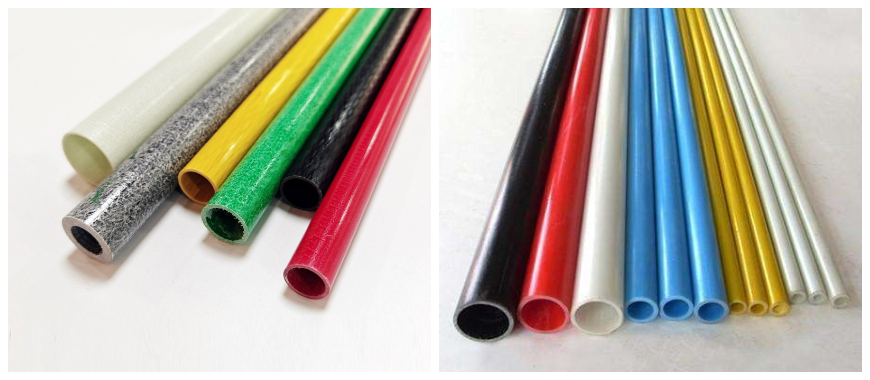
Large fiberglass tubes are essential components in numerous industries, offering unique advantages over traditional materials. Known for their lightweight yet strong nature, these tubes are used extensively in construction, transportation, and marine applications. Their corrosion resistance ensures durability, making them ideal for outdoor and industrial environments.Large fiberglass tubes can be manufactured in various sizes and shapes, accommodating diverse project requirements. The versatility of these tubes allows for innovative design solutions, enhancing both functionality and aesthetic appeal. Large fiberglass tubes, lightweight, strong, corrosion-resistant, and non-conductive, are perfect for industrial, construction, and hobby applications.
What Are Large Fiberglass Pipes?
Large fiberglass tubes are engineered products made from fiberglass materials. They are designed to meet the needs of various applications across different industries.
Large fiberglass pipes are specialized, engineered products made from fiberglass composite materials. These pipes are designed to offer a solution to many challenging requirements in industrial, construction, and environmental applications. While large fiberglass pipes can vary in size, composition, and design, they are generally produced by reinforcing glass fibers within a resin matrix to create a durable, yet lightweight product. Their use extends across multiple sectors, driven by the combination of strength, low weight, and resistance to environmental factors. Below, we’ll explore the different aspects of large fiberglass pipes, from how they are made to the standards that define their manufacturing.
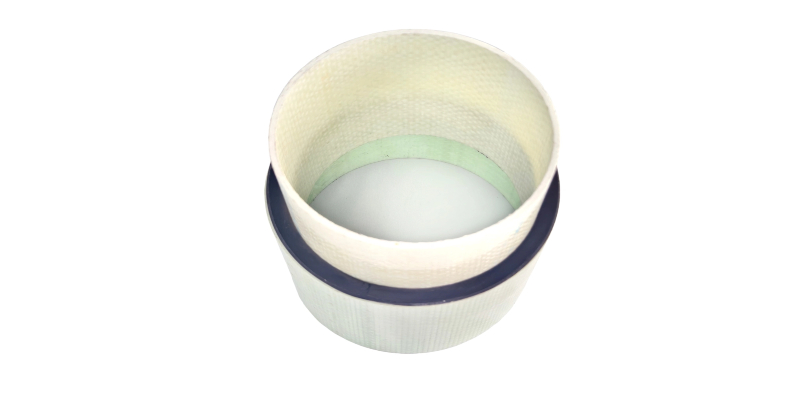
Manufacturing Process
The process of creating large fiberglass pipes involves a careful and precise combination of materials and techniques. Fiberglass pipes are typically made using a method called filament winding or centrifugal casting. In filament winding, continuous glass fibers are impregnated with resin and wound onto a mandrel in a specific pattern to create the pipe’s structure. Centrifugal casting, on the other hand, involves pouring resin and glass fiber into a rotating mold to form the pipe. These methods ensure that the resulting pipes have a uniform structure and strength, which is crucial for their performance under pressure or in challenging environments.
Material Composition
Large fiberglass pipes are made from a composite material, combining glass fibers with a resin matrix, typically polyester, vinyl ester, or epoxy. The glass fibers provide tensile strength and rigidity, while the resin binds the fibers together and gives the pipe its shape and form. The exact composition can vary depending on the intended use of the pipes, with certain resins and fiber types offering better resistance to chemicals, heat, or corrosion. This versatility in material selection makes large fiberglass pipes adaptable to a variety of applications across different industries.
Standards and Regulations
Large fiberglass pipes are manufactured according to stringent industry standards and regulations to ensure their safety and effectiveness. These standards vary by region and application but generally require that fiberglass pipes meet specific performance criteria such as pressure rating, impact resistance, and chemical compatibility. For example, the American Water Works Association (AWWA) and the ASTM (American Society for Testing and Materials) set guidelines for the design and manufacturing of these pipes, ensuring they meet both national and international quality benchmarks. Complying with these standards ensures that the pipes are reliable and safe for use in critical applications.
Installation Considerations
The installation of large fiberglass pipes is an important aspect of their performance. Since these pipes are lightweight compared to alternatives like steel or concrete, they are easier to handle and install, requiring fewer resources for transportation and labor. However, proper installation is still critical to avoid damaging the pipes or compromising their performance. Typically, fiberglass pipes are installed using standard piping techniques, but care must be taken to ensure proper sealing, alignment, and support during installation to prevent leakage or structural failure.
Large fiberglass pipes are sophisticated products made to offer a balance of strength, durability, and adaptability for various industrial uses. The combination of glass fibers and resin provides excellent resistance to corrosion, high strength-to-weight ratios, and the flexibility to be customized for different needs. The production process, material selection, and adherence to industry standards all contribute to the superior performance of these pipes in demanding environments.
Why FRP Pipe Railing is Ideal for Outdoor Installations
Features and Advantages of Large Fiberglass Pipes
Large fiberglass pipes are engineered products that stand out due to their unique combination of features, making them highly suitable for a variety of demanding applications. In this section, we will explore the key features of these pipes, followed by their advantages that make them indispensable in various industries. While features describe the inherent qualities that define the material, advantages explain how these features translate into practical benefits for users.
Features of Large Fiberglass Pipes
The features of large fiberglass pipes are the characteristics that give them the ability to perform reliably across a broad range of applications. These attributes stem from the specific materials used in their manufacture and their design, which contribute to their overall performance and utility.
Impressive Strength-to-Weight Ratio
One key fiberglass tube property is the strength-to-weight ratio, which makes these pipes an ideal solution for applications where both strength and lightweight performance are required. The fiberglass composite construction allows the pipes to support heavy loads and withstand significant internal pressure, all while maintaining a reduced weight compared to traditional materials like steel or concrete. This feature enables easier handling and installation, particularly in environments where weight reduction is crucial, such as in aerospace or transportation projects.
Transparency for Visual Inspection
Fiberglass pipes often feature a degree of transparency, which is especially valuable for industries such as water treatment. The ability to visually inspect the contents of the pipe without disassembling it makes it easier to monitor flow and detect any blockages or issues. This feature enhances operational efficiency by reducing downtime and improving maintenance practices.
Non-Conductive Properties
Another prominent fiberglass tube property is their non-conductivity. The pipes are naturally resistant to electricity, making them an excellent choice for electrical applications where the risk of electrical faults must be minimized. This non-conductive nature reduces the chance of short circuits and electrical hazards, offering a higher level of safety in environments like telecommunications, fluid power systems, and industrial settings where electrical systems are in close proximity.
Corrosion and Chemical Resistance
Fiberglass pipes are known for their remarkable durability, particularly their resistance to corrosion and chemicals. Unlike metal pipes, fiberglass does not corrode when exposed to water, chemicals, or environmental elements. This feature is especially important in industries such as oil and gas, marine, and wastewater treatment, where pipes are exposed to harsh conditions. The resistance to corrosion greatly extends the lifespan of the pipes and ensures minimal maintenance requirements over time.
Versatility in Application
The versatility of large fiberglass pipes is evident in their ability to be adapted for various applications. They come in different sizes and specifications, allowing for customization to meet specific project requirements. Additionally, the innovations in small diameter fiberglass tubes production have further expanded the possibilities, allowing these pipes to be used in more specialized applications, such as precise fluid power systems and smaller, more intricate constructions.
Advantages of Large Fiberglass Pipes
While the features describe the inherent qualities of large fiberglass pipes, the advantages focus on how these qualities translate into real-world benefits. These advantages make fiberglass pipes an attractive choice for industries across the board.
Enhanced Strength and Durability
One of the primary advantages of large fiberglass pipes is their strength and durability. The fiberglass tube property of being both strong and lightweight offers superior performance compared to other materials like steel, aluminum, and PVC. The ability to withstand high pressure, resist cracking, and handle external loads makes fiberglass pipes ideal for critical infrastructure projects. Their corrosion resistance enhances their longevity, reducing the frequency of repairs and replacements, leading to significant cost savings over time.
Reduced Maintenance Costs
The resistance to corrosion, chemicals, and environmental stress significantly lowers maintenance costs associated with large fiberglass pipes. Since fiberglass does not deteriorate in the presence of moisture, salt, or chemicals, these pipes have a longer lifespan and require less frequent upkeep. Additionally, the smooth inner surface of fiberglass reduces the chances of build-up and blockages, further reducing the need for maintenance. This translates to reduced downtime and operational costs, making fiberglass pipes a cost-effective long-term solution.
Safety in High-Voltage and Electrical Environments
The non-conductive property of large fiberglass pipes offers an advantage in high-voltage or electrical environments, providing essential safety in applications where electrical systems are involved. By using fiberglass pipes, industries can prevent potential electrical hazards such as short circuits and equipment failure. This is particularly valuable in industries such as telecommunications, electrical conduit systems, and fluid power systems, where safety is a primary concern.
Adaptability Across Industries
Large fiberglass pipes offer versatility across industries, making them applicable in a wide range of settings. Their ability to withstand extreme environmental conditions and resist corrosion makes them highly adaptable to industries like marine, wastewater treatment, and oil and gas. The innovations in small diameter fiberglass tubes production also allow these pipes to be used in more specialized areas, such as telecommunication conduits and fluid management systems. The versatility ensures that fiberglass pipes can be integrated into almost any infrastructure project requiring reliable performance.
Ease of Installation and Transportation
Another key advantage is the ease of installation and transportation of large fiberglass pipes. Due to their lightweight nature, fiberglass pipes are much easier to handle compared to heavier materials like steel or concrete. This reduces transportation costs and simplifies installation procedures. The ability to customize the pipe length on-site further enhances installation efficiency, making it an ideal option for projects where speed and cost-effectiveness are critical.
Large fiberglass pipes are engineered to offer significant benefits in various industrial and commercial applications, thanks to their unique features and resulting advantages. Their combination of strength, lightweight properties, durability, and versatility makes them ideal for demanding environments. As discussed, the features of these pipes, such as the fiberglass tube property of being non-conductive and resistant to corrosion, contribute to their outstanding performance, while the advantages of cost savings, safety, and adaptability further enhance their appeal. Additionally, fiberglass bondage tubes, often used in specialized applications, share similar benefits and are an extension of the versatility and reliability offered by large fiberglass pipes. With ongoing innovations in small diameter fiberglass tubes production, the range of applications for these pipes continues to expand, offering solutions across a variety of industries.
Key Advantages of Using Hollow Fiberglass Tube in Construction
Pricing of Large Fiberglass Tubes
Factors Influencing the Price of Large Fiberglass Tubes
Several factors determine the price of a large fiberglass tube, making the cost vary depending on specific project needs.
- Material quality is one of the primary considerations. Tubes made from higher-grade fiberglass resins and reinforced with advanced additives typically cost more due to their superior performance characteristics.
- Size is another crucial factor. Larger tubes or those with thick wall fiberglass tubes require more material, increasing their overall price. On the other hand, thin wall fiberglass tubes can provide a cost-effective solution by using less material while still meeting strength requirements for specific applications, making them ideal for lightweight and space-sensitive projects.
- Customization also plays a significant role in pricing. Tubes designed with specific features, such as added UV protection, fire resistance, or special dimensions, tend to be more expensive. The complexity of manufacturing processes and lead times can influence the final cost of large fiberglass tubes, especially in projects requiring specialized designs or shorter turnaround times.
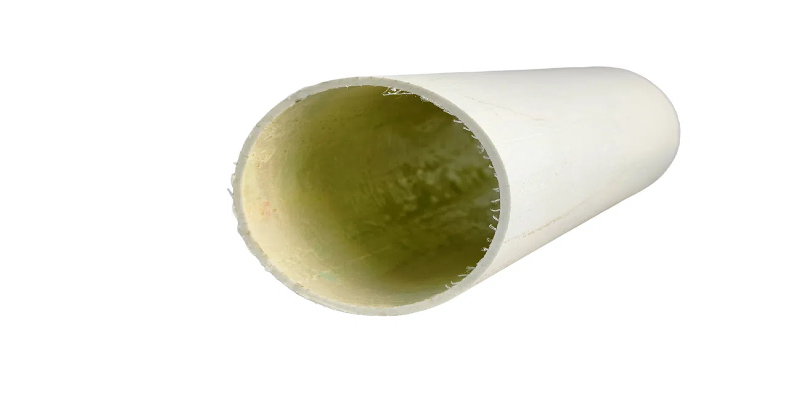
Average Price Range for Large Fiberglass Tubes
The average price range for large fiberglass tube components varies depending on the factors mentioned above. Bulk orders may benefit from discounted pricing, reducing the cost per unit for large-scale projects. While fiberglass tube/component may initially appear more expensive compared to other materials, their long-term durability and low maintenance requirements often result in cost savings over time.
Applications of Large Diameter Fiberglass Tubes
Large fiberglass tubes are widely used for their versatility.
Their unique characteristics make them an ideal choice for both structural and functional applications, providing significant benefits over traditional materials like steel or aluminum. Large diameter fiberglass tubes are particularly useful in industries where strength, corrosion resistance, and durability are essential.
1.Typical Uses in Industries:One common application of large fiberglass tubes is in fluid power systems, where they are used to transport liquids, gases, and chemicals. Their corrosion resistance ensures they perform well in environments that would typically degrade other materials. In pressurized air-oil reservoirs, these tubes offer excellent resistance to internal pressure, preventing leaks and maintaining performance over time.
2.n the construction sector, large fiberglass tubes are used as structural supports, providing a lightweight alternative to metal that doesn’t compromise strength. The marine industry also benefits from large fiberglass tubes due to their ability to withstand harsh, corrosive environments while maintaining integrity.
3.These tubes are used in water treatment plants for piping systems, ensuring durability and preventing contamination. Large fiberglass tubes are increasingly used in telecommunications as protective conduits for wiring, where non-conductivity is crucial for safety.
How to Choose the Right Tapered Fiberglass Tube Size
Advantages Over Alternatives
Compared to materials like steel, aluminum, and PVC, large fiberglass tubes offer several advantages that make them a preferred choice for many applications.
Feature | Large Fiberglass Tubes | Steel | Aluminum | PVC |
---|---|---|---|---|
Corrosion Resistance | High | Low | Medium | Medium |
Impact Strength | Excellent | High | Medium | Low |
Tensile Strength | High | Very High | High | Low |
Weight | Lightweight | Heavy | Lightweight | Lightweight |
Non-conductivity | Yes | No | No | Yes |
Maintenance Costs | Low | High | Medium | Low |
As shown in the table, large fiberglass tubes offer superior impact and tensile strength compared to PVC and aluminum, while being more corrosion-resistant than steel. Their lightweight nature and non-conductive fiberglass properties make them safer and easier to install in various industrial settings.
Key Considerations When Purchasing Large Fiberglass Tubes and How to Choose a Manufacturer
When purchasing large fiberglass tubes, it is crucial to pay attention to several key data features that directly influence the tube’s performance, durability, and suitability for the intended application. Additionally, choosing the right manufacturer is essential to ensure high-quality products and reliable service. In this section, we will explore the critical factors to consider when buying large fiberglass tubes, as well as how to choose the best manufacturer for your needs. This guide will cover data features like material specifications, certifications, and manufacturing standards, along with tips for evaluating potential suppliers based on their expertise, reputation, and production capabilities.
Important Data Features to Consider When Purchasing Large Fiberglass Tubes
Before purchasing large fiberglass tubes, several technical and performance data features should be assessed to ensure the product meets your requirements. These features vary depending on the specific application, but certain attributes are essential for all purchases.
Diameter and Length Specifications
The diameter and length of the fiberglass tubes are among the most crucial data points to consider. Tubes come in various sizes, and it is important to select a product that meets the size requirements of your project. Pay attention to both the outer diameter and wall thickness to ensure proper fit and functionality. Larger diameter tubes, for example, are often needed for high-volume fluid transport, while smaller diameters may be used for electrical conduit systems or structural reinforcement.
Material Composition and Resin Type
Fiberglass tubes are made by combining glass fibers with a resin matrix. The type of resin used (such as polyester, vinyl ester, or epoxy) affects the tube’s performance in various environments. It’s essential to select a resin that aligns with your project’s needs—whether it’s for resistance to heat, chemicals, or UV exposure. Understanding the fiberglass tube property based on its resin type will help you ensure compatibility with the materials or fluids the tube will encounter.
Strength and Load-Bearing Capacity
One of the key data features of large fiberglass tubes is their tensile strength and load-bearing capacity. This data will inform you of the pipe’s ability to withstand internal pressure and external loads without failure. Ensure that the tube you choose is rated to handle the stresses it will be subjected to, especially if it will be used in heavy-duty applications such as fluid power systems, scaffolding, or structural reinforcement.
Corrosion and Chemical Resistance
Fiberglass tubes are valued for their resistance to corrosion and harsh chemicals. However, the level of resistance can vary depending on the resin used and the design of the tube. When making a purchase, be sure to inquire about the chemical compatibility of the fiberglass tube with the substances it will carry or be exposed to. This is particularly important for industries like wastewater treatment, oil and gas, and marine applications.
Pressure Rating and Temperature Tolerance
Pressure rating and temperature tolerance are crucial in ensuring the fiberglass tubes will perform reliably under the conditions they will face. These properties determine how much pressure the tube can handle without failure, as well as the temperature range in which the tube can maintain its structural integrity. Be sure to check these specifications to ensure the fiberglass tube will function effectively within your specific operating conditions.
How to Choose a Large Fiberglass Tubes Manufacturer
Selecting the right manufacturer for large fiberglass tubes is equally important as choosing the correct product. A reputable manufacturer can guarantee the quality, performance, and longevity of the fiberglass tubes you purchase. Below are key factors to consider when evaluating potential manufacturers.
Experience and Expertise
Experience plays a significant role in the quality of the product. Manufacturers with years of experience in producing large fiberglass tubes will have a deeper understanding of material specifications, performance standards, and application requirements. It’s essential to choose a manufacturer who has a proven track record in producing high-quality fiberglass products tailored to your specific needs.
Certifications and Industry Compliance
Ensure the manufacturer complies with industry standards and holds relevant certifications such as ISO 9001, ASTM, or AWWA certifications. These certifications indicate that the manufacturer follows established quality control processes and adheres to international standards for safety, performance, and reliability. Manufacturers who meet these standards are more likely to produce high-quality products that will perform well in your application.
Customization Capabilities
Large fiberglass tubes often require customization to meet specific project requirements. Whether you need tubes with a unique diameter, specific resin type, or enhanced load-bearing capacity, a good manufacturer should be able to provide customization services. Ask potential manufacturers about their ability to tailor products to your needs, ensuring they can accommodate unique specifications or project demands.
Production Capacity and Lead Time
Production capacity and lead time are crucial factors in the decision-making process, especially for large-scale projects. A manufacturer with the ability to produce high volumes of large fiberglass tubes quickly and reliably can help you meet tight deadlines. Make sure to inquire about their production timelines and capacity to handle orders of varying sizes. Timely delivery is crucial to maintaining project schedules and avoiding unnecessary delays.
Customer Support and After-Sales Service
A strong relationship with the manufacturer should extend beyond the sale. Look for manufacturers who offer excellent customer support and after-sales service. This includes assistance with installation, troubleshooting, and any maintenance or warranty issues that may arise. Manufacturers with a customer-focused approach can help ensure that your project runs smoothly even after the initial purchase.
Reputation and Reviews
Finally, it is essential to evaluate the reputation of the manufacturer. Research online reviews, ask for references from previous clients, and assess feedback regarding product quality and customer service. A manufacturer with a strong reputation in the industry is more likely to provide consistent quality and support, ensuring you receive the best fiberglass tubes for your needs.
When purchasing large fiberglass tubes, paying attention to data features such as size specifications, resin type, load-bearing capacity, and resistance to corrosion is essential to ensure you select the right product for your project. Equally important is choosing a manufacturer who offers expertise, certifications, customization capabilities, and reliable customer support. By considering these key aspects, you can make an informed decision that ensures both the quality and performance of the large fiberglass tubes you need.
Shapes of Large Fiberglass Tubes: Round, Square, and Beyond
Large fiberglass tubes come in different shapes, with round and square being the most common. Each shape has its unique characteristics, advantages, and applications. The choice between round and square tubes depends on factors such as load-bearing capacity, aerodynamic efficiency, space utilization, and structural stability. While these two shapes dominate the market, other specialized fiberglass tube shapes also exist for specific industrial and engineering needs. This article will explore the differences between round and square fiberglass tubes, their advantages, common applications, and other potential shapes used in various industries.
Round Fiberglass Tubes: Characteristics, Advantages, and Applications
Round fiberglass tubes are the most widely used shape due to their excellent mechanical properties, structural efficiency, and ability to withstand external forces evenly. Their circular design makes them ideal for applications where load distribution, fluid flow efficiency, and aerodynamics are important.
Characteristics of Round Fiberglass Tubes:
- Uniform Strength Distribution: The circular shape allows for even distribution of stress, reducing weak points and preventing localized failures.
- High Torsional Strength: Round tubes resist twisting forces better than square tubes, making them ideal for applications involving rotational stress.
- Smooth Flow for Fluids and Air: The cylindrical shape minimizes friction and turbulence, making round tubes ideal for piping, ventilation, and fluid transport systems.
Advantages of Round Fiberglass Tubes:
- Corrosion Resistance: Unlike metal pipes, fiberglass does not rust or degrade in harsh environments.
- Lightweight Yet Strong: Offers a high strength-to-weight ratio, making transportation and installation easier.
- Durability in Harsh Environments: Withstands extreme weather, chemical exposure, and UV radiation, making it a long-lasting option for outdoor and marine use.
Common Applications of Round Fiberglass Tubes:
- Structural Supports: Used in bridges, marine docks, and utility poles due to their ability to handle high axial loads.
- Pipelines and Conduits: Ideal for water, chemical, and gas transportation due to their smooth internal surfaces and corrosion resistance.
- Aerospace and Automotive Components: Used in lightweight frames and aerodynamic structures where strength and flexibility are needed.
Square Fiberglass Tubes: Characteristics, Advantages, and Applications
Square fiberglass tubes offer superior stability, easy integration with flat surfaces, and high bending resistance. Their four-sided structure provides more contact area, making them suitable for applications that require strong joints and rigid frameworks.
Characteristics of Square Fiberglass Tubes:
- High Bending Resistance: Due to their shape, square tubes can withstand bending forces better than round tubes.
- Easy to Connect and Assemble: The flat surfaces make square tubes easier to bolt, weld, or bond to other structures.
- Efficient Use of Space: Unlike round tubes, square tubes fit neatly into cornered and compact spaces without leaving gaps.
Advantages of Square Fiberglass Tubes:
- Better Load Support for Frames: Ideal for industrial platforms, fences, and building frameworks.
- Improved Stability: The shape prevents rolling, making square tubes more stable in stationary applications.
- Aesthetic and Functional Design: Preferred in architectural and structural designs where uniformity and modern appearance matter.
Common Applications of Square Fiberglass Tubes:
- Construction and Infrastructure: Used in building frameworks, handrails, and support beams due to their structural integrity.
- Industrial Equipment Frames: Common in machine enclosures, workstations, and factory structures.
- Fencing and Barriers: Used in perimeter barriers, safety railings, and signposts for their rigid and stable nature.
Other Shapes of Fiberglass Tubes and Their Uses
Beyond round and square, other specialized shapes of fiberglass tubes exist for specific engineering and industrial applications. These unique shapes provide solutions to various challenges where standard designs are not suitable.
Rectangular Fiberglass Tubes:
- Stronger in One Direction: Offers high strength along the longer axis, making them useful for beams and bridges.
- Space-Efficient Design: Fits in narrow spaces better than round tubes.
Oval and Elliptical Fiberglass Tubes:
- Aerodynamic Efficiency: Used in wind energy, automotive, and aerospace applications where reducing drag is critical.
- Sleek and Lightweight: Preferred in sports equipment and specialized piping systems.
Triangular and Custom-Shaped Fiberglass Tubes:
- Specialized Engineering Needs: Often used in structural reinforcements, aerospace components, and high-tech applications.
- High Load Concentration Resistance: Can be designed for specific stress distribution requirements.
Large fiberglass tubes come in a variety of shapes, each with distinct structural, functional, and performance benefits. Round fiberglass tubes are ideal for fluid flow, high axial loads, and aerodynamic efficiency, while square fiberglass tubes excel in stability, bending resistance, and structural framing. Additionally, rectangular, oval, and custom-shaped fiberglass tubes offer unique advantages for specialized applications. The choice of shape depends on the specific needs of the project, balancing strength, weight, durability, and application efficiency to ensure optimal performance.
Manufacturing Processes Used in the Production of Large Fiberglass Tubes
The manufacturing process of large fiberglass tubes involves several key techniques, each contributing to the overall quality, strength, and durability of the final product. These processes are carefully chosen based on the intended application and performance requirements of the tube. In this section, we will explore the most commonly used manufacturing processes for large fiberglass tubes, focusing on how each process is applied and the advantages it offers. We will also highlight how each technique contributes to the properties that make fiberglass tubes ideal for industrial, commercial, and construction applications.
When it comes to producing large fiberglass tubes, several processes are employed depending on the size, strength, and specific features required. The choice of manufacturing process directly affects the structural integrity, finish, and overall performance of the final product. Below are the main methods used in the production of large fiberglass tubes.
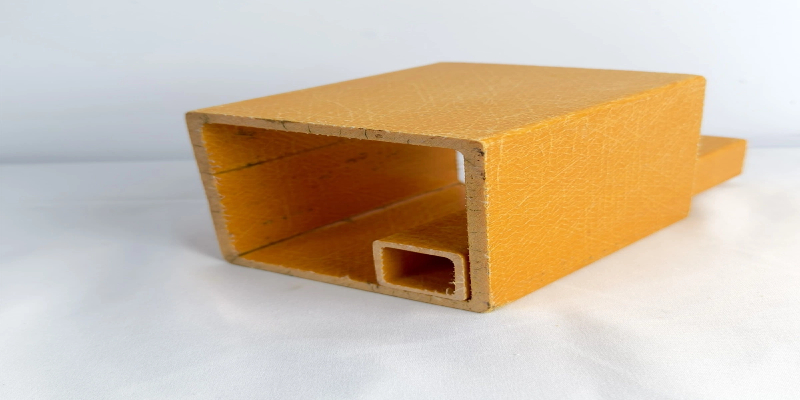
Filament Winding
One of the most common methods for producing large fiberglass tubes is filament winding. This process involves the continuous winding of resin-impregnated fiberglass filaments around a rotating mandrel. The mandrel is shaped according to the desired size of the tube, and the fiberglass filaments are wound in specific patterns to achieve the necessary strength and performance characteristics.
How It Works
In filament winding, the fiberglass filaments are first coated with a resin, typically polyester, vinyl ester, or epoxy, and then wound onto the mandrel in layers. These layers are built up at specific angles to ensure the tube can withstand internal pressures and external loads. Once the winding process is complete, the tube is cured in an oven or autoclave, hardening the resin and solidifying the structure.
Advantages
- This process allows for high precision in terms of tube dimensions and strength properties.
- Filament winding enables the production of large fiberglass tubes with consistent quality and uniform thickness.
- The process is ideal for producing tubes with high tensile strength, making them suitable for applications in high-stress environments.
Centrifugal Casting
Another method commonly used for large fiberglass tube production is centrifugal casting. In this process, a fiberglass pipe is created by pouring resin and chopped fiberglass into a rotating mold. The rotation forces the materials to evenly distribute along the inside walls of the mold, creating a uniform structure as the resin cures.
How It Works
The mold is spun at high speeds, causing the mixture of resin and fiberglass to be pushed outwards toward the mold walls. This centrifugal force ensures that the fiberglass is evenly distributed, forming a solid, dense pipe. Once the resin has cured, the mold is removed, and the fiberglass tube is finished.
Advantages
- Centrifugal casting produces fiberglass tubes with a smooth inner and outer surface, which is advantageous for fluid flow applications.
- This method is efficient for producing large-diameter tubes with consistent wall thickness and strength.
- It is ideal for manufacturing fiberglass tubes for environments requiring high corrosion resistance, such as those used in wastewater treatment and marine applications.
Pultrusion
Pultrusion is another specialized manufacturing process used to create large fiberglass tubes, particularly when precise and consistent dimensions are necessary. Unlike filament winding, pultrusion involves pulling continuous fibers through a resin bath and into a heated die, where the material is formed into the desired shape and cured.
How It Works
In pultrusion, continuous fibers, such as glass rovings, are saturated with resin and pulled through a heated die that shapes the material into a tube. The resin hardens in the die due to the heat, resulting in a solid, rigid tube with a consistent cross-sectional shape. The tube is then cut to the required length after exiting the die.
Advantages
- Pultrusion is excellent for producing large fiberglass tubes with high dimensional accuracy and consistency.
- The process allows for the integration of different fiber orientations, optimizing the tube for specific mechanical properties, such as strength and stiffness.
- Pultrusion is highly efficient, making it ideal for large-scale production of fiberglass tubes in standardized sizes.
Hand Layup
The hand layup process, while not as commonly used for mass production, is still employed for smaller runs or specialized applications where custom designs are required. In this method, layers of fiberglass mats or cloth are manually applied to a mold, and resin is poured or brushed onto each layer. The process is repeated to build up the desired tube thickness.
How It Works
A mold is prepared, and layers of fiberglass fabric or mat are applied by hand. Resin is then manually applied to each layer, and the composite structure is allowed to cure. Once cured, the mold is removed, and the fiberglass tube is inspected and finished.
Advantages
- Hand layup is highly versatile and allows for the creation of custom shapes and designs that may not be possible with other methods.
- It is often used for lower-volume production or prototypes.
- This method is ideal for applications requiring complex shapes or specialized resin systems that are not easily produced with other techniques.
Thermoforming
While less common for large fiberglass tubes, thermoforming is used in some cases to produce fiberglass tubes from pre-formed sheets or mats. This process involves heating fiberglass sheets to a pliable state and then shaping them around a mold.
How It Works
The fiberglass sheets are heated until they become soft and flexible. They are then draped over a mold, and pressure is applied to shape the material into a tube. Once the material cools and hardens, the mold is removed, and the tube is finished.
Advantages
- Thermoforming allows for the creation of fiberglass tubes with smooth surfaces and uniform thickness.
- It is suitable for certain applications where the fiberglass tube will be exposed to high temperatures or pressure.
The manufacturing process of large fiberglass tubes involves a variety of methods, each offering unique advantages depending on the application. Filament winding, centrifugal casting, and pultrusion are the most commonly used techniques for producing high-quality, durable, and high-strength fiberglass tubes, while methods like hand layup and thermoforming are more specialized, offering flexibility in design and custom requirements. Understanding these processes and their specific advantages allows manufacturers and engineers to select the most appropriate method based on the desired tube properties, ensuring that the finished product meets the rigorous demands of industrial, commercial, and construction applications.
FAQs about Large Fiberglass Tubes
Cutting fiberglass tubes requires careful preparation to ensure a smooth, clean cut. First, secure the tube using clamps or a vice to keep it stable. Use a marker or tape to mark your desired cutting line. For cutting, you can use a fine-toothed saw, such as a hacksaw or a circular saw with a diamond blade. Always wear safety equipment like goggles, a dust mask, and gloves to protect yourself from fiberglass dust and shards. If using a power tool, ensure it operates at a slower speed to minimize heat buildup and prevent the material from cracking. After cutting, smooth the edges with sandpaper or a file to avoid sharpness.
The best tools for cutting fiberglass tubes include a fine-toothed hacksaw, a circular saw with a diamond or carbide-tipped blade, or a jigsaw with a fine-tooth blade. For clean, precise cuts, using a diamond blade is ideal since it can handle the density of the fiberglass material without creating much heat. For smaller projects or DIY tasks, a handsaw with a high tooth count works well for a controlled cut. Power tools like a circular saw or jigsaw can be efficient for longer, straight cuts, but you must be cautious to avoid splintering. Always wear safety gear to protect against fiberglass dust.
To cut fiberglass without cracking, it’s essential to use the correct technique and tools. Begin by securing the fiberglass tube firmly in place with clamps or a vice to minimize movement. Mark the cut line clearly to guide your saw or cutting tool. Use a fine-toothed blade or a diamond blade, as these will produce smooth cuts and reduce the risk of cracking. Avoid using high-speed tools or applying excessive pressure, which can cause heat buildup and lead to the material cracking. It’s also helpful to score the fiberglass lightly before making the final cut to reduce stress on the material. Finally, always wear protective gear to avoid inhaling fiberglass dust.
Yes, you can cut fiberglass tubes with an angle grinder, but it requires caution. Using an angle grinder with a diamond or carbide-tipped blade works best for cutting through fiberglass. However, this method generates a lot of heat, which can cause the fiberglass to crack or splinter if not done carefully. To minimize this risk, use a slow, steady cutting motion and allow the tool to do the work without forcing it. Wear protective equipment, including a face shield, goggles, and gloves, since fiberglass dust can be hazardous to your health. If possible, cut in a well-ventilated area to avoid inhaling dust particles.
Cutting clear plastic tubes, including fiberglass tubes with plastic outer layers, is similar to cutting other types of plastic. Start by marking the cut line with a permanent marker or masking tape to ensure a clean and straight cut. Use a fine-toothed saw, such as a hacksaw or jigsaw with a fine blade, to avoid cracking. For smoother cuts, you can use a circular saw with a plastic cutting blade or a fine-toothed diamond blade. Make sure to secure the tube firmly to prevent movement, and always work slowly to avoid excess heat that could cause distortion or cracking. After cutting, use a file or sandpaper to smooth any rough edges.
Yes, a diamond blade is an excellent choice for cutting fiberglass tubes. Diamond blades are designed to handle tough materials, including fiberglass, without generating too much heat. This makes them ideal for clean cuts, especially when you’re using a power tool like a circular saw. When cutting fiberglass, the diamond blade’s abrasive surface effectively breaks through the fibers without causing cracks or splinters. However, make sure to use a lower-speed setting when cutting to avoid over-heating the material. Also, wear proper safety gear to protect against flying debris and dust.
Yes, fiberglass rebar can be cut with a hacksaw, though it requires a bit more effort compared to cutting standard rebar. To cut fiberglass rebar, use a fine-toothed hacksaw blade specifically designed for composite materials. Make sure to securely clamp the rebar in place to avoid movement while cutting. When cutting, go slowly and apply consistent pressure to ensure a clean cut without cracking the fiberglass. It may take a little longer to cut through compared to traditional steel rebar, but a hacksaw will still do the job. Always wear protective gloves and goggles to guard against fiberglass shards and dust.
To cut a fiberglass rod by hand, you’ll need a fine-toothed saw, such as a hacksaw or a small coping saw. Begin by measuring and marking the spot where you want to cut the rod. Secure the rod in a vice or clamp to prevent it from moving while you cut. If you use a hacksaw, choose a blade with fine teeth for a smoother cut. Apply slow, steady pressure while cutting to avoid generating too much heat, which can cause the fiberglass to crack. After the cut, smooth the edges with a file or sandpaper to eliminate sharpness. Remember to wear safety gear, including gloves and goggles, to protect yourself from fiberglass dust.
The best blade for cutting fiberglass tubes with a circular saw is a diamond blade or a carbide-tipped blade. These blades are designed to handle tough composite materials like fiberglass, providing clean cuts without causing excessive heat buildup. A diamond blade is particularly effective because it resists wear and tear, making it ideal for cutting through dense, fibrous materials. When using a circular saw, make sure to set the blade depth to just slightly more than the thickness of the fiberglass tube to reduce the chances of splintering or cracking. Always wear protective gear, including goggles and a dust mask, while cutting fiberglass.
Cutting corrugated fiberglass requires a bit more care than cutting flat fiberglass sheets due to the ridges. To begin, mark the cutting line clearly with a permanent marker or masking tape. Use a circular saw with a diamond or carbide-tipped blade, as these are ideal for cutting through the material. If using a jigsaw, ensure you have a fine-toothed blade to avoid damaging the fiberglass. Cut slowly and steadily to prevent cracking, and always cut along the ridges to avoid deforming the material. After cutting, use sandpaper or a file to smooth out any rough edges. Don’t forget to wear protective equipment to shield yourself from fiberglass dust and shards.
Large fiberglass tubes are used in a variety of industrial, construction, and hobby applications due to their unique properties. These tubes are lightweight yet strong, corrosion-resistant, and non-conductive, making them ideal for use in fluid power systems, structural reinforcement, and as protective casings for electrical cables. In the construction industry, large fiberglass tubes are often employed for applications such as scaffolding, columns, or piping. They are also used in environmental applications like water treatment systems and chemical transportation because of their resistance to corrosion. Additionally, fiberglass tubes are commonly utilized in manufacturing and transportation industries where durability, flexibility, and resistance to harsh environments are needed. Their ability to be custom-cut to specific sizes further enhances their versatility for both industrial and DIY projects.
Fiberglass pipes are known for their exceptional durability and long lifespan. When properly maintained, they can last between 50 to 75 years, depending on the environmental conditions and the type of application. The primary factors influencing the longevity of fiberglass pipes include exposure to UV light, chemicals, and extreme temperatures. Fiberglass is naturally resistant to corrosion, which helps it outperform traditional materials like steel or concrete pipes in many environments. For underground applications, fiberglass pipes are especially useful because they do not rust or degrade like metal pipes. Regular maintenance, such as cleaning and monitoring for physical damage, can further extend the lifespan of fiberglass pipes, making them a cost-effective choice for long-term projects.
Fiberglass pipes are incredibly strong for their weight, with high tensile and flexural strength. They can withstand significant internal pressure and are resistant to cracking and breaking, which makes them suitable for applications that require both strength and lightweight properties. The strength of a fiberglass pipe depends on the type of reinforcement used, typically glass fibers embedded in a resin matrix. Fiberglass pipes are designed to be lightweight yet durable, offering a strength-to-weight ratio that surpasses many metals. They can handle high-pressure environments, making them ideal for fluid transport systems, including water, oil, and gas pipelines. The combination of high strength and resistance to corrosion allows fiberglass pipes to maintain structural integrity in challenging conditions.
Fiberglass pipes are not insulation or foam themselves, but they are often used in insulation systems. Fiberglass pipe insulation is a common choice in industrial and commercial settings to reduce heat loss or prevent condensation. The fiberglass material used for pipe insulation is typically a combination of fiberglass matting or batt material that wraps around the pipe. This insulation helps control temperature and prevents freezing in cold climates. On the other hand, large fiberglass tubes are structural elements that are often used for applications such as fluid transportation and reinforcement, and may or may not require insulation depending on the specific needs of the project. Fiberglass can be used in both forms—either as structural tubes or as insulation, but the two are distinct in their applications.
Fiberglass is an excellent material choice due to its combination of strength, lightweight properties, and resistance to corrosion. Unlike metal pipes or tubes, fiberglass doesn’t rust or degrade in the presence of chemicals or moisture, which makes it perfect for use in harsh environments, including industrial, construction, and marine applications. It’s also non-conductive and non-magnetic, offering additional benefits for electrical and electronic applications. Fiberglass is easy to cut to size and install, reducing overall maintenance costs and ensuring longevity in most applications. Additionally, it’s highly customizable, allowing manufacturers to create fiberglass tubes in a wide variety of shapes and sizes for specific project requirements. Overall, using fiberglass ensures durability, low maintenance, and cost-effectiveness over time.
Fiberglass pipes are used in a broad range of industries due to their strength, resistance to corrosion, and versatility. They are commonly found in water and wastewater treatment plants, where they are used for transporting water, chemicals, and other fluids. Fiberglass pipes are also used in the oil and gas industry, especially for transporting corrosive substances or in offshore applications. Other common uses include industrial process systems, HVAC systems, and chemical processing plants. The construction industry also utilizes fiberglass pipes for drainage and stormwater management systems. Additionally, large fiberglass tubes are increasingly used in the transportation of fuels and chemicals, where their resistance to degradation from various chemicals makes them highly reliable. Their lightweight properties make them easier to install compared to traditional steel or concrete pipes, making them a cost-effective and durable solution.
The compressive strength of large fiberglass tubes varies depending on the specific composite material used, but it generally ranges from 250 to 600 MPa (megapascals). Fiberglass tubes are designed to handle significant compressive loads without cracking or buckling. The resin used in the fiberglass composite plays a critical role in determining its compressive strength, as does the arrangement of the glass fibers within the matrix. In most cases, the tubes are built to withstand high compressive forces while maintaining their lightweight nature, making them ideal for structural reinforcement applications. This compressive strength, combined with the material’s flexibility and durability, makes fiberglass tubes an excellent choice for applications requiring reliable performance under heavy loads or pressure.
The ultimate tensile strength of fiberglass varies depending on the fiber type, resin system, and manufacturing process. E-Glass fiberglass, the most common type used in large fiberglass tubes, has a tensile strength ranging from 30,000 to 50,000 psi. S-Glass, a higher-performance fiberglass material, offers an even greater tensile strength of around 100,000 psi. Fiberglass tubes designed for structural applications often use filament winding or pultrusion methods, which enhance their tensile properties by aligning fibers along the load-bearing axis. While fiberglass does not match the tensile strength of high-strength steels, its lightweight nature, corrosion resistance, and flexibility make it a preferred material in aerospace, marine, and construction applications. Unlike metal, fiberglass maintains its tensile properties even in corrosive environments, making it a long-lasting alternative to traditional materials in demanding industries.
Fiberglass pipes have a smooth internal surface, which provides excellent flow characteristics compared to metal pipes. The typical absolute roughness of fiberglass pipes ranges from 0.0002 to 0.005 inches (0.005 to 0.127 mm), depending on the manufacturing process and resin finish. This low roughness minimizes friction losses, allowing for efficient fluid flow with reduced turbulence and energy consumption. Compared to steel pipes, which have roughness values around 0.02 inches (0.5 mm) or more due to corrosion and scaling, fiberglass pipes maintain a consistently smooth surface over time. This feature makes fiberglass pipes ideal for applications in water treatment, chemical transport, and oil and gas pipelines, where high flow efficiency is crucial. Additionally, the non-corrosive nature of fiberglass ensures that roughness does not increase with age, unlike metal pipes, which degrade due to rust and deposits.
The thickness of large fiberglass pipes depends on their diameter, pressure rating, and application. Generally, fiberglass pipes range from 0.125 inches (3.2 mm) to over 1 inch (25 mm) thick. Pipes used for high-pressure systems, such as water transmission, chemical processing, and industrial piping, require thicker walls to withstand internal pressure and external loads. The thickness is often specified by standard classifications such as ASTM, ISO, and AWWA, ensuring that pipes meet structural and pressure requirements. For low-pressure applications, thinner fiberglass pipes are used to reduce weight and material costs while maintaining durability. The design thickness of a fiberglass pipe also accounts for corrosion resistance, impact strength, and environmental factors, ensuring longevity in harsh conditions. Engineers determine the required thickness based on fluid pressure, external forces, and safety factors, making fiberglass pipes versatile for different industrial and municipal applications.
Yes, large fiberglass tubes are strong in compression, but their strength varies based on the fiber orientation and resin system. The compressive strength of fiberglass typically ranges from 25,000 to 50,000 psi, which makes it capable of handling substantial loads. Pultruded fiberglass tubes, for example, have high axial compression strength, making them suitable for structural columns, supports, and load-bearing beams. Filament-wound fiberglass tubes provide excellent circumferential compression resistance, making them ideal for pipes and pressure vessels. While fiberglass is strong in compression, it does not outperform steel, which has a much higher compressive strength. However, fiberglass does not warp, corrode, or degrade under prolonged compression, making it highly durable for long-term structural applications. Engineers reinforce fiberglass tubes with additional layers or hybrid composites to enhance their load-bearing capabilities in applications where high compressive strength is required.
Fiberglass is not necessarily stronger than steel in absolute terms, but it has a higher strength-to-weight ratio. While steel has a tensile strength of approximately 50,000–100,000 psi, fiberglass typically ranges from 30,000–50,000 psi, depending on the type and resin system used. However, fiberglass is about 5 times lighter than steel, making it more efficient in applications where reducing weight is essential. In structural applications, pound for pound, fiberglass can outperform steel because it maintains strength while being much lighter and resistant to corrosion. Unlike steel, which rusts over time, fiberglass remains durable in harsh environments without the need for protective coatings. Additionally, fiberglass has better fatigue resistance and does not conduct electricity, making it a superior choice for utility poles, piping systems, and aerospace structures. However, for extreme load-bearing applications, steel still holds an advantage in compressive strength and hardness.
Yes, fiberglass is significantly stronger than standard plastic. Large fiberglass tubes outperform most conventional plastics in tensile strength, impact resistance, and durability. While plastics like PVC or polyethylene are lightweight and flexible, they lack the high strength-to-weight ratio that fiberglass provides. Fiberglass-reinforced plastic (FRP) combines fiberglass fibers with a resin matrix, creating a material that is much stronger and more rigid than pure plastic. This makes FRP an ideal choice for structural components, industrial applications, and high-performance tubing. Additionally, fiberglass has better heat and chemical resistance compared to most plastics, allowing it to function in extreme conditions where plastic would degrade. The added reinforcement of fiberglass fibers makes it superior for load-bearing applications, whereas plastic alone is more prone to cracking, warping, or breaking under heavy stress.
Fiberglass is highly durable and does not break easily under normal conditions. Large fiberglass tubes are designed to resist impact, stress, and environmental wear, making them suitable for heavy-duty applications. However, while fiberglass has excellent tensile and flexural strength, it can become brittle over time due to prolonged exposure to UV rays, extreme temperatures, or chemical degradation. Impact forces beyond its designed capacity can cause fractures or delamination, where the layers of fiberglass separate. In general, fiberglass is much more impact-resistant than glass or brittle plastics but less ductile than metals like steel. Proper reinforcement, such as adding additional layers or using advanced resin formulations, can enhance its durability. When correctly maintained and used within its structural limits, fiberglass remains a long-lasting, high-strength material for various applications, including structural supports, piping, and aerospace components.
Fiberglass and epoxy serve different purposes but complement each other in composite materials. Fiberglass itself is not stronger than epoxy in terms of sheer adhesive strength, but when combined, they create a highly durable and resilient structure. Epoxy is used as a bonding agent to hold fiberglass fibers together, enhancing the composite’s overall strength. While epoxy alone has excellent adhesion, hardness, and chemical resistance, it lacks the structural reinforcement that fiberglass provides. Large fiberglass tubes typically use epoxy resins to improve mechanical properties, increase impact resistance, and enhance load-bearing capabilities. The combination of epoxy and fiberglass results in a stronger, more flexible material than either component alone. When choosing between fiberglass and epoxy for structural applications, the combination of both materials in a composite form provides the best results for strength and durability.
Fiberglass can withstand tensile strengths of 30,000 to 50,000 psi, depending on the fiber composition, resin type, and tube construction. Large fiberglass tubes designed for high-pressure applications, such as piping systems or industrial supports, can withstand internal pressures exceeding 200 psi to 1000 psi or more. Filament-wound fiberglass tubes, reinforced with high-strength epoxy resins, offer higher pressure resistance and are used in environments where durability and lightweight properties are critical. The ability of fiberglass to withstand high psi levels makes it suitable for water and gas pipelines, structural beams, and aerospace applications. Unlike metal, fiberglass does not corrode or degrade when exposed to moisture and chemicals, maintaining its pressure resistance over long periods. However, impact damage or improper manufacturing can weaken the material, reducing its psi rating and requiring careful design and quality control.
Fiberglass mortar tubes, commonly used in fireworks displays and industrial applications, can last for many years if properly maintained. The longevity of these tubes depends on factors such as exposure to extreme temperatures, moisture, and physical wear. High-quality, well-constructed fiberglass mortar tubes can last 5 to 10 years or more under normal conditions. However, repeated exposure to heat and explosive forces can cause gradual degradation, leading to cracks or fiber delamination over time. Proper storage—keeping tubes dry, clean, and protected from UV exposure—can significantly extend their lifespan. Inspecting the tubes regularly for cracks, fraying, or internal wear is essential to ensure safety and performance. While fiberglass is highly durable and resistant to corrosion, impact damage from repeated use can weaken the structure over time, making periodic replacement necessary for high-stress applications.
The strongest type of fiberglass is typically S-Glass, which offers about 30% more tensile strength than traditional E-Glass fiberglass. S-Glass is used in high-performance applications such as aerospace, military, and advanced composite structures due to its superior mechanical properties, including higher impact resistance and greater stiffness. Filament-wound fiberglass tubes, reinforced with S-Glass fibers and epoxy resins, provide the highest strength and durability for structural applications. E-Glass, the most common type of fiberglass, is more affordable and offers good strength and corrosion resistance, making it ideal for general-purpose use in large fiberglass tubes. In addition, hybrid fiberglass composites, which incorporate carbon fiber or Kevlar, can significantly increase the tube’s strength while maintaining flexibility and durability. Choosing the right type of fiberglass depends on the application, with S-Glass and advanced composites being the best options for high-strength requirements.
Yes, large fiberglass tubes can hold significant weight, depending on their thickness, fiber orientation, and resin composition. Pultruded and filament-wound fiberglass tubes are commonly used in construction, aerospace, and industrial applications because of their high load-bearing capabilities. A properly designed fiberglass tube can support thousands of pounds without failure. For example, fiberglass structural beams and poles are used in bridges, power line supports, and heavy-duty scaffolding. Unlike metal, fiberglass does not bend or warp under sustained weight, making it reliable in long-term structural applications. However, excessive force beyond its designed load capacity can cause the material to crack or delaminate. Engineers consider factors such as wall thickness, diameter, and reinforcement to ensure that fiberglass tubes meet specific weight-bearing requirements. Overall, fiberglass offers an excellent combination of strength, durability, and weight support for demanding applications.
Fiberglass, including large fiberglass tubes, can be stronger than steel in certain aspects. While steel has a higher ultimate tensile strength (typically above 50,000 psi), fiberglass has a much better strength-to-weight ratio. Pound for pound, fiberglass can be stronger than steel because it provides excellent resistance to impact, bending, and corrosion while remaining much lighter. For example, fiberglass tubes used in structural applications can outperform steel by resisting environmental factors like rust and chemical exposure. Additionally, fiberglass is non-conductive and does not suffer from fatigue or thermal expansion issues like metal. However, steel still surpasses fiberglass in compressive strength and overall load-bearing capacity. The choice between fiberglass and steel depends on the application: if lightweight, corrosion resistance, and non-conductivity are priorities, fiberglass is superior. If extreme load-bearing and hardness are required, steel remains the preferred choice.
Large fiberglass tubes are known for their high strength-to-weight ratio. The strength of a fiberglass tube depends on its construction, resin type, and fiber orientation. Generally, fiberglass tubes have a tensile strength of around 30,000 to 50,000 psi, making them comparable to some metals. They are designed to withstand high loads without significant deformation or failure. Pultruded fiberglass tubes, commonly used in structural applications, offer superior axial strength, while filament-wound tubes provide excellent circumferential strength. These tubes can support significant weight while remaining lightweight, corrosion-resistant, and non-conductive. Their durability makes them suitable for industries such as aerospace, marine, construction, and utilities. While not as strong as carbon fiber, fiberglass tubes provide excellent impact resistance and longevity, especially in harsh environments where exposure to chemicals, moisture, and UV rays would degrade metal structures over time.
Fiberglass screens, including those used in large fiberglass tubes, can be cut using sharp utility knives, heavy-duty scissors, or specialized shears. For more precise or heavy-duty applications, a rotary tool with a cutting wheel or an oscillating multi-tool can be used. When working with large fiberglass tubes, cutting requires a different approach, such as using an angle grinder with a diamond blade or a carbide-tipped saw to ensure clean and even cuts. Always wear protective gear, including safety goggles, gloves, and a mask, to prevent irritation from fiberglass dust. Sanding the cut edges can help smooth rough surfaces, making the tube safer to handle and easier to assemble. Proper cutting techniques help maintain the tube’s structural integrity, preventing frayed or jagged edges that could weaken the material over time.
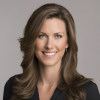
As the editor of GangLong Fiberglass, I have years of experience and in-depth research, focusing on cable tray products, fiberglass solutions, and grille systems. I incorporate years of industry insights and practical experience into every content, committed to promoting the progress of the industry. At GangLong Fiberglass, my commitment is reflected in every product, from innovative cable trays to durable fiberglass solutions and sturdy grille systems. As an authoritative voice in the industry, my goal is to provide valuable information to professionals and businesses and promote forward-looking solutions.