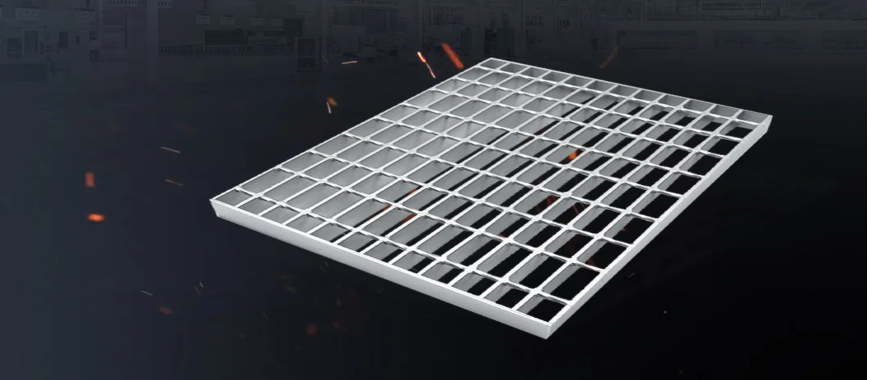
In the realm of industrial and commercial settings, the importance and utility of walkway grating cannot be overstated. These surfaces play a critical role in ensuring the safety and ease of movement for both personnel and machinery across various environments. Among the different materials used for manufacturing walkway grating, galvanised steel walkway grating stands out for its exceptional durability, resistance to corrosion, and overall performance under demanding conditions. This type of grating is specifically designed to withstand heavy traffic and harsh environmental conditions, making it an ideal choice for industries such as manufacturing, energy, and transportation. Its unique properties not only ensure a secure footing but also contribute to the efficiency and operational smoothness within these sectors. The implementation of galvanised steel walkway grating is a testament to the innovative solutions aimed at enhancing workplace safety and productivity. Galvanised steel walkway grating is durable, corrosion-resistant, and easy to install, ideal for walkways, ventilation, gutter covers, and more.
Why Choose Galvanised Steel Walkway Grating?
Choosing the right material for walkway grating in industrial and commercial settings is crucial due to its direct impact on safety and durability. Galvanised steel walkway grating is a top choice for several compelling reasons, particularly its durability and corrosion resistance. Below, we explore these attributes in detail.
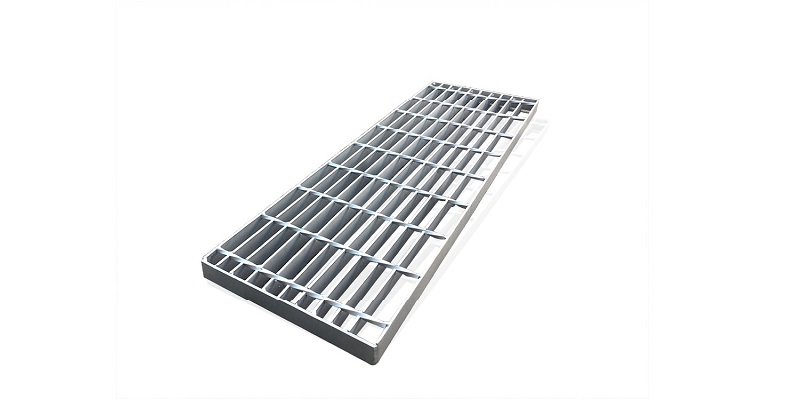
Durability
- Structural Integrity: Galvanised steel walkway grating maintains its structural integrity under heavy loads and repeated use, making it ideal for high-traffic areas.
- Impact Resistance: This grating can withstand significant impact without deformation, ensuring it remains functional after accidental drops or strikes.
- Abrasion Resistance: The tough surface of galvanised steel resists scratches and abrasions, which are common in industrial environments.
- Load Distribution: It effectively distributes weight, preventing stress on any single point of the structure.
- Resistance to Warping: Unlike other materials, galvanised steel does not warp easily, maintaining its shape over time and under varying temperatures.
- Minimal Maintenance: The need for repair or replacement is significantly reduced thanks to the hard-wearing properties of the steel.
- Adaptability: It can be designed to meet specific load-bearing requirements, making it versatile for multiple applications.
- Heat Resistance: Galvanised steel can withstand extreme temperatures, making it suitable for industries dealing with high heat processes.
- Safety: Its robust nature reduces the risk of accidents due to structural failure or surface degradation.
Corrosion Resistance
- Zinc Coating: The layer of zinc provides a protective barrier against environmental factors that cause corrosion.
- Long-Lasting Protection: This protective coating remains effective for many years, significantly extending the grating’s lifespan.
- Self-Healing: Minor scratches or damages to the coating can self-heal, as zinc’s properties encourage a natural recovery process.
- Chemical Resistance: It is resistant to damage from most industrial chemicals, preventing degradation that can occur from spills or exposure.
- Moisture Barrier: Zinc acts as a moisture barrier, reducing the risk of rust, which is critical in outdoor or humid environments.
- Uniform Coverage: During the galvanizing process, the steel is dipped in molten zinc, ensuring even coverage and comprehensive protection.
- Improved Longevity in Coastal Areas: Its ability to resist salt spray makes it excellent for use in marine or coastal settings.
- Industrial Resilience: The galvanized coating withstands industrial pollutants and environmental contaminants that can accelerate corrosion.
- Cost-Effectiveness: Given its longevity and reduced need for maintenance, galvanised steel walkway grating offers a cost-effective solution in the long term.
Extending the Life Span
- Comprehensive Coverage: The galvanizing process ensures that every part of the grating is coated, eliminating weak spots susceptible to rust.
- Enhanced Durability: The increased durability from the zinc coating directly translates to a longer useful life for the galvanized steel walkway grating.
- Reduced Lifecycle Cost: Less frequent replacements and repairs lower the overall lifecycle costs associated with galvanised steel grating.
- Sustainability: Longer-lasting materials mean fewer resources are consumed over time, which is beneficial from a sustainability perspective.
- Less Downtime: Facilities experience less downtime due to maintenance or grating failures, promoting continuous operational efficiency.
- Return on Investment: The initial cost of galvanising is offset by the extended lifespan and reduced maintenance costs.
- Weather Resistance: It performs well under various weather conditions, preventing environmental wear and tear from shortening its life.
- Protection Under Extreme Conditions: The protective qualities of galvanised steel ensure reliability even under extreme industrial conditions.
- Consistent Performance: The longevity of the grating’s structural and protective qualities ensures consistent performance throughout its lifespan.
Galvanised steel walkway grating provides an unmatched blend of durability, corrosion resistance, and life-extending properties, making it a superior choice for demanding environments.
Fiberglass W Beam vs Steel: What You Need to Know
Types of Walkway Grating: Galvanized Steel Grating Walkway and other Types
The steel of galvanized walkway grating is a vital component in various industrial and architectural applications. This type of grating ensures safety, durability, and corrosion resistance, making it ideal for outdoor and harsh environmental conditions. Let’s delve into the types and advantages of galvanized steel walkway grating.
Galvanized Steel Grating Walkway
The use of galvanised steel walkway grating is prevalent due to its exceptional strength and longevity. This grating type undergoes a galvanization process, where a protective zinc coating is applied to prevent rust and corrosion. Its main applications include industrial platforms, stair treads, and drainage covers. The benefits of galvanized steel grating walkways include:
- Durability: Resists harsh weather conditions and industrial chemicals.
- Safety: Provides excellent slip resistance, reducing accidents.
- High Load Capacity: Capable of supporting heavy loads and machinery.
- Easy Maintenance: The galvanized coating makes it easy to clean.
- Cost-Effectiveness: Long lifespan reduces the need for frequent replacements.
- Versatility: Available in various thicknesses and sizes to fit different applications.
- Aesthetic Appeal: Offers a neat, professional look to the premises.
- Fire Resistance: Steel is naturally fire-resistant, enhancing safety.
- Environmentally Friendly: Galvanized steel is recyclable, minimizing environmental impact.
Metal Grate Walkway
Metal grate walkways, including those made from galvanized steel, offer versatility for use in numerous environments. Beyond the industrial sector, these grates find applications in parks, residential areas, and commercial buildings. The versatility aspects of metal grate walkways involve their ability to enhance both functionality and aesthetics. For instance, a steel grating garden walkway combines durability with an appealing design, making it a perfect choice for outdoor spaces while ensuring water drainage and long-lasting performance:
- Variety in Design: Available in different patterns and styles for aesthetic preferences.
- Adaptable to Environments: Suits both urban and rural settings.
- Weather-Resistant: Performs well in all climates, from extreme heat to freezing temperatures.
- Customization: Can be cut and shaped to meet specific project requirements.
- Lightweight Options: Aluminum and other metals provide lighter alternatives where applicable.
- Non-Slip Surfaces: Essential for ensuring safety in wet or oily conditions.
- Load-Bearing Capacities: Suitable for pedestrian traffic and heavy equipment.
- Ease of Installation: Simplified installation processes save time and labor costs.
- Sustainability: Metal grates can be recycled, promoting environmental sustainability.
Plastic and Other Materials
While galvanised steel walkway grating remains a popular choice, alternatives like plastic grating offer solutions for specific, non-heavy-duty applications. Plastic grating is suitable for environments where corrosion resistance at a lower weight is crucial. Key points regarding plastic and other materials include:
- Corrosion Resistance: Ideal for chemical or saltwater exposure.
- Lightweight: Easier to transport and install compared to metal grates.
- Color Options: Available in various colors for aesthetic integration.
- Maintenance-Free: Does not require painting or special treatments.
- Cost-Effective: Generally lower upfront cost than metal options.
- Non-Conductive: Safe for electrical environments.
- UV Resistance: Plastic materials can be UV stabilized for outdoor use.
- Recyclable: Many plastic grates are made from recyclable materials.
- Softness: Gentle on the feet, offering a comfortable walking experience for light traffic areas.
Through the exploration of different materials and types of grates, it’s clear that while galvanized steel is preferred for heavy-duty and industrial applications, other materials like plastic present viable options for less intensive use cases. Each material offers unique benefits tailored to specific environmental and usage requirements, enabling designers and engineers to select the most appropriate solution for their project’s needs.
Types of Galvanised Steel Walkway Grating
Galvanised steel walkway grating comes in various types, each designed for specific applications and environments. These gratings offer excellent strength, durability, and corrosion resistance, making them suitable for industrial, commercial, and architectural use. The different types of grating are distinguished by their manufacturing process, load-bearing capacity, and surface characteristics. Below, we explore the key types of galvanised steel walkway grating, detailing their features and ideal applications.
Welded Steel Grating
Welded steel grating is one of the most commonly used types of galvanised steel walkway grating. It is made by welding bearing bars and cross bars together to form a strong and stable structure.
- High Strength & Load Capacity: The welding process creates a sturdy bond, making this grating ideal for heavy-duty applications such as industrial plants, platforms, and stair treads.
- Corrosion Resistance: The galvanised coating protects against rust and environmental damage, ensuring long-lasting durability.
- Applications: It is widely used in areas with high-impact loads, such as walkways, automobile traffic zones, and warehouses.
Press-Locked Steel Grating
Press-locked steel grating is known for its uniform appearance and flush surface, making it suitable for applications where aesthetics matter. Instead of welding, the grating is manufactured by pressing cross bars into pre-punched holes in the bearing bars.
- Welding-Free Construction: The absence of welding makes it ideal for environments where welding is restricted, such as chemical plants.
- Enhanced Appearance & Versatility: The grating offers a sleek, modern look while maintaining durability. It is often used in architectural designs, public walkways, and platforms.
- Structural Integrity: The press-locking process ensures a consistent and reliable structure that meets both aesthetic and functional needs.
Riveted Steel Grating
Riveted steel grating is a highly durable option designed for environments requiring maximum strength and safety. It is constructed by riveting flat bars and rods into the bearing bars, providing exceptional stability.
- Impact & Load Resistance: The riveted design enhances resistance to heavy loads and shock, making it ideal for bridges and high-traffic areas.
- Historical & Industrial Use: This grating is commonly used in historic renovations and industrial settings where structural reinforcement is needed.
- Corrosion Protection: The galvanised coating ensures long-term durability and protection against environmental factors.
Heavy-Duty Steel Grating
For areas that experience extreme conditions and heavy loads, heavy-duty steel grating is the best choice. It is constructed with thicker and deeper bearing bars to provide superior strength.
- Load-Bearing Excellence: This grating can withstand large vehicles, heavy equipment, and harsh conditions, making it ideal for airports, loading docks, and industrial plants.
- Durability & Corrosion Resistance: The galvanisation process enhances its ability to resist rust, weather exposure, and mechanical wear.
- Industrial Applications: It is widely used in high-load areas where standard grating would not be sufficient.
Bar Grating Stair Treads
Stair treads made from galvanised steel grating offer a safe and slip-resistant surface for stairways. These treads are commonly found in industrial and commercial buildings, ensuring safe foot traffic.
- Safety Features: The open design allows light, air, and debris to pass through, reducing the risk of slipping.
- Versatile Use: Bar grating stair treads are used in factories, warehouses, and outdoor staircases to provide stable footing.
- Long-Lasting Protection: The galvanised finish ensures durability in both indoor and outdoor environments.
Galvanised steel walkway grating comes in different types to meet diverse structural and functional requirements. From welded and press-locked grating to heavy-duty and stair tread options, each type serves a specific purpose. Grating and handrail systems are often paired together, providing not only a safe walking surface but also reliable support along elevated walkways and platforms. Choosing the right grating depends on factors such as load capacity, environmental conditions, and aesthetic considerations. With their durability, corrosion resistance, and strength, these solutions offer long-lasting reliability for industrial applications.
Design and Installation of Galvanised Steel Walkway Grating
When considering the design elements of galvanised steel walkway grating, it’s important to understand the balance between customization options and the industry’s standard dimensions. This ensures that the grating not only meets specific aesthetic and functional requirements but also aligns with manufacturing norms, thereby facilitating easier installation and potentially lower costs due to standardization.
- Bearing Bar Size: The load-bearing bars can vary in thickness and depth, depending on the anticipated load.
- Bar Spacing: The space between bars affects the passage of light and materials through the grate.
- Grate Size: Grating panels come in pre-defined dimensions but can be cut to specific sizes.
- Surface Treatment: The texture of the bars can be specified to enhance grip and safety.
- Finish: Galvanisation is the standard finish, but additional coatings may be applied for extra protection or color.
- Edge Banding: Adding a band to the grate edges can reinforce the structure and prevent warping.
- Load Table Consultation: Referring to industry load tables ensures the correct specifications for intended use.
- Pattern and Shape: Grating patterns, such as elongated holes or decorative shapes, can be customized for unique applications.
- Accessibility Compliance: Design considerations should account for regulatory guidelines like ADA compliance when applicable.
Installation Tips
Proper installation of galvanised steel walkway grating is critical to ensure its longevity and performance. Below are some tips that can assist during the installation process:
- Site Inspection: Prior to installation, thoroughly inspect the site to ensure that the frames and supports are correctly positioned and leveled.
- Correct Tools: Use appropriate tools for securing the grating, like galvanized bolts, to prevent corrosion.
- Clamping: Temporary clamps can hold grating in place and keep it aligned during the installation process.
- Alignment: Make sure all grating panels are square and aligned before final fixation for a uniform surface.
- Clearances: Ensure adequate clearance for expansion and contraction due to temperature changes.
- Welding: When welding is required, protect the zinc coating by welding only at the corners or specially designed contact points.
- Cutting: If on-site customization is needed, cut grating with appropriate power tools and coat the exposed edges to prevent rust.
- Sequencing: Install the grating progressively to maintain accessibility and avoid displacement of installed panels.
- Regular Maintenance: Post-installation check-ups are vital for the long-term safety and durability of the grating.
By adhering to these points, the proper design and installation of galvanised steel walkway grating can be significantly more efficient, reliable, and in line with professional standards, providing a secure and enduring solution for pedestrian access in a variety of settings.
Recommended Installation Methods for Galvanised Steel Walkway Grating
Proper installation of galvanised steel walkway grating is crucial for ensuring safety, stability, and longevity. There are three primary installation methods: welding, bolting, and clamping. Each method offers unique advantages and is suited for different applications based on factors such as permanence, ease of maintenance, and structural requirements. Below, we explore these installation techniques in detail, highlighting their benefits and applications.
Welding Installation Method
Welding is the most permanent and secure installation method for galvanised steel walkway grating. This method is preferred for applications requiring long-term stability and high load-bearing capacity.
- Permanent Connection: Welding fuses the grating directly to the supporting structure, preventing movement or displacement.
- High Strength & Stability: It is ideal for areas with heavy foot traffic, industrial platforms, and high-impact environments.
- Corrosion Resistance: Although welding may remove some of the galvanised coating, additional protective measures like zinc-rich paint can restore corrosion resistance.
- Applications: Common in factories, bridges, and heavy-duty walkways where structural integrity is a priority.
Bolting Installation Method
Bolting allows for secure yet removable installation, making it suitable for areas where maintenance or reconfiguration may be needed.
- Easy Disassembly & Reassembly: Unlike welding, bolted grating can be removed and replaced without damaging the structure.
- Flexibility in Application: It is ideal for walkways, maintenance platforms, and temporary installations.
- Requires Pre-Drilled Holes: Proper alignment of holes in both the grating and support structure is necessary for effective installation.
- Applications: Used in facilities that require periodic access to underlying equipment, such as HVAC platforms and industrial plants.
Clamping Installation Method
Clamping is the quickest and easiest method for installing galvanised steel walkway grating. It is a non-permanent solution that requires no welding or drilling.
- Fast & Simple Installation: Grating clamps secure the panels in place without the need for specialized tools.
- No Structural Damage: Since no welding or bolting is involved, the underlying structure remains intact.
- Limited to Lighter Loads: While effective for general applications, clamping may not be suitable for heavy-duty industrial settings.
- Applications: Common in temporary walkways, maintenance access platforms, and situations where frequent removal is necessary.
The choice of installation method for galvanised steel walkway grating depends on the specific needs of the project. Welding provides maximum strength and durability, bolting offers flexibility and easy removal, while clamping allows for quick and non-invasive installation. Understanding these methods helps ensure safe and efficient installation for various industrial, commercial, and architectural applications.
Key Properties of Fiberglass Sheet vs Steel Sheet Revealed
Applications of Galvanised Steel Walkway Grating
The versatility and durability of galvanised steel walkway grating make it a preferred material for a variety of applications across multiple sectors. Here, we explore at least nine key areas where this sturdy, reliable material is commonly implemented:
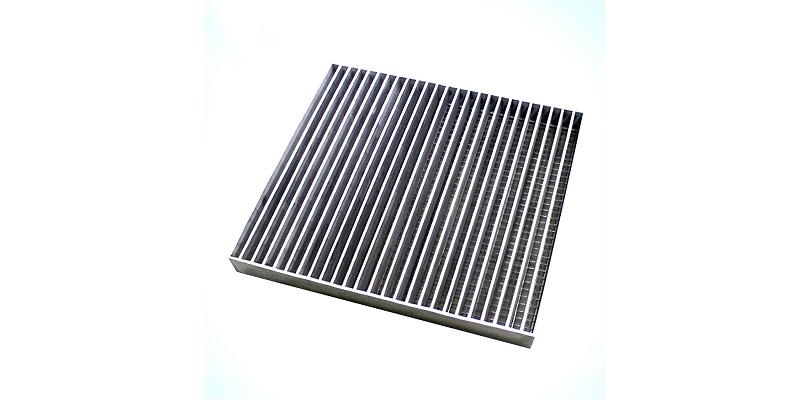
Industrial Usage
In heavy industrial environments, galvanised steel walkway grating is indispensable due to its robustness and ability to withstand harsh conditions. Examples include:
- Oil and Gas Industry: Platforms, walkways, and stair treads in refineries and processing plants are often made from galvanised steel grating, especially black steel grating, due to its resistance to slips, spills, and extreme conditions.
- Water Treatment Plants: Gratings, such as channel gratings, are used over open channels and between tanks for secure maintenance pathways and to cover drainage areas, preventing accidents and facilitating easy access for inspections and repairs.
- Power Plants: Walkways around turbines and cooling towers utilize galvanised grating to ensure safety and provide extensive durability under high-load conditions.
Commercial Spaces
Beyond industrial applications, galvanised steel walkway grating also enhances functionality and aesthetic in various commercial settings:
- Shopping Malls: It is used in parking lots, service areas, and as decorative elements that double as robust walking surfaces.
- Parks and Recreational Areas: Bridges and walkways are often constructed from galvanised grating to ensure longevity and safety in public spaces exposed to diverse weather conditions.
- Architectural Features: Frequently used in faҫades, screens, and sunshades, its versatility offers both utility and visual appeal.
Safety and Accessibility
Safety features of galvanised steel walkway grating include:
- Anti-Slip Surfaces: The grating is often manufactured with serrated edges to provide a high-traction surface, reducing the risk of slips and falls in wet or oily conditions.
- High Load-Bearing Capabilities: Designed to support heavy loads, this grating ensures structural integrity in high-traffic areas, making it ideal for safety and accessibility.
- ADA Compliance: Specific designs conform to the Americans with Disabilities Act to accommodate wheelchairs and other mobility devices, providing safe and universal access.
Additional Considerations
The use of galvanised steel walkway grating extends beyond functional requirements; it also offers aesthetic contributions to the settings in which it is installed. Its open design does not obstruct light or air flow, making it an excellent choice for environmentally sensitive and visually dependent applications.
Through these examples, it’s clear that galvanized steel grating walkway is not only practical due to its durability and safety features, but also remarkably adaptable across a broad range of applications. Whether used in heavy industrial settings or as integral components in commercial and public spaces, it proves to be an indispensable material in modern architectural and engineering projects.
Maintenance and Care of Galvanised Steel Walkway Grating
Proper maintenance and care are crucial to extend the lifespan and ensure the optimal performance of galvanised steel walkway grating. Here are ten essential tips:
- Regular Cleaning: Frequently remove debris and dirt buildup to prevent the grating from becoming slippery and to minimize the risk of corrosion under debris accumulation.
- Inspection Routine: Establish a routine inspection schedule to check for any signs of wear or damage. Early detection of issues like cracks, rust spots, or loosened bolts can prevent more extensive damage and costly repairs.
- Immediate Repairs: Address any damage as soon as possible. If any part of the galvanised steel walkway grating is damaged, repair or replace it immediately to maintain safety and integrity.
- Avoid Harsh Chemicals: When cleaning, use mild detergents and avoid harsh chemicals that could damage the zinc coating which offers protection against corrosion.
- Rinse Thoroughly: After cleaning with detergents, rinse the galvanized steel walkway grating thoroughly with clean water to remove any chemical residues.
- Proper Drainage: Ensure proper drainage around the installed areas. Water pooling can lead to increased risk of corrosion over time, especially if pollutants are present in the water.
- Check for Rust: While galvanised steel is corrosion-resistant, it isn’t entirely rust-proof. Regularly check areas with damaged galvanization for rust and address them according to maintenance protocols.
- Load Management: Avoid placing loads on the grating that exceed its design capacity. Overloading can cause structural deformation and fatigue, shortening its usable life.
- Use Protective Coatings: Occasionally, applying additional protective coatings can help prolong the life of the grating, especially in highly corrosive environments.
- Professional Consultation: When in doubt about the condition or maintenance practices, consult with professionals. It is important to adhere to the manufacturer’s guidelines or seek expert maintenance services to handle specific issues effectively.
Adhering to these maintenance tips ensures that the galvanised steel walkway grating continues to perform safely and effectively, maintaining its structural integrity and appearance over an extended period. Regular and thoughtful care not only enhances performance but also maximizes the return on investment by extending the grating’s lifespan.
High-Quality Bar Grating from Leading Steel Grating Factory
How to Choose Galvanized Steel Walkway Grating
Choosing the right galvanized steel walkway grating is crucial to ensuring safety, durability, and functionality in various applications, such as industrial facilities, commercial buildings, and outdoor walkways. Several factors must be considered when selecting grating, including load capacity, coating type, regulatory compliance, environmental conditions, aesthetics, installation requirements, and maintenance. This guide provides an in-depth analysis of each of these aspects to help buyers make an informed decision.
Load Capacity Requirements
One of the most critical factors when choosing galvanized steel walkway grating is its ability to support the expected load. Different grating types offer varying levels of strength and durability.
- Press-Locked Grating: Designed for high-load applications, such as industrial walkways and public access areas. It provides excellent strength and stability due to the interlocking process that secures the bars together.
- Welded Steel Grating: Ideal for areas with moderate foot traffic. It consists of bearing bars welded together to form a sturdy structure, making it suitable for light-duty applications.
- Bar Spacing Considerations: The spacing between the bearing bars affects the load capacity and safety. Closer spacing increases strength and prevents small objects from falling through.
Galvanized Coating Type
The type of galvanized coating significantly impacts the grating’s durability and resistance to corrosion, especially in harsh environments.
- Hot-Dipped Galvanizing: This method involves immersing the grating in molten zinc, creating a thick and durable coating. It provides superior corrosion resistance and is ideal for outdoor and industrial environments exposed to moisture, chemicals, and extreme temperatures.
- Electro-Galvanizing: A thinner zinc coating is applied using an electrochemical process. While it offers some corrosion resistance, it is less durable than hot-dipped galvanizing and is best suited for indoor applications with minimal exposure to harsh conditions.
Regulations and Standards
Compliance with industry regulations and safety standards is essential to ensure the grating meets performance and safety requirements.
- Load-Bearing Standards: Different industries have specific guidelines for the minimum load capacity of walkway gratings. These standards ensure structural integrity and prevent accidents.
- Mesh Size and Slip Resistance: Regulatory bodies may dictate the maximum allowable mesh size to enhance safety and prevent slipping or objects from falling through.
- Fire and Structural Codes: Some applications require fire-resistant grating materials to comply with building codes and safety regulations.
Environmental Conditions
The lifespan of galvanized steel walkway grating depends on the environmental conditions in which it is installed. Choosing the right grating ensures long-term durability and minimal maintenance.
- Moisture and Humidity: High moisture levels can accelerate corrosion. Hot-dipped galvanized grating is recommended for areas exposed to rain, snow, or high humidity.
- Chemical Exposure: Industrial settings with chemical exposure require grating with enhanced corrosion resistance, such as coatings with additional protective layers.
- Temperature Extremes: Prolonged exposure to extreme heat or cold can impact the structural integrity of the grating. Selecting materials designed for specific temperature ranges ensures longevity.
Aesthetics
While functionality is the primary concern, the visual appeal of the grating also plays a role in certain applications. The right choice enhances the overall appearance of the space.
- Color and Finish: Some gratings come in different finishes or can be painted to match the surrounding environment.
- Pattern and Design: Decorative grating designs can add aesthetic value while maintaining safety and durability.
- Surface Texture: Smooth, serrated, or patterned surfaces offer different levels of slip resistance and visual appeal.
Installation Requirements
Proper installation is essential for maximizing the safety and effectiveness of galvanized steel walkway grating. Buyers should consider factors that affect the ease and cost of installation.
- Panel Size and Shape: Grating should be sized appropriately for the available space. Some products allow for customization to fit specific dimensions.
- Support Structure Compatibility: Ensuring compatibility with existing or planned support structures simplifies installation and reduces costs.
- Installation Tools and Techniques: Some grating types require specialized tools or welding, while others can be secured with simple fasteners. Choosing the right installation method enhances efficiency.
Maintenance
Long-term maintenance requirements influence the total cost of ownership and the lifespan of galvanized steel walkway grating. Choosing a low-maintenance option reduces ongoing expenses.
- Cleaning Needs: Grating with open spaces is easier to clean and prevents debris buildup. Regular cleaning helps maintain slip resistance and appearance.
- Corrosion Prevention: Regular inspections for signs of wear, corrosion, or damage can extend the grating’s lifespan. Hot-dipped galvanized grating requires minimal maintenance due to its durable coating.
- Replacement Considerations: In high-traffic areas, choosing grating that allows for easy replacement of individual sections can save time and cost in case of damage.
Selecting the right galvanized steel walkway grating requires careful evaluation of load capacity, coating type, compliance with regulations, environmental conditions, aesthetics, installation requirements, and maintenance needs. By considering these factors, buyers can ensure they choose a durable, safe, and cost-effective grating solution that meets their specific application requirements.
Service Life of Galvanised Steel Walkway Grating: Key Factors and Considerations
The service life of galvanised steel walkway grating depends on multiple factors, including the quality of galvanization, environmental conditions, load-bearing capacity, maintenance practices, and the specific application. Understanding these factors helps in estimating its longevity and ensuring optimal performance in various settings. In general, galvanized steel walkway grating can last 20 to 50 years or more, depending on the conditions it is exposed to. Below, we explore the key aspects that influence its service life in detail.
Quality of Galvanization
The durability of galvanized steel walkway grating heavily depends on the quality and type of galvanization applied. Proper galvanization enhances corrosion resistance and extends the lifespan of the grating.
- Hot-Dip Galvanization: This method provides a thick zinc coating, significantly increasing resistance to rust and environmental degradation. Hot-dip galvanized grating typically lasts 30 to 50 years in moderate conditions and 10 to 25 years in highly corrosive environments.
- Electro-Galvanization: This process creates a thinner zinc layer, offering lower corrosion resistance. It is more suitable for indoor applications, where the service life may extend beyond 20 years if not exposed to harsh weather or chemicals.
Environmental Conditions
The surrounding environment plays a crucial role in determining the longevity of galvanized steel walkway grating. Exposure to harsh conditions can accelerate wear and reduce its service life.
- Industrial and Chemical Exposure: In facilities with chemical exposure, such as factories and processing plants, the protective zinc coating may degrade faster, reducing the grating’s lifespan to 10 to 25 years.
- Outdoor Weather Conditions: Areas with high humidity, frequent rainfall, or coastal locations with salt-laden air may lead to faster corrosion, reducing longevity to 15 to 30 years.
- Mild and Indoor Environments: In controlled environments with minimal exposure to moisture and chemicals, galvanized grating can last 40 to 50 years or more.
Load-Bearing and Structural Stress
The service life of galvanized steel walkway grating also depends on the type and intensity of load it carries over time.
- Heavy-Duty Industrial Use: High foot traffic, heavy equipment, and vehicle loads can cause mechanical wear and structural fatigue, shortening its lifespan to around 15 to 30 years, depending on the thickness and quality of the grating.
- Moderate Foot Traffic: In commercial and residential applications with moderate load requirements, the grating may last 30 to 50 years with minimal wear.
- Occasional or Light Use: Gratings used in areas with minimal load-bearing requirements (such as decorative applications) can remain functional for over 50 years.
Maintenance Practices
Regular maintenance plays a key role in prolonging the service life of galvanized steel walkway grating. Proper care prevents corrosion, structural damage, and deterioration over time.
- Cleaning: Removing debris, dirt, and chemical residues prevents buildup that could accelerate corrosion, thereby extending the grating’s lifespan.
- Inspection and Repairs: Routine inspections for rust, structural integrity, and coating damage allow for timely repairs, preventing further deterioration.
- Re-Galvanization: If the zinc coating starts wearing off, re-galvanization can significantly extend the grating’s service life beyond its initial expectancy.
Application-Specific Lifespan
Different applications affect the longevity of galvanized steel walkway grating. Selecting the right type for a specific use ensures maximum durability.
- Industrial Plants and Factories: Exposure to chemicals, heat, and mechanical stress may limit the lifespan to 15 to 30 years.
- Outdoor Public Walkways: Subject to weather conditions and pedestrian traffic, these gratings typically last 20 to 40 years.
- Indoor Commercial and Residential Use: Protected from extreme elements, indoor gratings can last 40 to 50 years or more.
The service life of galvanized steel walkway grating varies widely depending on galvanization quality, environmental exposure, load capacity, maintenance efforts, and application type. In ideal conditions, galvanized steel grating can last over 50 years, while harsh environments may reduce this to 10 to 25 years. Understanding these factors helps in selecting the right grating and implementing proper maintenance to maximize its durability and effectiveness.
Difference Between Galvanised Steel Walkway Grating and Electro-Galvanised Walkway
Galvanised steel walkway grating and electro-galvanised walkway grating are two types of corrosion-resistant steel grating used in industrial, commercial, and architectural applications. While both offer protection against rust and environmental damage, they differ in the galvanisation process, durability, cost, and application. Understanding these differences helps in selecting the most suitable type of grating for specific conditions. Below, we explore the key distinctions between these two types of walkway grating.
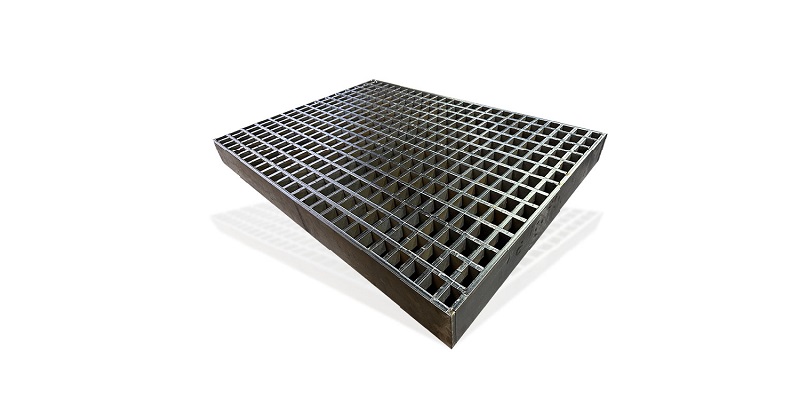
Galvanisation Process
The primary difference between galvanised steel walkway grating and electro-galvanised walkway grating lies in their galvanisation process. The method used affects the thickness of the zinc coating and the overall durability of the grating.
- Galvanised Steel Walkway Grating (Hot-Dip Galvanisation): This process involves immersing steel grating in molten zinc, which forms a thick, durable zinc coating. This method provides superior corrosion resistance, making it ideal for outdoor and heavy-duty applications.
- Electro-Galvanised Walkway Grating: This type is coated with zinc through an electrochemical process, where a thin layer of zinc is deposited onto the steel using an electric current. While this process offers some level of corrosion resistance, the zinc layer is much thinner than that of hot-dip galvanisation, making it less durable in harsh environments.
Corrosion Resistance & Durability
Both types of grating provide corrosion resistance, but their effectiveness varies depending on the exposure to environmental conditions.
- Galvanised Steel Walkway Grating: The hot-dip galvanisation process provides a thick zinc coating that offers long-term protection against rust and corrosion. It is ideal for outdoor applications, marine environments, and industrial settings where exposure to moisture and chemicals is high.
- Electro-Galvanised Walkway Grating: Due to the thin zinc coating, electro-galvanised grating is more susceptible to rust and wear, especially in high-humidity or corrosive environments. It is better suited for indoor applications or areas with minimal exposure to harsh weather conditions.
Strength & Load Capacity
The strength of walkway grating is crucial for applications requiring high load-bearing capacity.
- Galvanised Steel Walkway Grating: The hot-dip galvanisation process does not alter the structural strength of the steel, making it a preferred choice for heavy-duty applications such as bridges, industrial flooring, and high-traffic walkways.
- Electro-Galvanised Walkway Grating: While still strong, the thinner coating and less intensive galvanisation process make electro-galvanised grating less suitable for heavy-load environments. It is often used in decorative or low-impact applications.
Cost & Application
The cost-effectiveness of each type of grating depends on the initial investment and long-term maintenance requirements.
- Galvanised Steel Walkway Grating: Although hot-dip galvanised grating has a higher initial cost, its durability and minimal maintenance needs make it a cost-effective solution for long-term use. It is commonly used in industrial plants, offshore platforms, and construction projects.
- Electro-Galvanised Walkway Grating: This type is generally more affordable upfront but may require more frequent replacement or maintenance due to its lower corrosion resistance. It is typically used in indoor facilities, warehouses, and areas with controlled environmental conditions.
Galvanised steel walkway grating and electro-galvanised walkway grating differ primarily in their galvanisation process, durability, corrosion resistance, and cost. Hot-dip galvanised grating provides superior protection, strength, and longevity, making it ideal for outdoor and heavy-duty applications. Electro-galvanised grating, while more cost-effective initially, is better suited for indoor or low-impact environments. Choosing the right type depends on the specific application and exposure conditions to ensure optimal performance and longevity.
Can Galvanised Steel Walkway Grating Be Used in Coastal Areas?
Galvanised steel walkway grating is widely used in various environments, but its performance in coastal areas requires special consideration due to the harsh conditions, including high humidity, salt-laden air, and potential exposure to seawater. While galvanised steel grating can be used in coastal applications, its longevity and performance depend on factors such as the type of galvanization, environmental exposure, maintenance, and additional protective measures. Below, we examine these aspects to understand whether galvanised steel walkway grating is a suitable choice for coastal environments.
Corrosion Resistance in Coastal Environments
One of the biggest challenges in coastal areas is the high level of corrosion caused by moisture and salt exposure. Galvanized steel grating is designed to resist corrosion, but the level of protection depends on the type of galvanization used.
- Hot-Dip Galvanisation: This method provides a thick zinc coating that offers enhanced protection against rust and corrosion. In coastal environments, hot-dip galvanized grating is the preferred choice, as it can withstand saltwater exposure much better than electro-galvanized steel.
- Electro-Galvanisation: This process creates a thinner zinc coating, making it less resistant to harsh coastal conditions. Electro-galvanized grating may deteriorate faster due to the continuous presence of moisture and salt, leading to premature corrosion.
- Expected Lifespan in Coastal Conditions: In marine environments, hot-dip galvanized steel walkway grating can last around 10 to 25 years, depending on maintenance and exposure levels. Electro-galvanized options may last significantly shorter.
Effect of Salt and Humidity
Salt and humidity in coastal areas can accelerate the breakdown of protective coatings, affecting the durability of galvanised steel walkway grating.
- Salt-Laden Air: Continuous exposure to salty air can cause zinc coatings to erode faster, exposing the underlying steel to corrosion. Grating installed near oceanfront locations requires additional protective measures to prolong its lifespan.
- Direct Contact with Seawater: If the grating is exposed to seawater splashes or submerged periodically, corrosion will accelerate, and special coatings or alternative materials may be necessary.
- Humidity Impact: High humidity increases the rate of oxidation, which can weaken the structural integrity of the grating over time. Regular inspections and protective coatings help combat this issue.
Maintenance Requirements for Coastal Applications
In coastal areas, regular maintenance is necessary to maximize the lifespan and performance of galvanised steel walkway grating.
- Routine Cleaning: Washing away accumulated salt deposits helps slow down the corrosion process. Periodic freshwater rinsing is recommended for grating exposed to salt air.
- Inspection for Rust and Damage: Regular checks ensure early detection of rust spots, which can be treated before they spread and compromise the structural integrity of the grating.
- Re-Galvanization or Coating Application: Applying an additional protective coating, such as marine-grade paint or a corrosion-resistant sealant, can enhance durability in coastal environments.
Alternative Materials for Coastal Conditions
While galvanised steel walkway grating is a viable option for coastal areas, some alternatives may offer longer-lasting performance with lower maintenance.
- Stainless Steel Grating: Stainless steel, particularly grade 316, provides excellent corrosion resistance and is often recommended for highly corrosive environments such as coastal and marine locations. However, it is significantly more expensive than galvanised steel.
- FRP (Fiberglass Reinforced Plastic) Grating: This non-metallic alternative is resistant to salt, chemicals, and moisture, making it an excellent option for environments where corrosion is a major concern. It is lightweight, durable, and requires minimal maintenance.
Galvanised steel walkway grating can be used in coastal areas, but its durability depends on the type of galvanization, environmental exposure, and maintenance practices. Hot-dip galvanized grating is the best choice for coastal environments due to its superior corrosion resistance, while electro-galvanized grating is less suitable for such conditions. Regular cleaning, inspections, and additional protective coatings can help prolong its service life. However, for extreme coastal conditions with prolonged salt exposure, alternatives like stainless steel or FRP grating may provide better long-term performance.
FAQs about Galvanised Steel Walkway Grating
Galvanized steel grating is a durable, corrosion-resistant metal grating made by coating mild steel with zinc through hot-dip galvanization or electro-galvanization. This process enhances the grating’s longevity by protecting it from rust and environmental damage. It is widely used in industrial, commercial, and public infrastructure applications such as walkways, platforms, stair treads, drainage covers, and ventilation grilles. Galvanized steel walkway grating offers high load-bearing capacity, slip resistance, and ease of installation, making it an ideal choice for areas exposed to harsh conditions.
GRP (Glass Reinforced Plastic) grating is lightweight, non-corrosive, and resistant to chemicals, making it suitable for marine or chemical environments. However, galvanized steel walkway grating is stronger, more durable, and capable of handling higher loads, making it ideal for heavy-duty applications such as industrial walkways, platforms, and bridges. While GRP is preferred for corrosion-prone environments, steel grating remains the best option for strength, longevity, and cost-effectiveness in most structural applications.
In galvanized steel walkway grating, “19 W/4” refers to the bar spacing and configuration. The “19” indicates that the bearing bars are spaced 19/16 inches (or 1.1875 inches) apart, while “W” denotes welded grating. The “4” signifies that the cross bars are spaced 4 inches apart. This configuration provides high strength and durability, making it suitable for walkways, platforms, and industrial flooring where load-bearing capacity and slip resistance are essential.
15W4 grating is a welded steel grating where the bearing bars are spaced 15/16 inches apart, and the cross bars are spaced 4 inches apart. The “W” stands for welded construction, ensuring strength and stability. This type of galvanized steel walkway grating is commonly used in heavy-duty industrial applications, including platforms, stair treads, and drainage covers, where a strong, corrosion-resistant, and slip-resistant surface is required for safety and durability.
The best grating depends on the application. Galvanized steel walkway grating is preferred for heavy-duty and industrial uses due to its high strength, durability, and corrosion resistance. It is ideal for walkways, platforms, and bridges. GRP grating is better suited for chemical or marine environments where corrosion resistance and lightweight properties are priorities. Stainless steel grating is used in highly corrosive environments requiring high hygiene standards.
A grating with 3500 lines per cm is an optical diffraction grating used to disperse light into its component wavelengths. While this is more relevant in spectroscopy, in galvanized steel walkway grating, finer mesh patterns improve grip and drainage. Such high line densities are not typically used in industrial steel gratings but are significant in optical and scientific applications.
The minimum bearing length for galvanized steel walkway grating depends on the load and span. Generally, a bearing length of at least 1 inch is required for lighter applications, while industrial walkways and platforms need at least 1.5 inches to 2 inches for proper load distribution. Ensuring adequate bearing length improves safety and longevity.
A grating with 300 lines per mm refers to an optical diffraction grating, commonly used in scientific instruments. In the context of galvanized steel walkway grating, spacing between bearing bars determines strength, load capacity, and slip resistance. Standard steel grating does not use such high-density line measurements but follows industry standards for spacing based on load requirements.
The width of galvanized steel walkway grating is calculated based on the number of bearing bars and their spacing:
Width = (Number of bearing bars – 1) × Bar spacing + Bearing bar width
This formula helps determine the correct dimensions for walkways, platforms, and drainage applications, ensuring load capacity and structural stability.
The standard size of galvanized steel walkway grating varies based on application. Common panel sizes are 1m × 6m or 3ft × 20ft. Bearing bar thickness typically ranges from 3mm to 6mm, with spacing options such as 19W4 or 15W4. Custom sizes can be manufactured to meet specific project needs.
Grating spacing is calculated based on the required load capacity and application. For example, in a 19W4 galvanized steel walkway grating, bearing bars are spaced 1.1875 inches (19/16 inches) apart, while cross bars are 4 inches apart. The formula considers safety requirements, slip resistance, and drainage efficiency.
Heavy-duty galvanized steel walkway grating typically has bearing bars ranging from 6mm to 12mm thick, depending on the load requirements. Thicker bars provide higher strength, making them ideal for industrial flooring, bridges, and platforms subject to heavy vehicular or pedestrian traffic.
A grating with 15,000 lines per inch has a line spacing of:
1 inch = 2.54 cm → 15,000 lines per inch = 15,000 ÷ 2.54 ≈ 5905.5 lines per cm.
This applies to optical diffraction gratings rather than galvanized steel walkway grating, where spacing is measured in inches or millimeters for industrial use.
Galvanized steel walkway grating comes in various sizes based on bearing bar spacing and thickness. Common sizes include 19W4, 15W4, and 30W4, with standard panel dimensions of 1m × 6m (or 3ft × 20ft). Custom sizes are available based on specific structural needs.
SS grating refers to stainless steel grating, which is highly corrosion-resistant and used in extreme environments, such as chemical plants, food processing facilities, and marine applications. While galvanized steel walkway grating is more cost-effective and widely used in infrastructure, SS grating is preferred for hygienic and highly corrosive conditions.
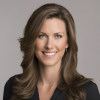
As the editor of GangLong Fiberglass, I have years of experience and in-depth research, focusing on cable tray products, fiberglass solutions, and grille systems. I incorporate years of industry insights and practical experience into every content, committed to promoting the progress of the industry. At GangLong Fiberglass, my commitment is reflected in every product, from innovative cable trays to durable fiberglass solutions and sturdy grille systems. As an authoritative voice in the industry, my goal is to provide valuable information to professionals and businesses and promote forward-looking solutions.