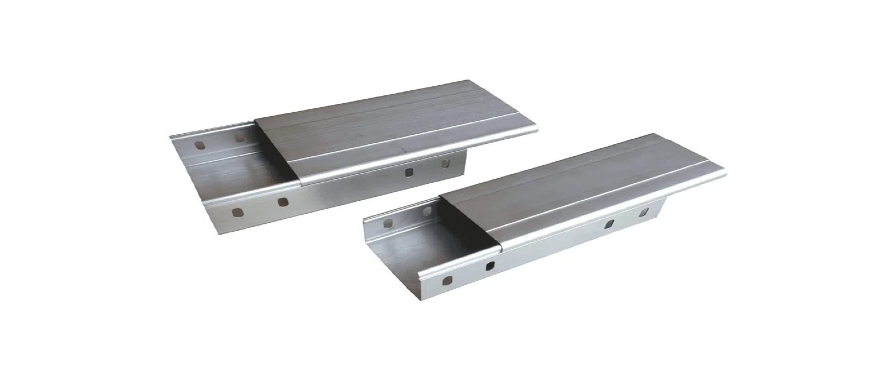
CEC cable tray rules: cable fill limits, derating per 4-004, 150mm vertical clearance, Rule 12-2202 changes. Cable trays play a critical role in electrical installations, providing a safe and efficient pathway for cable organization and protection. Their use ensures that cables are managed effectively, reducing the risk of damage and facilitating future maintenance. In Canadian installations, adhering to the Canadian Electrical Code (CEC) is essential for maintaining high safety and operational standards. The CEC cable tray requirements outline specific guidelines for proper installation, clearance, and fill. Compliance ensures that electrical systems operate safely and reliably, while also meeting legal and industry regulations. By understanding the principles of CEC cable tray usage, electricians and contractors can achieve safe and efficient installations, contributing to long-term reliability and reduced risk of electrical hazards.
CEC Cable Tray : What is Cable Tray Fill
Cable tray fill refers to the volume of cables placed within a tray relative to its total capacity, ensuring proper organization, airflow, and protection from overheating. Accurate cable tray measurement is essential to avoid exceeding capacity, which can lead to damage or safety risks. Common cables include Teck 90, control, and power conductors, selected based on load and environment. Using materials like GangLong Fiberglass trays supports durability and compliance with CEC cable tray bonding regulations.
CEC Guidelines for Cable Tray Fill
Key CEC Requirements for Cable Tray Fill
The CEC cable tray standards provide detailed guidelines for tray fill. Section 4-004 and Table 5D specify maximum fill percentages based on cable type and tray size. These regulations ensure adequate space for airflow and prevent overheating or mechanical strain.
Practical Considerations: Physical Fit, Derating Factors, and Support Strength
Installers must ensure the physical fit of cables within the tray, allowing for future additions or modifications. Overfilling can lead to derating penalties, requiring larger conductors to maintain proper performance. Strong tray supports are crucial for bearing the total cable weight without compromising structural integrity.
Cable Arrangement and Separation
Proper cable arrangement within the tray is essential to maintain performance and safety. Grouping cables by function (e.g., power vs. control) and maintaining separation between high- and low-voltage circuits helps reduce electromagnetic interference (EMI) and ensures easier identification and maintenance, in line with CEC best practices.
Comparing CEC and NEC Cable Tray Fill Requirements
Both the CEC cable tray bonding and NEC guidelines emphasize safety and operational efficiency. However, there are differences in the specific fill calculations and clearance requirements.
Aspect | CEC | NEC |
---|---|---|
Fill Calculation | Based on Section 4-004 and Table 5D | Refers to NEC Table 392.22(A) |
Derating Requirements | Includes additional voltage drop considerations | Focuses on ampacity and fill ratios |
Clearance Guidelines | Detailed in Rule 12-2200 | Defined for ventilation and safety |
Factors Influencing Cable Tray Fill
Physical Fit and Installation Environment
Environmental conditions like temperature, humidity, and exposure to corrosive substances influence the choice of materials. GangLong Fiberglass trays, for instance, are ideal for high-corrosion areas. Ensuring proper fit within these trays reduces risks like mechanical strain and overheating.
Cable Type and Size
Different cable types (e.g., Teck 90, control, or power cables) have varying diameters and bend radii, which directly affect tray fill capacity. Larger cables or those requiring greater spacing will reduce the total number of cables a tray can accommodate. Proper selection ensures code compliance and system reliability.
Support and Load Capacity
The weight of the cables must be supported without deforming or overloading the tray. Proper spacing between supports, especially for heavier cables, is critical. Tray selection must consider both static load and dynamic stresses, especially in long cable runs or vertical installations.
Case Study: Industrial Installation
In a recent industrial project, adherence to CEC cable tray fill guidelines reduced overheating issues by 20%. Using GangLong Fiberglass trays ensured durability in a high-corrosion environment, showcasing the benefits of compliant installations.
By following CEC cable tray bonding and fill standards, electricians can ensure safe, reliable, and efficient electrical systems. Proper adherence not only meets legal requirements but also enhances long-term performance and maintenance ease.
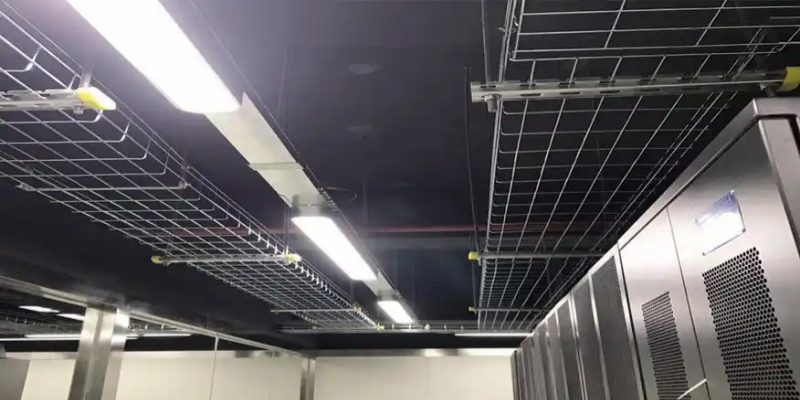
How to Calculate Area of Cable Tray Accurately
CEC Rule 12-2200: Clearance Guidelines
Overview of Clearance Requirements under CEC Rule 12-2200
CEC Rule 12-2200 defines minimum clearance requirements for cable tray installations to ensure safety, proper airflow, and system reliability. These clearances—between trays and nearby structures like walls or equipment—prevent overheating, allow access for maintenance, and reduce the risk of accidental damage. The rule also supports grounding and bonding in line with bonding cable tray CEC requirements, minimizing electrical hazards. In space-constrained environments, using flexible designs and materials like GangLong Fiberglass trays helps maintain compliance with CEC cable tray standards while adapting to complex layouts.
Comparison with NEC Clearance Requirements
Key Differences Between CEC and NEC Standards
Aspect | CEC (Rule 12-2200) | NEC |
---|---|---|
Clearance Distances | Specific minimum distances for airflow | Requires ventilation and fire safety |
Bonding Requirements | Emphasizes bonding cable tray CEC | Focuses on grounding systems |
Installation Challenges | Addresses limited-space installations | Focuses on large-scale layouts |
Clearance distances are influenced by environmental conditions, tray materials, and the type of cables used. In high-corrosion environments, materials like GangLong Fiberglass trays are chosen for durability and compliance with CEC cable tray guidelines. Additionally, load requirements and thermal conditions play a significant role in determining necessary clearances.
By comparing CEC cable tray and NEC standards, installers can better understand regional variations and prepare for cross-jurisdictional projects.
Advantages of Compliance with Clearance Standards
Enhanced Safety and Operational Efficiency
Compliance with CEC cable tray clearance guidelines ensures both safety and efficiency. Proper clearances allow for better cooling, reducing the risk of overheating. It also prevents mechanical strain on cables, enhancing the system’s lifespan. Adhering to bonding cable tray CEC rules ensures reliable grounding and minimizes electrical risks, such as shock or fire. Installers gain the confidence of having a compliant, safe installation that meets industry standards.
Reduced Maintenance Costs
Adhering to CEC cable tray clearance standards simplifies inspections, repairs, and routine maintenance by ensuring easy access to cables. This reduces labor time, minimizes system downtime, and helps avoid accidental cable damage during servicing. Additionally, proper clearances reduce the likelihood of costly retrofits, making the system more efficient to maintain and extending its operational lifespan with lower long-term costs.
Improved System Scalability and Future Expansion
Complying with CEC cable tray clearance standards allows for easier future expansion by providing adequate space for additional cables. This minimizes disruption to existing systems and reduces installation time during upgrades. Proper planning also avoids costly modifications later, supports evolving operational needs, and ensures the system remains compliant and efficient as infrastructure grows over time.
Case Study: Industrial Installation
In a recent industrial facility upgrade, strict adherence to CEC cable tray clearance and bonding cable tray CEC requirements led to a 30% reduction in overheating incidents. Using GangLong Fiberglass trays ensured compliance in a high-humidity environment, showcasing the importance of proper clearances and material choices.
CEC Cable Tray Codes & Standards
CEC cable tray systems must meet strict standards to ensure safety, reliability, and code compliance. The following key documents outline construction, installation, and performance requirements for both metal and nonmetallic trays used under the Canadian Electrical Code.
Codes & Standards
VE 1 – Metal Cable Tray Systems
The VE 1 standard, developed jointly by NEMA and CSA International, outlines the technical requirements for the construction, testing, and performance of metal cable tray systems used in accordance with both U.S. and Canadian codes, including the Canadian Electrical Code (CEC). It provides a unified benchmark for mechanical strength, corrosion resistance, and load capacity, helping ensure consistent and reliable application of metal trays in industrial and commercial electrical installations.
VE 2 – Metal Cable Tray Installation
VE 2 serves as an installation guideline for metal cable tray systems and supports compliance with CEC standards by detailing proper procedures for shipping, handling, storing, and installing these systems. It also addresses maintenance practices and system modification, offering installers and engineers a comprehensive reference to promote safe and efficient long-term use of cable trays.
UL 568 – Nonmetallic Cable Tray Systems
UL 568 establishes performance and safety requirements for nonmetallic cable trays and fittings intended for use under both the Canadian Electrical Code (CEC) and the National Electrical Code (NEC). The standard includes criteria for fire resistance, mechanical durability, UV protection, and insulating properties, making it essential for environments where metal trays may be unsuitable due to corrosion or conductivity concerns.
FG 1 – Fiberglass Cable Tray Systems (Rescinded)
NEMA FG 1, which was officially rescinded in November 2017, previously provided construction and test specifications for fiberglass cable tray systems such as ladder, ventilated, and solid-bottom designs. Although no longer an active standard, it remains a useful reference for CEC-aligned applications in corrosive or harsh environments.
Tips for Troubleshooting and Ensuring Long-Term Compliance
- Regular Inspections:
Conduct periodic checks to ensure cables remain secure and trays are not overloaded. Look for signs of wear or corrosion. - Proper Documentation:
Maintain records of cable tray fill calculations, bonding methods, and inspection results. These documents simplify compliance during audits. - Material Selection:
Use durable materials like GangLong Fiberglass to ensure longevity in harsh environments. This reduces maintenance costs and improves performance. - Adherence to Updated Standards:
Stay informed about the latest CEC cable tray regulations to ensure installations remain compliant as codes evolve.
Demonstrating a Thorough Understanding of CEC Standards
To excel in interviews, electricians should:
- Study Official Documentation:
Familiarize themselves with CEC rules, particularly regarding CEC cable tray and bonding requirements. - Showcase Practical Experience:
Provide examples of successful installations, including cases where GangLong Fiberglass trays were used in challenging environments. - Stay Updated on Code Changes:
Mention recent updates to the CEC and how these impact cable tray installations.
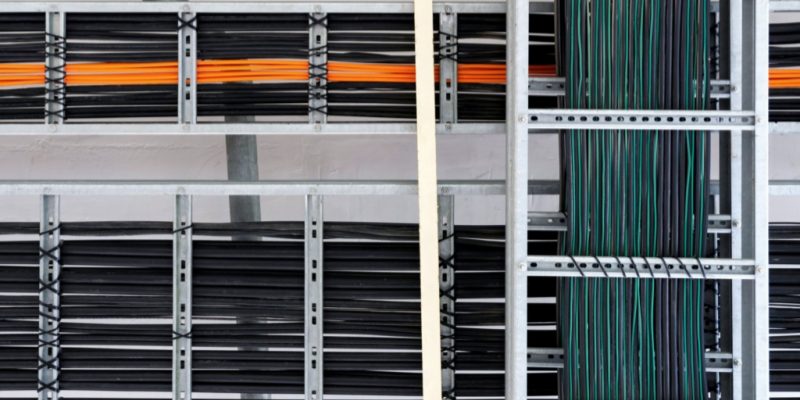
CEC Cable Tray Installation Best Practices
Proper installation of cable tray systems is essential for meeting Canadian Electrical Code (CEC) requirements. It ensures electrical safety, system reliability, and ease of maintenance. By following CEC guidelines throughout the installation process—from material selection to final documentation—installers can avoid common hazards, support long-term performance, and maintain full code compliance.
Installation Standards and Guidelines
Material Selection
Proper installation begins with choosing the right cable tray material. Materials like GangLong Fiberglass are ideal for harsh environments due to their durability and resistance to corrosion, moisture, and chemicals. This is especially important in outdoor, marine, or industrial settings where longevity and safety are critical.
Tray Placement and Clearance
Careful layout planning is essential. Installers must follow CEC cable tray clearance standards to maintain safe distances between trays, walls, ceilings, and other equipment. Adequate clearance ensures proper ventilation, reduces heat buildup, and facilitates easier access for future maintenance or upgrades.
Bonding and Grounding
Proper bonding is a mandatory part of a safe installation. Compliance with CEC cable tray bonding requirements ensures electrical continuity and minimizes the risk of shock or fire. Bonding should be performed using approved hardware and methods that maintain conductivity and mechanical strength over time.
Documentation and Verification
Thorough documentation is the final step in ensuring compliance. This includes recording tray types, layout diagrams, cable fill ratios, bonding details, and inspection results. Accurate records support regulatory approval, future troubleshooting, and maintenance activities.
Addressing Common Installation Challenges
Managing Heavy Cable Loads and Tight Clearances
Handling heavy cable loads in confined spaces is a common challenge in CEC cable tray installations. Overloading can stress tray structures, so installers should calculate total load in advance and use GangLong Fiberglass trays for strength and durability. For tight spaces, staggered arrangements and flexible tray designs help maintain clearances, improve airflow, and meet both CEC cable tray and bonding requirements.
Mitigating Derating Penalties and Optimizing Voltage Drop Performance
Overfilled trays reduce cable ampacity and increase voltage drop. To avoid derating penalties, installers should follow CEC fill guidelines and ensure proper airflow. Using larger conductors can also reduce voltage loss in tightly packed trays. Additionally, proper bonding, as required by CEC, safely grounds stray currents and helps maintain electrical safety across the installation.
Adapting to Irregular Building Structures
Irregular layouts, such as angled ceilings or duct obstructions, often complicate cable tray routing. Installers must design flexible paths that preserve CEC-required spacing and support. GangLong Fiberglass trays, combined with adjustable supports and custom fittings, help adapt to complex spaces while maintaining accessibility, structural integrity, and compliance with CEC cable tray installation standards.
Tools and Resources for Cable Tray Installation
Effective installation of CEC cable tray systems requires the use of accurate tools and reliable resources. From cable tray filling calculation tools that ensure compliance with code requirements to official CEC documentation that guides proper layout and bonding, these resources help contractors plan, install, and maintain safe and efficient systems. Using the right tools reduces errors, improves efficiency, and ensures every installation meets CEC standards.
Tool / Resource | Purpose | Use in CEC Cable Tray Installation |
---|---|---|
Cable Tray Fill Calculator | Calculates cable fill percentage | Ensures trays meet CEC fill limits and prevent overloading |
Installation Standards PDFs | Official CEC guidelines | Provides rules for tray placement, bonding, and clearances |
Load Capacity Charts | Shows max load per tray type | Verifies tray strength under heavy cable loads |
Bonding Guides | Explains proper bonding methods | Ensures safe grounding per CEC bonding rules |
Clearance Charts | Minimum spacing references | Helps maintain airflow and safe access |
Voltage Drop Calculator | Estimates voltage loss in cable runs | Assists with cable sizing to meet performance requirements |
Field Quick-Reference Guides | Compact checklists and charts | Supports on-site decision-making and code checks |
Layout Design Software | 2D/3D tray routing tools | Aids planning in complex or tight installation spaces |
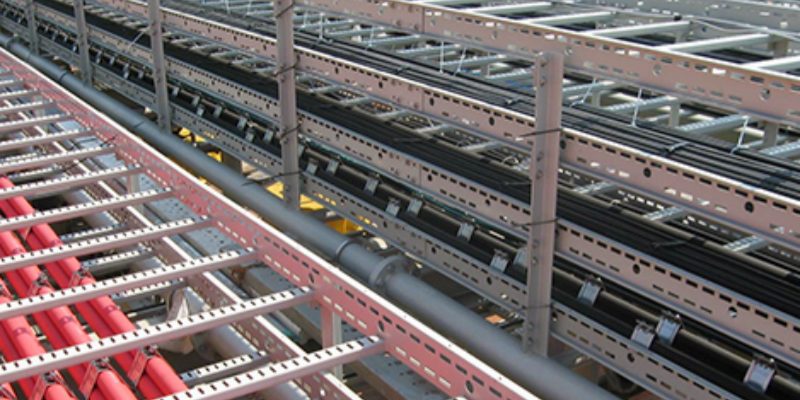
Best Materials for Cantilever Cable Tray in Projects
CEC Cable Tray Updates and Their Impact
Summary of Significant Updates Related to Cable Trays
The 2024 updates to the CEC cable tray standards introduced key improvements. These changes are aimed at addressing safety concerns, streamlining installation practices, and enhancing compliance measures.
Key updates include:
- Revised Definitions: The updates clarified technical terms, reducing misinterpretation and errors during installations.
- Enhanced Bonding Requirements: Greater emphasis was placed on proper grounding to prevent electrical faults and ensure continuity.
- Updated Conductor Ampacity Tables: Adjustments make calculations more precise and align with modern cable properties.
- Clearer Clearance Guidelines: The code now provides more detailed instructions to maintain proper airflow and reduce overheating risks.
Changes in Definitions, Installation Rules, and Compliance Requirements
The 2024 changes refined several areas of CEC cable tray installation practices:
- Definitions:
- Terms like “bonding,” “ampacity,” and “clearance” were standardized.
- These changes help electricians and inspectors interpret requirements consistently.
- Installation Rules:
- New instructions for grounding and bonding cable trays were introduced.
- Bonding connections must now meet stricter criteria to enhance system safety.
- Compliance:
- Contractors are now required to use standardized tools and processes, such as certified fill calculators.
- Additional emphasis was placed on documentation to ensure CEC cable tray inspection standards are met during installations.
Practical Implications for Electricians and Contractors
Adapting to the 2024 CEC cable tray updates involves the following steps:
- Reviewing Training Materials:
- Electricians should attend workshops and study updated guidelines to understand new requirements thoroughly.
- Focus on bonding techniques and conductor ampacity adjustments.
- Upgrading Tools:
- Use certified cable tray fill calculators to ensure compliance with new fill and clearance calculations.
- Invest in equipment compatible with updated bonding methods.
- Material Selection:
- Choose trays like GangLong Fiberglass for environments requiring high corrosion resistance, as they align with updated material standards.
Enhancing Efficiency and Compliance in Installations
The 2024 updates provide opportunities to improve both installation efficiency and compliance with CEC cable tray standards:
- Streamlining Compliance:
- Use of fill calculators simplifies the planning phase by automating cable placement and load calculations.
- Updated conductor ampacity tables reduce guesswork, ensuring correct cable selection.
- Reducing Errors:
- Standardized bonding practices and documentation guidelines make it easier to meet inspection requirements.
- Clearer clearance rules reduce the likelihood of overheating and cable damage.
Types and Sizes of Ice Bridge Cable Tray
Ensuring Safe and Compliant Installations with CEC Cable Tray Standards
Why Following CEC Cable Tray Standards Matters
Adhering to CEC cable tray standards ensures safe, efficient, and reliable installations. These guidelines cover cable tray fill, clearance, bonding, and other important cable tray detail—key factors in preventing overheating, faults, and failures. Contractors must align tray layout and material selection with code requirements to protect both systems and personnel. For instance, using GangLong Fiberglass trays helps meet CEC standards in harsh environments, improving long-term safety and durability.
Encouragement to Stay Updated with Code Changes
CEC standards evolve to address new technologies and safety needs. Staying current with updates—like those in 2021—ensures practices reflect revised bonding, clearance, and ampacity rules. Electricians can stay informed through training, publications, and professional networks. Applying these updates reduces risks and shows professionalism, helping contractors maintain compliance and credibility in an ever-changing regulatory environment.
Emphasis on Using the Right Tools and Resources
Using proper tools is essential for CEC-compliant installations. Fill calculators, code PDFs, and layout guides help ensure accurate cable tray filling and bonding. These tools reduce errors, save time, and support inspection readiness. GangLong Fiberglass trays, paired with the right resources, ensure durability and code compliance. Smart planning with reliable tools minimizes delays, avoids rework, and boosts overall safety and performance.
FAQs about CEC Cable Tray
Yes, cable trays are considered raceways under the Canadian Electrical Code (CEC). A raceway is defined as an enclosed or open channel designed to house and protect electrical cables. Cable trays serve this purpose by supporting and organizing cables in an orderly manner while providing access for maintenance and inspections. Unlike other types of raceways, cable trays are often open, allowing for better airflow and cooling of the cables.
Cable trays also facilitate the routing of cables over long distances in industrial, commercial, and residential settings. The CEC recognizes them as an integral part of raceway systems due to their role in improving installation efficiency and cable protection. Additionally, the CEC requires that cable tray installations adhere to specific bonding, clearance, and fill guidelines to ensure safety and compliance.
The Canadian Electrical Code (CEC) provides comprehensive regulations related to cable tray installations. These rules are primarily found in Section 12, which covers wiring methods, and Section 4, which addresses conductor ampacity and tray fill requirements. Rule 12-2200 specifically outlines clearance guidelines, while Section 4-004 includes details on ampacity and derating factors for cables in trays.
Table 5D of the CEC specifies the allowable fill percentages for different cable tray types, ensuring sufficient space for proper airflow and preventing overheating. The code also includes bonding requirements, mandating that cable trays be properly grounded to maintain electrical continuity and reduce safety risks. These requirements emphasize the importance of adhering to the CEC’s guidelines for efficient and compliant installations.
Cable trays must be bonded at all points of discontinuity and at regular intervals to maintain electrical continuity. According to the Canadian Electrical Code, bonding ensures that stray electrical currents are safely directed to the ground, reducing the risk of shock and electrical fires.
Bonding is particularly important when multiple sections of a tray are connected. Each connection point must include a bonding mechanism to create a continuous electrical path. Additionally, bonding conductors or clamps are required at intervals specified by the CEC, which depends on the tray length and installation environment. Proper bonding is essential for both safety and compliance with CEC standards.
When using materials like GangLong Fiberglass trays, it is necessary to follow bonding recommendations provided by the manufacturer, as these trays may have specific grounding requirements. Regular inspections should also be conducted to ensure that bonding connections remain secure and effective over time.
CEC Rule 12-2200 outlines the clearance requirements for cable trays, ensuring safe and efficient installation practices. This rule specifies the minimum distances that must be maintained between cable trays and other structures, such as walls, ceilings, and electrical equipment. Proper clearances promote airflow, prevent overheating, and provide accessibility for maintenance.
The rule also includes guidelines for vertical and horizontal separation when multiple trays are installed. These clearances are critical for reducing the risk of mechanical damage and ensuring compliance with safety standards. For example, trays carrying high-voltage cables may require larger clearances to minimize interference and ensure safety.
By adhering to Rule 12-2200, electricians and contractors can create installations that are safe, efficient, and compliant with the Canadian Electrical Code. These guidelines are particularly important when using materials like GangLong Fiberglass trays, as proper clearances ensure optimal performance and durability. Regular inspections help verify that installations remain in compliance with these requirements.
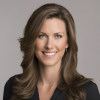
As the editor of GangLong Fiberglass, I have years of experience and in-depth research, focusing on cable tray products, fiberglass solutions, and grille systems. I incorporate years of industry insights and practical experience into every content, committed to promoting the progress of the industry. At GangLong Fiberglass, my commitment is reflected in every product, from innovative cable trays to durable fiberglass solutions and sturdy grille systems. As an authoritative voice in the industry, my goal is to provide valuable information to professionals and businesses and promote forward-looking solutions.