plastic grating, is a composite material composed of a polymer matrix reinforced with fiberglass. This unique composition results in a lightweight yet robust product that is highly resistant to corrosion and chemicals. FRP grating is widely utilized in various applications, including industrial settings, commercial facilities, and even residential projects. Its ability to withstand harsh environments makes it ideal for use in areas prone to moisture and chemical exposure. When paired with grating pedestals, FRP grating offers additional stability and ease of installation. Compared to traditional materials like steel and wood, FRP grating material offers several advantages, such as lower maintenance requirements, increased durability, and superior slip resistance. These qualities make it a preferred choice for walkways, platforms, and other structural applications where safety and longevity are paramount. FRP grating material is a lightweight, strong, and corrosion-resistant alternative to steel, offering high strength and safety in industrial applications.
Types of FRP Grating Material
When considering FRP grating material, two primary types stand out: molded FRP grating and pultruded FRP grating. Each type has distinct characteristics that make it suitable for various applications.
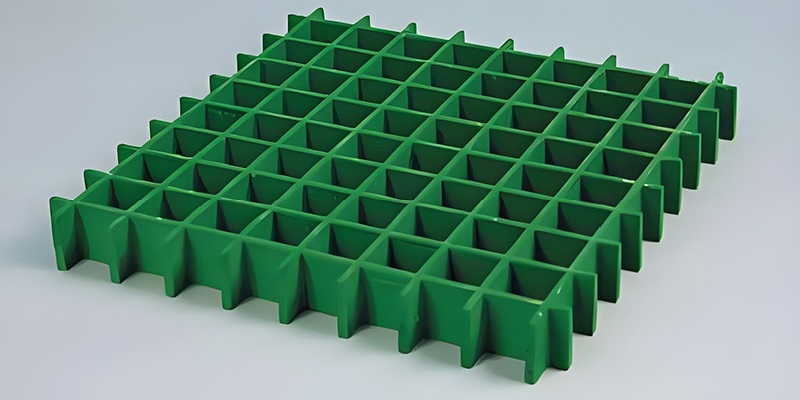
Molded FRP Grating
Molded FRP grating is produced by layering continuous strands of glass fiber and resin in a mold. This process creates a structured product with bidirectional strength. The grating is formed in sheets, which can be easily cut to fit specific applications.
Applications and Benefits:
Molded FRP grating is widely used in environments where slip resistance and corrosion resistance are critical. Common applications include:
- Walkways in chemical plants
- Platforms in wastewater treatment facilities
- Stair treads and safety barriers
Advantages:
- High impact tolerance
- Chemical resistance, making it suitable for harsh environments
- Slip-resistant surfaces that enhance safety
Pultruded FRP Grating
Characteristics and Advantages:
Pultruded FRP grating is manufactured by pulling continuous glass strands through a resin bath and then through a heated die. This method results in a product with a higher glass-to-resin ratio, offering superior strength and rigidity.
Common Uses in Heavy-Duty Applications:
Pultruded FRP grating is ideal for heavy-duty applications due to its strength. It is commonly found in:
- Industrial flooring
- Bridge decking
- Heavy machinery platforms
Advantages:
- Smooth, corrosion-resistant surface
- Higher load-bearing capacity compared to molded grating
- Versatility in design, allowing for custom shapes and sizes
Understanding the different types of FRP grating material helps in selecting the appropriate product for specific applications, ensuring optimal performance and safety.
Construction FRP Solutions for Advanced Infrastructure Projects
FRP Grating Material Suppliers
Finding reliable FRP grating material suppliers or an FRP grating manufacturer is crucial for ensuring the quality and availability of your materials. Here are some key steps and considerations for locating the right suppliers.
How to Find FRP Grating Material Suppliers Near You
- Online Research: Start by conducting online searches for FRP grating material suppliers in your area. Use specific keywords like “FRP grating material suppliers near me” to narrow down your options.
- Industry Directories: Utilize industry-specific directories and resources that list manufacturers and distributors of FRP products. Websites like ThomasNet and Manufacturer’s Directory can be helpful.
- Local Building Supply Stores: Visit or contact local building supply stores, as many may carry or can order FRP grating materials.
Key Factors to Consider When Choosing a Supplier
When selecting a supplier for FRP grating material, consider the following factors to ensure you make the best choice:
- Reliability: Look for suppliers with a solid reputation in the industry. Check reviews and testimonials from previous customers.
- Product Range: Ensure the supplier offers a wide range of FRP grating materials, including various types, sizes, and finishes, to meet your specific project needs.
- Customer Service: Good customer service is essential. A responsive supplier can assist you with any questions and provide support throughout your purchasing process.
- Pricing: Compare prices among different suppliers to find a balance between quality and cost. Keep an eye out for bulk purchase discounts.
- Delivery Options: Evaluate the supplier’s delivery options, including shipping times and costs, to ensure they can meet your project deadlines.
List of Reputable Suppliers for FRP Grating Material
- GangLong Fiberglass: With over 24 years of expertise, GangLong Fiberglass is a leading provider of high-quality fiberglass materials and custom manufacturing solutions. Founded in 2000 and based in Hebei Province, China, we offer an extensive range of products including fiberglass fabrics, fiberglass tubes, fiberglass profiles, fiberglass sheets, and custom fiberglass hand lay-up solutions. Our innovative designs and superior craftsmanship extend to cable trays and grating products, we offer a variety of styles, materials, and finishes ensuring optimal performance and durability.
By considering these factors and exploring reputable suppliers, you can find the right FRP grating material to meet your project’s requirements effectively.
FRP Grating Material and 4’x8′ Fiberglass Grating
4’x8′ fiberglass grating is a popular size in the realm of FRP grating material, widely used across various industries due to its versatility and practicality. This standard size provides an effective solution for numerous applications, offering a balance of strength and ease of handling.
Overview of Standard Sizes
The 4’x8′ fiberglass grating panels are typically manufactured to meet the needs of various construction and industrial projects. This size allows for significant coverage while minimizing the number of seams, which can enhance structural integrity and reduce installation time.
Applications of 4’x8′ Fiberglass Grating
The applications of 4’x8′ fiberglass grating are extensive, making it a preferred choice in many environments. Common uses include:
- Walkways: Ideal for creating safe pathways in industrial settings.
- Platforms: Supports machinery and equipment, providing a durable surface.
- Drain Covers: Used in areas where drainage is essential to prevent flooding.
- Ramps: Facilitates easy access in facilities with mobility considerations.
Advantages of 4’x8′ Fiberglass Grating
The benefits of using 4’x8′ fiberglass grating include:
- Corrosion Resistance: Unlike metal grating, fiberglass does not rust, making it suitable for wet or corrosive environments.
- Lightweight: Easy to transport and install, reducing labor costs and time.
- Slip Resistance: Can be manufactured with slip-resistant surfaces, enhancing safety in high-traffic areas.
- Durability: Withstands heavy loads and extreme weather conditions, ensuring a long service life.
Comparison with Other Standard Sizes Available in the Market
Size | Applications | Advantages |
---|---|---|
4'x4' | Smaller walkways, ramps | Lightweight, easier to handle |
4'x8' | Platforms, drain covers, walkways | Best balance of size and strength |
2'x4' | Tight spaces, smaller projects | Highly portable, fits limited areas |
2'x2' | Custom applications, repairs | Ideal for small repairs, easy to transport |
The 4’x8′ fiberglass grating is a versatile choice in FRP grating material, offering various applications, significant advantages, and an effective solution for many projects. Its durability and resistance to environmental factors make it a reliable choice for both industrial and commercial use.
Pricing of FRP Grating Material
The pricing of FRP grating material is influenced by various factors that play a significant role in determining the overall cost. Understanding these factors can help in making informed purchasing decisions.
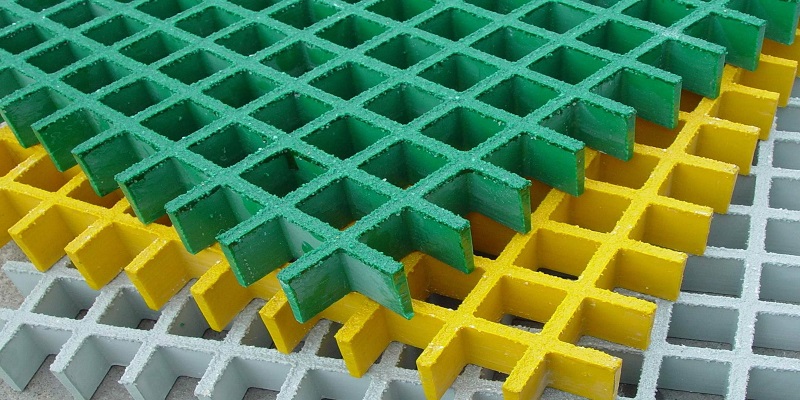
Factors Influencing FRP Grating Price
- Material Quality: The type and quality of resin and fiberglass used significantly affect the price. Higher-quality materials tend to cost more but offer improved durability and performance.
- Manufacturing Process: Different manufacturing methods, such as molded or pultruded grating, come with varying production costs. Pultruded grating, known for its higher strength and load-bearing capabilities, typically commands a higher price.
- Supplier: Pricing can also vary among suppliers based on their location, market reach, and reputation. Suppliers that offer additional services, such as custom fabrication or specialized coatings, may charge higher prices.
- Customization: Custom sizes, colors, and specific features (like slip resistance) can increase the cost of the FRP grating material.
Average Price Ranges for Different Types of FRP Grating Material
- Molded FRP Grating: Typically ranges from $2.50 to $6.00 per square foot, depending on thickness and surface treatment.
- Pultruded FRP Grating: Generally costs between $5.00 and $10.00 per square foot, reflecting its enhanced strength and durability.
Comparison of FRP Grating Prices with Other Materials
Material Type | Average Price Range (per square foot) | Key Features |
---|---|---|
FRP Grating | $2.50 - $10.00 | Lightweight, corrosion-resistant |
Steel Grating | $4.00 - $8.00 | Strong, heavy, susceptible to rust |
Aluminum Grating | $6.00 - $12.00 | Lightweight, corrosion-resistant, but costlier than FRP |
While FRP grating material may have a higher initial cost compared to some traditional materials, its long-term durability, low maintenance needs, and resistance to corrosion can result in lower lifetime costs. This makes it an attractive option for many applications, particularly in environments exposed to moisture and chemicals.
Where to Buy FRP Grating Material
Finding the right source for FRP grating material is crucial for ensuring quality and availability. Here are some options to consider when looking to purchase FRP grating:
GangLong Fiberglass:
With over 24 years of expertise, GangLong Fiberglass is a leading provider of high-quality fiberglass materials and custom manufacturing solutions. Founded in 2000 and based in Hebei Province, China, we offer an extensive range of products including fiberglass fabrics, fiberglass tubes, fiberglass profiles, fiberglass sheets, and custom fiberglass hand lay-up solutions. Our innovative designs and superior craftsmanship extend to cable trays and grating products, we offer a variety of styles, materials, and finishes ensuring optimal performance and durability.
Tips for Purchasing the Right Type of FRP Grating Material
- Assess Your Needs: Before purchasing, evaluate the specific application for which you need the FRP grating. Consider factors such as load capacity, environmental exposure, and required dimensions.
- Check for Certifications: Look for FRP grating materials that meet industry standards and certifications to ensure quality and safety.
- Compare Prices: Shop around to compare prices and features across different suppliers to find the best value for your specific needs.
- Consult with Experts: If you’re unsure about which type of FRP grating material to choose, consider consulting with industry professionals or suppliers who can provide recommendations based on your project requirements.
By exploring various purchasing options and following these tips, you can find the ideal FRP grating material to suit your needs effectively.
Key Types of Grating for Industrial Usage
FRP Grating Material and Other Grating Materials: A Comprehensive Comparison
Grating materials are critical in various industrial, commercial, and environmental applications, where factors like strength, durability, corrosion resistance, and safety play a significant role. In this context, FRP grating material has become increasingly popular due to its unique properties, such as its lightweight structure, corrosion resistance, and high strength-to-weight ratio. However, other materials, such as steel, aluminum, and galvanized steel, are also commonly used for grating, each offering its own set of advantages. This detailed comparison will explore FRP grating material alongside other common grating materials, highlighting their characteristics, uses, and differences to help determine which material is most suitable for specific applications.
Steel Grating Material: Durability and Strength
Steel grating is one of the most widely used materials in industrial settings, known for its high strength and load-bearing capacity. Steel grating is often chosen for environments that require heavy-duty support, such as in manufacturing plants, construction sites, and power stations. Steel grating is usually made from carbon steel or stainless steel, which provides resistance to wear and tear, making it suitable for areas exposed to heavy foot traffic or machinery.
Steel grating, however, has some limitations. One major disadvantage is its susceptibility to rust and corrosion when exposed to moisture or chemicals. To combat this, steel grating can be treated with coatings such as powder coating, galvanization, or anodization to enhance its corrosion resistance. Despite these treatments, steel grating generally requires more maintenance over time compared to FRP grating material.
Advantages of Steel Grating:
- High strength and load-bearing capacity
- Durable and long-lasting with proper maintenance
- Available in various designs for different industrial needs
Disadvantages:
- Prone to rust and corrosion
- Heavier than FRP, making installation more costly
- Requires regular maintenance to prevent degradation
Aluminum Grating Material: Lightweight with Good Corrosion Resistance
Aluminum grating is another popular choice, especially for applications where weight is a concern. Aluminum is lightweight, which simplifies installation and reduces transportation costs. Additionally, aluminum grating offers good corrosion resistance, especially in environments where moisture or corrosive chemicals are present, such as in the marine industry.
However, aluminum is generally not as strong as steel, and its load-bearing capacity may not be sufficient for heavy-duty applications without added reinforcement. Despite this, aluminum grating is often used for pedestrian walkways, ramps, and platforms where strength is necessary, but weight is a critical factor.
Advantages of Aluminum Grating:
- Lightweight, reducing installation costs
- Corrosion-resistant, making it ideal for wet or marine environments
- Non-conductive, enhancing safety in electrical environments
Disadvantages:
- Not as strong as steel, requiring extra reinforcement for heavy loads
- More expensive than steel, especially for large-scale installations
Galvanized Steel Grating Material: Enhanced Corrosion Resistance
Galvanized steel grating is steel that has been coated with a layer of zinc to improve its corrosion resistance. This treatment makes galvanized steel grating a more cost-effective option compared to stainless steel, while still offering enhanced durability against rust and weathering. Galvanized steel grating is used in a variety of applications, including industrial flooring, drainage covers, and walkways.
The main benefit of galvanized steel over regular carbon steel is its increased lifespan due to the protective zinc coating. However, it still shares some of the same drawbacks as steel, such as its susceptibility to impact damage and the potential for coating wear over time.
Advantages of Galvanized Steel Grating:
- Improved corrosion resistance compared to plain steel
- Strong and durable, with good load-bearing capabilities
- More cost-effective than stainless steel
Disadvantages:
- Heavier than FRP, increasing installation complexity
- Zinc coating may wear down over time, leading to corrosion issues
Stainless Steel Grating Material: High Performance and Longevity
Stainless steel grating is highly regarded for its excellent corrosion resistance, strength, and longevity, making it ideal for harsh environments, including chemical processing plants, offshore platforms, and food processing industries. Stainless steel is inherently resistant to corrosion and rust, ensuring a longer service life compared to carbon or galvanized steel.
However, stainless steel grating is heavier and more expensive than other materials like FRP or aluminum, making it less cost-effective for applications where weight is a concern. Despite its high cost, stainless steel grating is considered a premium choice for situations where corrosion resistance and durability are the top priorities.
Advantages of Stainless Steel Grating:
- Superior corrosion resistance
- High strength and load-bearing capacity
- Durable and long-lasting in harsh environments
Disadvantages:
- High cost, especially for large projects
- Heavy, making installation more expensive and complex
FRP Grating Material: The Lightweight, Corrosion-Resistant Solution
FRP grating material stands out as a versatile and cost-effective solution in industrial settings, offering a combination of strength, lightweight properties, and corrosion resistance. Made from glass fibers embedded in a resin matrix, FRP grating is designed to be highly durable, non-conductive, and resistant to chemicals, moisture, and extreme weather conditions. This makes it particularly suitable for environments such as chemical plants, wastewater treatment facilities, and offshore platforms.
The key advantage of FRP grating material is its strength-to-weight ratio. Despite being lighter than steel, it can bear significant loads, reducing transportation and installation costs. Additionally, FRP grating is safer than metal alternatives due to its non-slip surface, which is especially beneficial in wet or hazardous environments. Its resistance to rust, corrosion, and impact makes it a low-maintenance option compared to metal gratings.
Advantages of FRP Grating Material:
- Lightweight and easy to install
- Superior corrosion resistance compared to steel and aluminum
- Non-conductive, offering electrical safety
- Low maintenance, reducing long-term costs
- Impact-resistant, enhancing safety
Disadvantages:
- Limited load-bearing capacity compared to steel or stainless steel in heavy-duty applications
- May require custom configurations for specific industrial needs
When choosing between FRP grating material and other materials like steel, aluminum, galvanized steel, or stainless steel, it’s crucial to consider factors such as strength, weight, corrosion resistance, cost, and maintenance. While FRP grating offers distinct advantages in terms of its lightweight, corrosion resistance, and safety features, materials like steel and stainless steel remain preferable in applications requiring extremely high load-bearing capacities.
In environments prone to corrosion or requiring electrical safety, FRP grating material is often the better choice. On the other hand, for heavy-duty industrial uses that demand maximum strength and durability, steel or stainless steel grating may be more appropriate. Ultimately, the best material depends on specific project requirements, balancing cost with performance and safety considerations.
Applications and Uses of FRP Grating Material Across Various Industries
FRP (Fiberglass Reinforced Plastic) grating material is a versatile and durable material used across numerous industries for its lightweight, corrosion resistance, and high strength. This material is widely adopted in environments where traditional materials like steel or wood may not perform well due to exposure to harsh chemicals, moisture, or heavy loads. In this article, we will explore the key areas of application for FRP grating material, categorized under specific subheadings to provide a detailed and structured understanding.
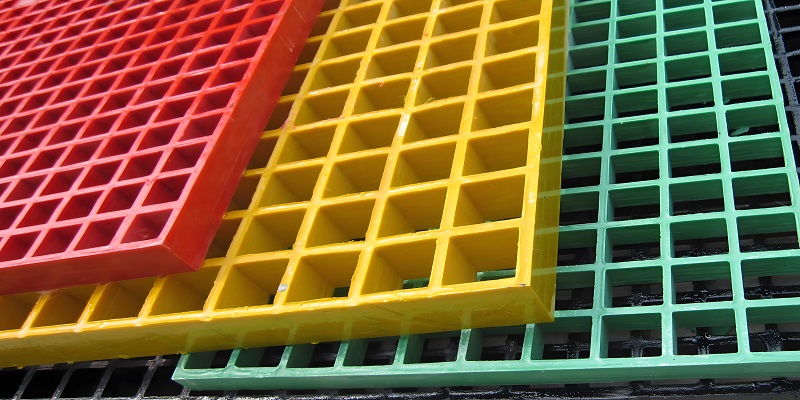
Industrial and Chemical Processing Facilities
FRP grating material is extensively used in industrial and chemical processing facilities due to its exceptional resistance to corrosion and harsh chemicals.
In such environments, traditional materials often degrade quickly due to the presence of acidic or alkaline substances, leading to costly replacements. FRP grating material offers a cost-effective, long-lasting solution for:
- Walkways and platforms in chemical plants
- Tank covers and drainage systems exposed to corrosive fluids
- Protective structures in oil refineries
The non-slip properties of FRP grating also improve safety for workers in these hazardous conditions.
Marine and Offshore Applications
Given its excellent resistance to saltwater corrosion and its lightweight nature, FRP grating material is a natural choice for marine and offshore industries.
The harsh environment of marine settings requires materials that can withstand constant exposure to moisture and saline conditions. FRP grating is commonly used for:
- Boat decks and docks
- Offshore oil rigs and platforms
- Seawater desalination plants
Additionally, its non-conductive nature ensures safety in applications where electrical systems are involved.
Wastewater Treatment Plants
FRP grating material is a staple in wastewater treatment plants, where exposure to moisture, chemicals, and biological agents is constant.
In such facilities, corrosion resistance and low maintenance are essential, making FRP grating ideal for:
- Walkways over water treatment tanks
- Covers for channels and pits
- Safety platforms in wet or corrosive environments
Its lightweight properties also simplify installation in large-scale facilities.
Public Infrastructure and Utilities
In public infrastructure projects, FRP grating material is valued for its longevity and minimal maintenance requirements.
Applications include:
- Drain covers and trench grating in urban areas
- Pedestrian walkways and bridges
- Protective enclosures for utility equipment
FRP’s ability to withstand weather extremes makes it a reliable choice for outdoor use.
Transportation Industry
FRP grating material is also finding increased use in the transportation sector, where its lightweight and durable nature contribute to efficiency.
Key uses include:
- Flooring for rail cars and buses
- Platforms and stairways in maintenance facilities
- Safety barriers and ventilation grates
Its fire-resistant variants provide additional safety in confined spaces.
Food and Beverage Industry
Hygiene and resistance to contamination are critical in food processing and beverage production facilities, making FRP grating a preferred choice.
The smooth, non-porous surface of FRP grating material resists bacterial growth and is easy to clean. Common uses include:
- Flooring in production areas
- Drain covers in food plants
- Anti-slip walkways in wet or slippery environments
Recreational and Entertainment Areas
In recreational spaces, FRP grating material is appreciated for its aesthetic options, including customizable colors and textures.
This material is often used for:
- Swimming pool decks and diving boards
- Boardwalks in parks and beachfronts
- Access ramps and bridges
The anti-slip features make it safe for areas prone to water accumulation.
FRP grating material is a highly adaptable and reliable solution for environments requiring durability, corrosion resistance, and safety. From industrial plants and marine environments to public infrastructure and recreational facilities, its versatility makes it a favored choice across various sectors. As industries continue to prioritize sustainability, safety, and cost efficiency, the demand for FRP grating material is expected to grow, further solidifying its place as a critical material in modern applications.
Manufacturing Standards for FRP Grating Material: Ensuring Quality and Safety
FRP grating material is widely used in various industrial, commercial, and environmental applications due to its unique properties, such as corrosion resistance, strength, and lightweight design. However, to ensure its effectiveness and reliability, FRP grating must adhere to several manufacturing standards. These standards cover everything from the raw materials used to the final product’s performance characteristics, ensuring that the grating meets required safety, strength, and durability specifications. This section will explore the key standards that should be followed during the manufacturing process of FRP grating material, including international guidelines, material specifications, testing procedures, and safety considerations.
Raw Material Standards: Quality Glass Fibers and Resins
The raw materials used in the production of FRP grating are critical to its performance. The glass fibers and resin must meet specific standards to ensure the final product’s strength, corrosion resistance, and durability. The type and quality of resin, such as polyester, vinyl ester, or epoxy, determine the grating’s resistance to chemicals, temperature fluctuations, and moisture. Likewise, the glass fibers used must be of high quality, ensuring uniform distribution throughout the resin matrix.
Resin Standards: The resin used in FRP grating must comply with standards such as ASTM D1983 (Standard Specification for Polyester Resin) or ASTM D3846 (Standard Test Method for Tensile Strength of Reinforced Plastics). These standards ensure that the resin provides sufficient bonding strength and chemical resistance for the intended application.
Glass Fiber Standards: Glass fibers used in FRP grating should comply with standards like ASTM D578 (Standard Specification for Glass Fiber), which ensures consistent quality and performance. The fibers should be resistant to chemical attack, heat, and moisture to ensure long-term durability.
Manufacturing Process Standards: Pultrusion and Molding Techniques
The manufacturing process for FRP grating material typically involves two primary techniques: pultrusion and molding. Each of these methods has specific standards to ensure that the grating meets performance and safety requirements.
Pultrusion Standards: Pultrusion involves pulling fibers through a resin bath and then curing them into a solid profile. This process is designed to produce high-strength, consistent, and durable grating. The relevant standard for pultrusion is ASTM D638 (Standard Test Method for Tensile Properties of Plastics), which provides guidelines for testing the strength of the materials produced by this process. This standard ensures that the final grating product can withstand the intended load-bearing capacity and resist wear and tear.
Molding Standards: Molding involves casting the grating shapes into molds, typically using a resin matrix and glass fibers. The standards for this method are often outlined in ASTM D5948 (Standard Specification for Glass-Fiber-Reinforced Polyester Structural Shapes). This standard governs the minimum requirements for dimensional accuracy, strength, and impact resistance of molded FRP products. It ensures that molded grating products are structurally sound and consistent.
Strength and Load-Bearing Capacity Standards: Ensuring Durability
One of the most important considerations in the manufacturing of FRP grating material is ensuring it can support the loads it is designed for, without bending or failing. To achieve this, manufacturers must comply with specific strength and load-bearing standards.
Load-Bearing Standards: FRP grating materials should meet the requirements of standards like ASTM C578 (Standard Specification for Rigid, Cellular Polystyrene Thermal Insulation) or ASTM F3050 (Standard Guide for Load-Bearing Capacity of FRP Grating Systems). These standards outline the methodology for calculating the load capacity based on the type of resin, fiber orientation, and thickness of the grating. They ensure that the material is tested under appropriate conditions to guarantee performance in the intended application, whether it’s for pedestrian walkways, industrial platforms, or heavy machinery areas.
Strength Testing: FRP grating must undergo rigorous strength testing as per ASTM D198 (Standard Test Methods for Tensile Properties of Plastics), ensuring the grating can withstand stress without cracking or deforming. It is vital that the FRP grating material meets both minimum tensile strength and flexural strength standards to handle the stresses it will be subjected to during use.
Corrosion Resistance Standards: Protecting Against Harsh Environments
One of the primary advantages of FRP grating is its resistance to corrosion, making it ideal for use in chemically aggressive environments, marine applications, and areas with high humidity. The manufacturing process must ensure that FRP grating meets stringent corrosion resistance standards.
Corrosion Resistance Testing: FRP grating material should comply with ASTM D570 (Standard Test Method for Water Absorption of Plastics), which evaluates the material’s resistance to water absorption and its ability to withstand corrosion in wet conditions. Additionally, ASTM D543 (Standard Practices for Determining the Resistance of Plastics to Chemical Reagents) should be followed to assess the material’s resistance to a wide range of chemicals, ensuring that the grating can perform in environments like chemical plants or wastewater treatment facilities.
Salt Spray Testing: For marine environments, FRP grating must pass salt spray tests to assess its resistance to the corrosive effects of saltwater. The relevant standard for this testing is ASTM B117 (Standard Practice for Operating Salt Spray (Fog) Apparatus), which ensures that the grating can withstand the harsh conditions of coastal or offshore applications.
Safety Standards: Ensuring Worker Protection
In industrial applications, FRP grating must meet safety standards to ensure the protection of workers and the integrity of the structure. The slip resistance of FRP grating is particularly crucial in environments where wet or hazardous conditions are common.
Slip Resistance Standards: FRP grating must meet ASTM E303 (Standard Test Method for Measuring Surface Frictional Properties Using a Portable Skid Resistance Tester), which tests the slip resistance of flooring materials to prevent accidents in environments where water or oils may be present. FRP grating can be designed with a textured surface to enhance safety, especially in wet or slippery environments.
Fire Resistance Standards: FRP grating material should also meet fire resistance standards, such as ASTM E84 (Standard Test Method for Surface Burning Characteristics of Building Materials). These standards ensure that the material does not contribute to the spread of fire in critical environments like chemical plants, refineries, or offshore platforms.
The manufacturing process for FRP grating material requires strict adherence to various international standards to ensure that the product meets the necessary performance, safety, and durability requirements. By complying with established standards for raw materials, manufacturing processes, strength, corrosion resistance, and safety, FRP grating can provide reliable, long-lasting solutions in a wide range of industrial applications. Adhering to these standards guarantees that FRP grating material performs efficiently and safely under the harshest conditions, making it a preferred choice for numerous industries worldwide.
Cost and Maintenance Considerations of FRP Grating Material
FRP (Fiberglass Reinforced Plastic) grating material is renowned for its durability and low maintenance, but understanding its cost structure and long-term maintenance benefits is essential for evaluating its overall value. While the initial investment in FRP grating may be higher than traditional materials like steel or wood, its longevity and reduced upkeep expenses often make it a more economical choice in the long run. This article will analyze the cost and maintenance aspects of FRP grating material through multiple perspectives, offering a comprehensive understanding of its financial and operational advantages.
Initial Cost of FRP Grating Material
The upfront cost of FRP grating material is higher compared to conventional materials, but this investment reflects the advanced manufacturing process and superior material properties.
Specific cost factors include:
- Raw Materials: The use of high-quality fiberglass and resin increases durability but adds to the cost.
- Customization Options: FRP grating can be tailored in terms of size, color, and texture, which can influence pricing.
- Installation Costs: Although FRP is lightweight and easier to install, requiring less labor compared to heavier materials like steel, specialized cutting or customization may increase initial expenses.
While the initial cost is higher, it is important to view this as a long-term investment due to its durability and lower maintenance requirements.
Long-Term Cost Benefits
Though the upfront cost of FRP grating material may be significant, its long-term cost advantages outweigh the initial expense.
Key benefits include:
- Corrosion Resistance: FRP grating does not rust or degrade, reducing the need for frequent replacements or repairs.
- Longevity: With a lifespan significantly longer than materials like steel or wood, FRP grating minimizes capital expenditure over time.
- Energy Efficiency in Maintenance: Lightweight properties reduce transportation costs and simplify handling during installations or upgrades.
For industries where environmental exposure is severe, such as marine or chemical facilities, the reduced risk of degradation further enhances the material’s cost-efficiency.
Maintenance Requirements
FRP grating material is celebrated for its low maintenance demands, making it a practical and cost-effective choice for various applications.
Its maintenance advantages include:
- Non-Corrosive Properties: FRP grating does not require anti-corrosion coatings or treatments, unlike steel.
- Easy Cleaning: The smooth, non-porous surface resists dirt and bacterial growth, making it easy to clean with basic detergents or water.
- Damage Resistance: It withstands impact and heavy loads, minimizing the need for repairs or replacements due to wear and tear.
- UV Stability: Many FRP gratings are UV-resistant, preventing discoloration or surface deterioration in outdoor environments.
These low maintenance requirements translate into significant cost savings for industries that rely on continuous operation.
Comparative Analysis with Traditional Materials
To fully understand the cost-effectiveness of FRP grating material, it is essential to compare it with traditional materials like steel, aluminum, or wood.
- Steel: Steel grating is less expensive initially but requires regular maintenance to prevent rust and corrosion, particularly in humid or chemical environments.
- Aluminum: While lightweight and corrosion-resistant, aluminum lacks the strength and durability of FRP, leading to higher replacement rates in heavy-duty applications.
- Wood: Wood is cheaper but prone to rot, warping, and pests, resulting in frequent repairs and shorter lifespans compared to FRP.
In all these cases, FRP grating offers a longer-lasting, low-maintenance alternative, making it a better long-term investment despite its higher initial cost.
Environmental and Lifecycle Benefits
FRP grating material also delivers cost savings by contributing to sustainable practices and reducing waste.
Specific environmental benefits include:
- Reduced Waste: Its durability reduces the frequency of replacement, minimizing material waste.
- Energy Savings: Lightweight FRP grating requires less energy for transportation and installation.
- Recyclability: Some types of FRP materials are recyclable, aligning with eco-friendly practices and reducing disposal costs.
These lifecycle benefits make FRP grating material an attractive option for industries prioritizing environmental responsibility alongside cost efficiency.
FRP grating material, while initially more expensive than traditional alternatives, offers unparalleled long-term cost advantages and minimal maintenance requirements. Its resistance to corrosion, easy cleaning, and extended lifespan ensure reduced operational costs and lower replacement rates over time. Moreover, the environmental benefits and sustainability factors further enhance its overall value. For industries seeking a reliable, durable, and low-maintenance solution, FRP grating material remains a superior choice, combining both economic and operational efficiency.
FAQs about FRP Grating Material
FRP grating, or Fiberglass Reinforced Plastic grating, is primarily made from a combination of fiberglass and a polymer resin. The fiberglass provides strength and structural integrity, while the resin acts as a matrix that binds the fibers together and offers corrosion resistance. This combination results in a durable, lightweight material that can withstand harsh environmental conditions. Common types of resins used in FRP grating include polyester, vinylester, and epoxy, each offering specific benefits such as enhanced chemical resistance and improved strength.
FRP, or Fiberglass Reinforced Plastic, is a composite material made from a polymer matrix reinforced with glass fibers. The glass fibers are responsible for providing the material’s tensile strength and rigidity, while the resin matrix helps protect the fibers from environmental factors. This combination yields a versatile material that is lightweight, strong, and resistant to corrosion, making it suitable for various applications across multiple industries, including construction, marine, and transportation.
The lifespan of FRP grating can vary depending on several factors, including the type of resin used, environmental conditions, and the level of maintenance. Generally, FRP grating has an impressive lifespan ranging from 20 to 30 years or more when properly maintained. Its resistance to corrosion and UV degradation contributes to its durability, particularly in harsh environments such as chemical plants or coastal areas. Regular inspections and cleaning can further extend the lifespan of FRP grating.
FRP (Fiberglass Reinforced Plastic) and GRP (Glass Reinforced Plastic) are terms that are often used interchangeably; however, there are some distinctions. FRP typically refers to composite materials that can utilize various types of reinforcing fibers, including carbon or aramid fibers, in addition to glass. GRP specifically refers to composites that exclusively use glass fibers for reinforcement. Both materials exhibit similar properties, such as corrosion resistance and high strength-to-weight ratios, but the specific applications may differ based on the reinforcing materials used. Understanding these differences can help in selecting the right grating type for specific project requirements.
Fiberglass (FRP) grating is generally cheaper than steel grating in terms of initial cost, particularly when factoring in long-term benefits like reduced maintenance and corrosion resistance. Steel grating may have a lower upfront price, but it requires more frequent upkeep to prevent rust, which can lead to higher overall costs. Additionally, FRP grating’s lightweight nature reduces labor costs during installation and transportation, making it more cost-effective for many projects. While steel has a higher load-bearing capacity, FRP grating is often favored in applications where corrosion resistance and safety are priorities. The choice between fiberglass and steel grating depends on specific use cases, environmental conditions, and total cost of ownership over time.
FRP grating is known for its impressive strength despite being lightweight. Its strength comes from the glass fibers embedded in a resin matrix, which provides a high strength-to-weight ratio. In fact, FRP grating is typically stronger than many types of steel or aluminum grating in terms of its ability to resist impact and distribute loads. The strength can be tailored by adjusting the fiber orientation during production, making it suitable for a wide range of industrial applications. Although it is strong, the specific strength of FRP grating depends on factors such as the resin used, fiber content, and manufacturing process (molded or pultruded). It is designed to withstand heavy foot traffic, equipment loads, and harsh environments without warping or weakening over time.
The thickness of FRP grating can vary based on the application and specific design requirements. Typically, FRP grating comes in thicknesses ranging from 1/2 inch (12.7 mm) to 2 inches (50.8 mm). The thickness of the grating is influenced by factors such as load-bearing capacity, the type of resin used, and the specific type of FRP grating (molded or pultruded). Thicker grating is often used in industrial settings where higher load capacities or additional strength is required, while thinner grating may be sufficient for less demanding applications. The overall thickness is designed to balance the strength of the material with the desired weight and ease of installation. In custom applications, thickness can be adjusted to meet specific performance needs.
GRP (Glass Reinforced Plastic) grating, or FRP grating, offers several advantages over steel grating in specific applications. While steel grating provides excellent strength, GRP grating is superior in terms of corrosion resistance, lightweight, and safety. Unlike steel, which can rust and corrode in harsh environments, GRP grating remains unaffected by chemicals, saltwater, and extreme weather conditions, making it ideal for use in chemical plants, marine environments, and outdoor applications. Additionally, GRP grating is non-conductive, reducing electrical hazards in sensitive areas. Steel grating, however, may still outperform GRP grating in applications requiring extremely high load-bearing capacity. Ultimately, the choice depends on the environment and load requirements; for corrosive or electrical safety needs, GRP grating is a better option, while steel grating might be preferred for heavy-duty industrial applications.
The primary advantages of FRP grating include its high strength-to-weight ratio, excellent corrosion resistance, flame retardancy, and non-conductivity. These qualities make it an ideal choice for use in industries like chemical processing, wastewater treatment, and marine applications where durability and safety are critical. FRP grating is lighter than steel or aluminum, which reduces installation and transportation costs, and its non-corrosive nature ensures longevity, reducing maintenance and replacement costs over time. Additionally, FRP grating is more impact-resistant than metal alternatives, improving safety in environments where foot traffic or equipment movement occurs frequently. Its ability to resist extreme temperatures and various chemicals further enhances its versatility in diverse industrial settings. Overall, the advantages of FRP grating make it a cost-effective, durable, and safe choice for a wide range of applications.
The load-bearing capacity of FRP grating varies depending on factors such as the thickness of the grating, the type of resin used, and the configuration of the fibers. Typically, FRP grating can bear loads ranging from 500 to 2,000 pounds per square foot (psf). This makes it suitable for a variety of applications, from light pedestrian traffic to heavy industrial equipment. In applications where high load capacity is essential, FRP grating can be custom-engineered to provide greater strength. The pultruded manufacturing process, which aligns fibers in a specific direction, results in higher strength and load-bearing capacity compared to molded grating. As a general guideline, FRP grating can withstand significant forces while remaining light, durable, and resistant to corrosion. Its precise load-bearing capability should always be confirmed based on the grating’s specifications for the intended use.
FRP grating is used in a wide variety of industrial, commercial, and environmental applications due to its corrosion resistance, strength, and durability. Common uses include chemical plants, oil rigs, water treatment facilities, and marine environments, where the grating’s resistance to chemicals, saltwater, and moisture makes it highly valuable. It is also used in pedestrian walkways, platforms, stairways, and mezzanines in areas that require non-slip surfaces. The lightweight and non-conductive properties make it ideal for electrical installations, such as substations or areas with hazardous materials. FRP grating is also commonly found in food processing, pulp and paper mills, and any industry with strict safety standards, as it reduces the risk of slipping and injury. Its versatility allows it to be adapted to a variety of environments, improving safety and efficiency across a wide range of sectors.
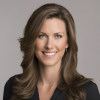
As the editor of GangLong Fiberglass, I have years of experience and in-depth research, focusing on cable tray products, fiberglass solutions, and grille systems. I incorporate years of industry insights and practical experience into every content, committed to promoting the progress of the industry. At GangLong Fiberglass, my commitment is reflected in every product, from innovative cable trays to durable fiberglass solutions and sturdy grille systems. As an authoritative voice in the industry, my goal is to provide valuable information to professionals and businesses and promote forward-looking solutions.