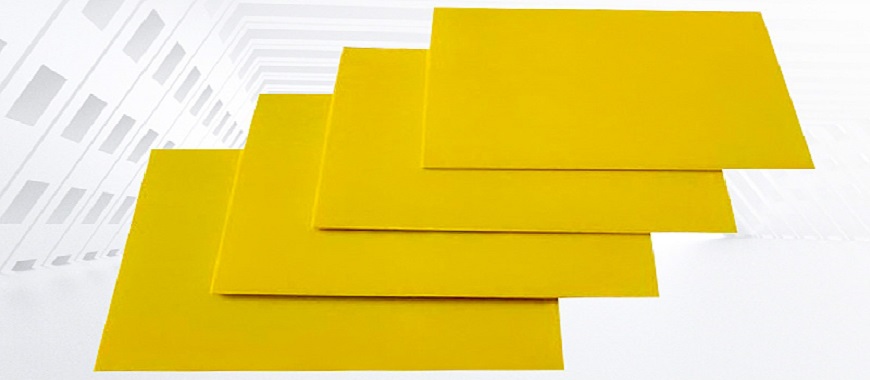
Fire retardant FRP (Fiberglass Reinforced Plastic) is a crucial material in modern construction. Fire Retardant FRP offers superior flame resistance and stability, ensuring safety in commercial and industrial applications with high fire ratings. FRP is widely used for its strength, lightweight nature, and resistance to various environmental factors. The addition of fire-retardant properties enhances its safety in buildings, particularly in areas where fire risks are high. Fire retardant FRP reduces the spread of flames and smoke, protecting both structures and occupants. Regulations, like those in New York City, emphasize the need for materials with low smoke toxicity and good fire performance. This makes fire retardant FRP an essential component in construction projects, ensuring compliance with safety standards and improving overall fire safety.
What Is Fire Retardant FRP Fire Resistance Period
The fire resistance period of a material refers to the amount of time it can withstand exposure to fire before failing structurally. For fire retardant FRP, such as fiberglass reinforced resin panels, this period is influenced by the type of resin and reinforcements used in the composite. While fiberglass itself does not burn, the resins that bind it can combust under high heat. Therefore, the fire resistance of fire retardant FRP depends heavily on the flame-retardant properties of the resin. Specialized fire-retardant resins can slow the spread of fire but still require external conditions, such as the absence of an external flame source, to be fully effective.
Key Elements of FRP Fire Rating
- Flame Spread Index (FSI):
This measures how quickly a flame spreads across the surface of the material. Materials with a low FSI are more effective in preventing rapid flame spread. FRP materials are generally tested using standards like ASTM E84 (Standard Test Method for Surface Burning Characteristics of Building Materials).- Class A: FSI of 0-25 (best performance in preventing flame spread).
- Class B: FSI of 26-75.
- Class C: FSI of 76-200 (indicates poorer flame spread resistance).
- Smoke Developed Index (SDI):
This measures the amount of smoke produced by the material during exposure to fire. High smoke production can hinder evacuation, reduce visibility, and pose significant health risks. The lower the SDI, the safer the material in terms of smoke release.- Class A: SDI of 0-450.
- Class B: SDI of 451-750.
- Class C: SDI of 751-1000.
- Structural Integrity:
This aspect assesses how well the FRP maintains its structural properties, such as strength and stiffness, when exposed to fire. The ability of FRP to retain its integrity during a fire ensures that the building or structure can withstand the fire for a longer period, facilitating safe evacuation and firefighting.
Factors Affecting Fire Retardant FRP Performance
Several factors affect the fire resistance of fire retardant FRP. One of the main factors is the type of resin used. Thermoset resins, commonly used in FRP, can be made more resistant to fire by incorporating fire-retardant additives. The thickness of the FRP composite also influences the fire resistance period. Thicker panels or ducts provide longer protection, but the fire-retardant properties of the resin remain critical in determining how long the material can resist fire. Lastly, the presence of external flames or heat sources significantly impacts the effectiveness of fire retardant FRP in fire situations.
Fire Retardant Fiber Reinforced Polymer (FRP) materials are widely used in various industries for their excellent strength-to-weight ratio, durability, and corrosion resistance. However, when it comes to fire safety, their performance can be influenced by various factors. Below is a detailed description of the key factors that affect the fire retardant performance of FRP materials:
Material Composition
The chemical composition of FRP materials plays a significant role in their fire retardant properties. FRPs are typically made of a polymer matrix and reinforcing fibers, with the matrix being the most crucial component when it comes to fire resistance. A higher proportion of fire-retardant additives or flame-retardant resins, such as epoxy or vinyl ester resins, enhances the material’s ability to resist ignition and slow down fire propagation.
Type of Fiber Reinforcement
The type of fibers used in the reinforcement of FRP materials can impact fire retardant performance. Common fibers include glass, carbon, and aramid. Glass fibers are generally more fire-resistant compared to carbon or aramid fibers, making them a better choice for fire-retardant FRPs. The specific characteristics of the fibers, such as melting point, strength, and their interaction with the matrix material, can influence the overall fire resistance of the composite.
Fire Retardant Additives
The inclusion of fire retardant additives, such as aluminum hydroxide, magnesium hydroxide, and brominated compounds, can significantly improve the fire-resistant properties of FRP. These additives work by releasing water or non-combustible gases when exposed to heat, thereby cooling the material and limiting the spread of flames. The concentration and uniformity of these additives throughout the material are crucial for consistent fire performance.
Thickness of the FRP Material
The thickness of the FRP material directly influences its fire retardant performance. Thicker materials provide greater insulation and resistance to heat penetration, thus improving fire performance. However, this can also increase the weight and cost of the material. Therefore, a balance must be struck between material thickness and desired fire performance.
Exposure Conditions
The conditions under which the FRP material is exposed to fire are important factors affecting its performance. Factors like the intensity of heat, duration of exposure, and the presence of additional combustible materials can all affect how well the FRP resists fire. For example, direct flame contact will result in different outcomes than exposure to radiant heat. FRPs exposed to long-term heat may degrade over time, reducing their fire resistance.
The fire retardant performance of FRP materials depends on a variety of factors, including material composition, type of fibers, fire retardant additives, and exposure conditions. Proper design, manufacturing, and maintenance of FRPs can significantly enhance their fire safety capabilities.
FRP Fire Rating and Its Importance
The fire rating of FRP materials is extremely important for several reasons:
Safety Compliance
Building codes and fire safety regulations often mandate the use of fire-rated materials in specific areas. For example, Class A fire-rated FRP materials are required in public buildings, high-rise structures, and industrial facilities where fire safety is a high priority. Using materials with the proper fire rating ensures compliance with local fire safety codes and helps avoid legal and safety risks.
Fire Resistance
The primary purpose of fire-rated FRP materials is to enhance the fire resistance of a building or structure. Materials with higher fire ratings (such as Class A) significantly reduce the likelihood of a fire spreading quickly, giving more time for occupants to evacuate safely and for firefighters to control the blaze. By preventing or delaying fire propagation, fire-rated FRPs protect both lives and property.
Smoke Control
Alongside flame spread, the amount of smoke produced by materials in the event of a fire is critical for safety. Materials with lower Smoke Developed Indices (SDI) release less smoke, improving visibility and air quality in evacuation paths. This makes it easier for individuals to navigate and find exits during an emergency.
Durability and Performance
FRP materials with high fire ratings tend to be more durable and perform better under extreme heat conditions. This ensures that the material will not break down quickly or degrade during a fire, preserving the integrity of the structure. The durability of fire-rated FRPs is especially important in environments where exposure to heat or fire is likely, such as industrial plants or transportation systems.
Insurance and Liability
Buildings constructed with fire-rated materials may receive lower insurance premiums due to the reduced fire risk. On the other hand, failure to meet fire safety standards can lead to higher premiums or even denial of coverage. Fire-rated FRPs help mitigate risks, reducing the potential for catastrophic losses and liability in case of a fire.
The fire rating of FRP materials plays a crucial role in ensuring safety, compliance, and durability in fire-prone environments. A higher fire rating (such as Class A) offers better flame spread resistance, smoke control, and structural integrity, making it essential for public buildings, industrial facilities, and any application where fire safety is a primary concern. When selecting FRP materials, it is important to assess the fire rating to ensure that the material meets the required safety standards and provides the necessary protection in the event of a fire.
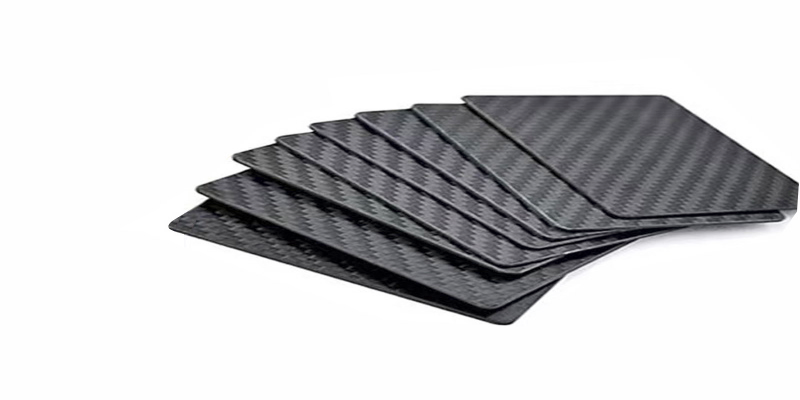
Best Deals on Fiberglass Mortar Tubes Sale for Fireworks
Comparing FRP Class A vs Class C Fire Ratings
Fire Retardant Fiber Reinforced Polymer (FRP) materials are often classified based on their fire performance. The two common classifications are Class A and Class C fire ratings. These ratings are determined according to specific fire testing standards and represent different levels of fire resistance. Here’s a detailed comparison of Class A vs. Class C fire ratings:
Fire Resistance Performance
- Class A Fire Rating:
- A Class A fire rating indicates the highest level of fire resistance for building materials. FRP materials that meet this rating are considered to have low flame spread and low smoke generation. They are designed to prevent fire from spreading rapidly, which is essential in areas where fire safety is critical, such as public buildings, industrial facilities, and high-rise structures.
- Flame Spread Index (FSI): Class A materials have an FSI of 0 to 25 (lower is better).
- Smoke Developed Index (SDI): Class A materials have an SDI of 0 to 450 (lower is better).
- Class C Fire Rating:
- A Class C fire rating indicates a lower level of fire resistance compared to Class A. These materials are generally suitable for areas where fire safety requirements are less stringent, but they still offer some protection against fire. Class C-rated FRP materials tend to have a higher flame spread and higher smoke generation compared to Class A.
- Flame Spread Index (FSI): Class C materials have an FSI of 76 to 200.
- Smoke Developed Index (SDI): Class C materials have an SDI of 451 to 700.
Applications
- Class A Fire Rating:
- Commercial and public spaces: These materials are commonly used in environments that require strict fire safety standards. For example, airports, hospitals, schools, shopping malls, and office buildings.
- Fire-sensitive environments: Industrial facilities where high heat or the potential for fire spread is a concern often require Class A materials to ensure maximum safety.
- Class C Fire Rating:
- Residential and less critical environments: Class C-rated materials may be used in less fire-sensitive environments like residential buildings or non-critical areas of commercial facilities.
- Non-public spaces: They can also be found in warehouses, garages, and certain industrial applications where the likelihood of fire spread is less of a concern.
Flame Spread and Smoke Development
- Class A Fire Rating:
- Class A materials exhibit minimal flame spread and low smoke production, helping to maintain visibility and prevent rapid fire propagation. This is especially crucial in evacuation scenarios, where individuals need to move to safety quickly.
- Class C Fire Rating:
- Class C materials tend to have a higher flame spread, which means that the fire can spread more rapidly. Additionally, these materials can generate more smoke, which can limit visibility and pose health risks during a fire emergency.
Regulatory Compliance
- Class A Fire Rating:
- Materials with a Class A fire rating are often required by building codes and fire safety regulations for certain types of buildings. Compliance with these regulations ensures that the structure meets high fire safety standards.
- Class C Fire Rating:
- Class C-rated materials may not meet the fire safety codes for buildings that require strict fire-resistant materials. However, they are still compliant with less stringent fire safety regulations for specific applications.
Cost and Availability
- Class A Fire Rating:
- Higher cost: Class A-rated FRP materials are more expensive due to the additional fire-retardant additives and rigorous manufacturing processes required to meet these high standards.
- These materials may be harder to source, depending on the region and supplier, due to their specific fire resistance requirements.
- Class C Fire Rating:
- Lower cost: Class C-rated FRP materials are generally less expensive compared to Class A. They require fewer fire-retardant additives and less complex manufacturing processes.
- More widely available in various markets, particularly for less demanding applications.
Performance in Fire Conditions
- Class A Fire Rating:
- Superior protection: These materials offer superior protection against fire, maintaining structural integrity and resisting combustion for longer periods. Class A-rated FRPs are designed to limit the spread of fire and minimize smoke production, giving more time for evacuation and firefighting efforts.
- Class C Fire Rating:
- Lower resistance: In the event of a fire, Class C materials offer lower protection. They may burn more quickly and produce more smoke, leading to faster fire spread and greater health risks from smoke inhalation.
7. Maintenance and Durability
- Class A Fire Rating:
- Materials with a Class A fire rating tend to be more durable and require less frequent maintenance due to their higher resistance to heat and flames.
- Class C Fire Rating:
- Class C-rated FRPs may degrade faster over time and require more frequent maintenance, especially if exposed to extreme conditions or if they start to show signs of wear and tear.
The main difference between Class A and Class C fire ratings lies in the material’s performance in terms of flame spread, smoke development, and overall fire resistance. Class A offers the highest level of fire safety, making it suitable for high-risk, public, and commercial applications. Class C, on the other hand, is appropriate for less critical environments where fire safety is still important but not as stringent. Understanding the specific fire safety requirements of the application is key to choosing the right fire retardant FRP material.
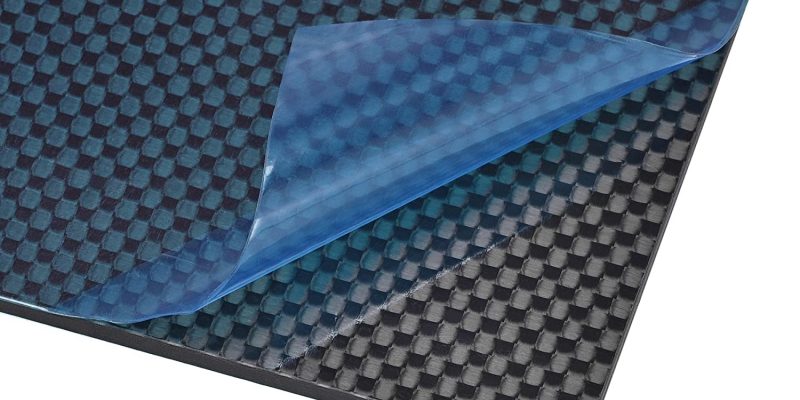
The Characteristics of Class C Fire Retardant FRP
Class C fire retardant FRP is designed to provide basic fire protection, but it does come with limitations. One of its key characteristics is its lower flame spread rating compared to Class A. It is more cost-effective and easier to install, making it a good option for less demanding applications. However, Class C fire retardant FRP does not perform as well in environments where fire safety is a priority.
Limitations of Class C FRP in Fire Performance
The main limitation of Class C fire retardant FRP is its lower resistance to fire and smoke compared to Class A materials. In high-risk environments, relying on Class C FRP can present significant safety concerns. Its higher flame spread rate means that fires can move more quickly through areas using Class C materials. Moreover, the smoke generated can lead to reduced visibility and increased danger for people in the vicinity. These factors make Class C fire retardant FRP unsuitable for areas that demand top-tier fire safety.
Key Applications of FRP Panels in Fire-Resistant Construction
FRP panels play a crucial role in fire-resistant construction, offering a combination of strength, durability, and fire protection. While fiberglass flammable by nature, fire retardant FRP panels are specifically designed to withstand exposure to flames and extreme heat, providing an extra layer of safety in critical structures. These panels are often used in walls, ceilings, and partitions where fire resistance is required by building codes.
Improving Fire Performance with Fire-Retardant Additives
To enhance the fire resistance of FRP panels, fire-retardant additives are commonly used. These additives slow down the combustion process, reduce smoke generation, and limit flame spread. Fire retardant FRP panels that incorporate these additives provide better protection in high-risk environments like hospitals, airports, and commercial buildings. By improving the fire performance of FRP panels, they become an essential component in fire-resistant construction.
Industries Where Fire Retardant FRP Panels Are Essential
Fire retardant FRP panels are essential in industries where fire safety is critical. In the electronics industry, for example, smoke and flame control is crucial to prevent damage to sensitive equipment. Chemical plants also rely on these panels to contain potential fires and reduce the spread of hazardous materials. FRP panels are also widely used in public infrastructure, such as transportation hubs and data centers, where fire safety regulations are stringent. The ability of fire retardant FRP to resist flames and limit smoke makes it invaluable in these settings.
Factors Influencing Fire Retardant FRP Thickness and Fire Safety
The thickness of fire retardant FRP panels plays a significant role in determining their fire resistance. Thicker panels provide better insulation, allowing them to withstand heat for a longer period. This is especially important in environments where fire exposure is a serious risk. The relationship between fire retardant FRP thickness and fire safety is directly linked to the material’s ability to slow down flame spread and protect the structural integrity of buildings.
How Thickness Impacts Fire Rating Classifications
The thickness of fire retardant FRP can significantly influence its fire rating classification. Thicker panels tend to have a lower flame spread rating, meaning they are more resistant to fire and smoke. For example, FRP panels that are classified as Class A often have greater thickness, enabling them to resist flames more effectively compared to thinner Class C panels. Selecting the correct thickness is crucial when planning for fire safety, especially in buildings with strict fire codes.
Recommendations for Selecting FRP Thickness for Fire Resistance
When selecting fire retardant FRP, choosing the right thickness for your specific fire-resistance requirements is critical. In high-risk environments, like industrial or chemical plants, it is advisable to opt for thicker FRP panels, including those used for FRP wall protection, as they offer enhanced fire resistance. For lower-risk settings, such as residential buildings, thinner panels may be suitable. Consulting with fire safety experts or engineers can ensure that the chosen thickness meets both safety regulations and practical fire-resistance needs.
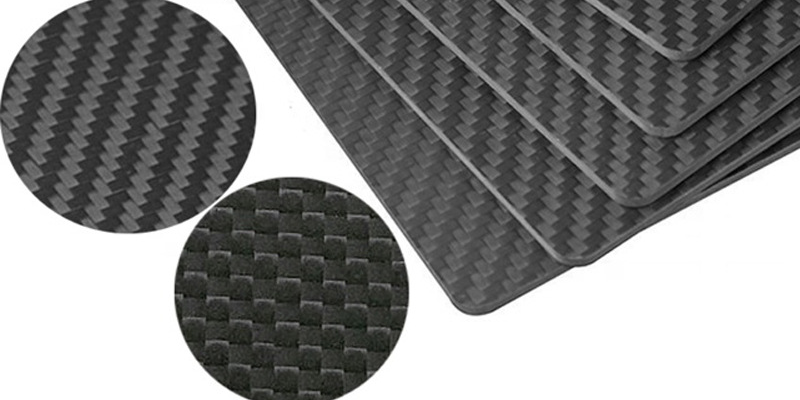
Performance of Fire Retardant FRP in Real-World Scenarios
The performance of fire retardant FRP in real-world fire incidents highlights its importance in modern construction. During a fire, fire retardant FRP panels and components help to delay the spread of flames and provide additional time for evacuation. For example, FRP pipes and ductwork in commercial buildings have been shown to withstand intense fire conditions, preventing significant structural damage. These real-world examples demonstrate how fire retardant FRP materials can protect buildings and people from the devastating effects of fire.
Potential Smoke Damage Even with Fire Retardant FRP
Despite its fire-retardant properties, fire retardant FRP can still produce smoke during a fire, particularly if the resins used contain combustible elements. In some cases, the smoke generated by burning FRP can cause more damage than the flames themselves, particularly in enclosed spaces. Dense smoke can obstruct visibility and make it difficult for occupants to escape, posing additional risks during fire emergencies. Therefore, while fire retardant FRP helps in slowing down flames, it is important to also consider the potential smoke hazards.
ASTM E-84 Test Results for Fire Retardant FRP
The ASTM E-84 test is commonly used to measure flame spread and smoke generation in building materials, including fire retardant FRP. The results of these tests indicate that while FRP materials can significantly limit flame spread, they may still produce high levels of smoke, particularly if they are made with polyester or vinyl ester resins. The test results also highlight the importance of selecting FRP products that balance both flame resistance and smoke control for optimal fire safety.
Addressing Concerns About Smoke in Fire Situations
One of the primary concerns with fire retardant FRP is the amount of smoke it generates during a fire. The resins used in FRP, such as polyester or vinyl ester, can produce large volumes of dense smoke when burned. This can be particularly hazardous in enclosed environments like factories or electronics facilities, where smoke can spread quickly and damage equipment or hinder evacuation.
Impact of Smoke in Enclosed Spaces
In enclosed environments, smoke generated by burning fire retardant FRP can lead to more severe consequences than the flames themselves. Smoke inhalation is a leading cause of fatalities in fire situations, and dense smoke can also obscure exit paths, delaying escape. In spaces such as electronics facilities, smoke can damage sensitive equipment, leading to significant financial losses in addition to the safety risks.
Strategies to Reduce Smoke Generation
To reduce smoke generation, manufacturers often incorporate halogenated fire-retardant resins into fire retardant FRP. These additives help smother the flames, causing the material to self-extinguish and minimizing smoke output. Other strategies include selecting resins that produce less smoke during combustion, such as bromine-based additives, which improve the overall fire performance of fire retardant FRP. By focusing on reducing smoke, building materials can offer enhanced protection during fire incidents, safeguarding both people and property.
FRP Pipe Fire Rating: What Every Industry Needs to Know
Recommendations for Specifying Fire Retardant FRP
When selecting fire retardant FRP for construction projects, it is essential to consult with experienced fabricators and resin manufacturers. These experts can provide valuable insights into the specific fire safety requirements for different environments. For applications involving fiberglass composite panel, they will help in choosing the most suitable type of fire retardant FRP, ensuring the material meets all necessary fire resistance standards. The resin composition and thickness of the panels play critical roles in how the material performs under fire conditions, so working closely with specialists will optimize fire safety.
Consultation with Experts in Fire Retardant FRP
Fabricators and resin manufacturers have in-depth knowledge of how fire retardant FRP behaves during fire incidents. They can offer recommendations on the best materials for each project, considering the specific fire risks and safety codes in your region. Consulting with these experts ensures that your FRP selections are well-informed and tailored to the fire protection needs of the building or industrial space.
Importance of Following Fire Codes for Fire Retardant FRP
Adhering to fire codes is crucial when specifying fire retardant FRP materials. Different regions have distinct regulations regarding flame spread, smoke generation, and fire resistance. It is vital to choose FRP products that meet or exceed these codes to ensure the safety of the structure. Failure to comply with fire regulations can result in significant legal and safety risks. By selecting FRP materials that are designed with fire safety in mind, you can protect both the building and its occupants in case of a fire.
How Fireproof Fiberglass Insulation Enhances Fire Safety
Additional Resources on Fire Retardant FRP
At GangLong Fiberglass, we are committed to helping our clients understand the full scope of fire safety when it comes to fire retardant FRP. Fire safety is not just about choosing the right material, but also about understanding how those materials behave in real-world fire scenarios. We encourage you to explore additional resources that provide in-depth information on the fire safety of fire retardant FRP and the importance of adhering to fire regulations.
Explore Fire Retardant FRP Resources
At GangLong Fiberglass, we offer comprehensive guides and documents that delve into the fire performance of fire retardant FRP components. These materials can help you make informed decisions when specifying FRP for your projects. Our downloadable resources include detailed analyses of how fire retardant FRP behaves under different fire conditions, including information on flame spread, smoke generation, and overall fire resistance.
Downloadable Guides and Detailed Fire Safety Documents
We understand that fire safety is a critical consideration for many industries. That’s why GangLong Fiberglass provides access to valuable, detailed documents focused on fire retardant FRP. These guides cover everything from selecting the right resin to understanding how different FRP products perform during fire incidents. We invite you to download these materials from our platform to ensure you have the information you need to choose the best fire retardant FRP solutions for your projects.
Stay Informed with GangLong Fiberglass
At GangLong Fiberglass, we are dedicated to offering not only top-quality products but also the information you need to make safe, informed choices. Our resources are designed to provide you with a thorough understanding of fire retardant FRP and how it can enhance fire safety in your buildings or industrial applications. Reach out to us today to learn more or download our fire safety materials to start your journey towards better fire protection.
FAQs about Fire Retardant FRP
FRP (Fiberglass Reinforced Plastic) can be made fire retardant by using specialized resins. Standard FRP is not inherently fire retardant, but when treated with fire-retardant additives, it can slow down the spread of flames. These additives work by either releasing flame-inhibiting gases or creating a protective char layer that limits further combustion. Fire retardant FRP is often used in construction projects where fire safety is a top priority, offering protection against fire without compromising the material’s strength and durability. However, even with fire retardant properties, FRP may still emit smoke when exposed to fire, which should be considered in safety planning.
FRP can offer a degree of fire resistance, but its level of resistance depends on the specific formulation of the resin used. While the fiberglass reinforcement in FRP is non-combustible, the resins that bind it can burn. Fire retardant FRP is designed to resist flames and slow down their spread, providing additional time for evacuation in case of a fire. However, the fire resistance of FRP is not as high as materials specifically designed for structural fire protection, such as steel or concrete. Fire codes and regulations will typically determine whether fire retardant FRP is appropriate for a given application.
FRP itself is not inherently flammable, but it can become combustible depending on the resin used. The fiberglass in FRP is non-flammable, but the resin binding the fibers can burn. Fire retardant FRP incorporates additives that make the material more resistant to ignition, reducing its flammability and slowing down flame spread. When exposed to extreme heat, FRP can still emit smoke and gases, which may pose risks in enclosed environments. For this reason, fire retardant FRP is commonly used in applications where fire safety is a concern but where complete fireproofing is not required.
In fire fighting, fire retardant FRP is often used in building materials to provide a certain level of fire protection. It is designed to slow the spread of flames and reduce the amount of smoke generated in a fire. This can help prevent fires from spreading quickly, giving firefighters more time to control the situation. Fire retardant FRP is also used in industrial settings where fire risks are higher, such as chemical plants or electronics facilities. By incorporating fire retardant FRP, building structures can offer better fire safety while maintaining the strength and versatility of fiberglass materials.
Can FRP withstand heat?
Fiberglass Reinforced Plastic (FRP) is a highly durable and versatile material, but its heat resistance is limited depending on the type of resin used in its composition. Generally, FRP can withstand temperatures up to 250°F (121°C) without significant degradation. However, certain types of FRP with specialized resins are engineered to resist higher temperatures, with some variants designed to perform in temperatures up to 500°F (260°C) or even higher. It’s important to consider that sustained exposure to temperatures beyond the material’s rated limit can cause the resin matrix to break down, leading to structural weakening and eventual failure. To determine the heat tolerance of FRP, manufacturers often provide specific temperature ratings for their products. Additionally, the environment in which FRP is used can impact its heat resistance. For example, chemical exposure, humidity, and physical stress can reduce the material’s ability to withstand high temperatures. When using FRP in environments where high heat is a concern, it’s essential to verify the resin type and check its compatibility with the expected temperature range to ensure the material’s integrity and longevity.
What are the 4 main types of FRP?
FRP is a composite material made from a polymer matrix reinforced with fibers. The four main types of FRP are as follows:
Polyester FRP: The most common and widely used type of FRP, polyester-based resins are relatively inexpensive and offer good mechanical properties. They are commonly used in the manufacturing of boats, tanks, and other industrial applications. Polyester FRP is generally resistant to water, chemicals, and corrosion but has limited heat resistance compared to other types.
Vinyl Ester FRP: Vinyl ester resins offer superior chemical resistance and can endure higher temperatures than polyester-based resins. This type of FRP is commonly used in applications that require resistance to harsh chemicals and high temperatures, such as in the automotive and aerospace industries.
Epoxy FRP: Epoxy resins provide exceptional strength, high heat resistance, and excellent adhesive properties. They are used in high-performance applications such as aircraft components, wind turbine blades, and sporting goods. Epoxy FRP offers better resistance to corrosion and environmental degradation than polyester and vinyl ester resins.
Phenolic FRP: Phenolic-based FRP resins are known for their fire resistance and are often used in environments where fire safety is crucial. These are typically used in the construction of fireproof panels and equipment for the aerospace industry and other high-risk fire zones.
Each of these types of FRP has its own advantages and disadvantages depending on the application, and selecting the right type of FRP is crucial for optimal performance.
What are the risks of FRP?
While FRP is a durable and versatile material, it does pose certain risks, particularly during its production, handling, and disposal. One of the main risks is the potential exposure to toxic fumes and dust during the manufacturing process. The resins and fibers used in FRP can release hazardous substances when cut, ground, or otherwise manipulated. These include volatile organic compounds (VOCs), which can be harmful to respiratory health if inhaled over extended periods.
Another significant risk is related to the potential brittleness of the material. While FRP is generally tough, it can become brittle with age, particularly when exposed to extreme weather conditions or ultraviolet (UV) radiation. This brittleness can lead to cracking or breaking of the material, posing a safety hazard, particularly in structures that are designed to support heavy loads.
Additionally, improper disposal of FRP materials can be harmful to the environment. FRP is not biodegradable, and when disposed of improperly, it contributes to landfill waste and can take hundreds of years to break down. Recycling of FRP is also challenging due to its composite nature, which requires specialized facilities.
Lastly, FRP can pose a fire risk if not treated with fire-resistant additives. Although some types of FRP are fire-resistant, others are combustible, and in the event of a fire, FRP can release harmful gases.
Can FRP be used outside?
Yes, FRP can be used outdoors, and it is, in fact, often chosen for exterior applications due to its durability and resistance to environmental factors. FRP’s composition of fiberglass fibers and resin allows it to withstand harsh weather conditions, including exposure to UV radiation, moisture, and temperature fluctuations. However, to ensure the material’s longevity, it’s important to choose the right type of resin. For example, polyester resins, which are commonly used in outdoor FRP products, may degrade over time when exposed to prolonged sunlight unless UV inhibitors are added. Vinyl ester and epoxy resins tend to offer better resistance to UV degradation and are preferred for applications where exposure to sunlight is significant.
In outdoor environments, FRP is frequently used for applications such as roofing, walkways, tanks, and even outdoor furniture. Its resistance to corrosion makes it ideal for use in coastal areas where saltwater exposure would degrade other materials like metal. However, it’s crucial to monitor the condition of outdoor FRP over time, especially in regions with extreme weather, as the material can become more brittle with prolonged exposure to UV rays and temperature extremes.
Are FRP panels toxic?
FRP panels are generally considered safe to use; however, certain precautions must be taken during manufacturing, installation, and disposal. The toxicity of FRP primarily arises from the resins used in the composite material. The most commonly used resins in FRP panels are polyester, vinyl ester, and epoxy, which may emit harmful chemicals during production, installation, or when the material is exposed to extreme temperatures. For example, when cutting or grinding FRP panels, small particles and dust may be inhaled, which can cause respiratory irritation. Prolonged exposure to the dust or vapors emitted by FRP resins, especially during installation or in poorly ventilated areas, can lead to health issues such as lung irritation, dizziness, and headaches.
Furthermore, when FRP panels reach the end of their lifespan and are disposed of improperly, they can release hazardous substances into the environment, particularly if burned. It’s important to follow local regulations regarding the safe disposal of FRP materials. Some manufacturers are working on developing more eco-friendly FRP options with less toxic resin systems, but these products are still relatively new in the market.
In general, FRP panels are not considered toxic in their final form once installed, but it’s essential to exercise caution during handling and processing.
Is FRP the same as fiberglass?
FRP and fiberglass are closely related but not the same. Fiberglass refers to the actual glass fibers that are used as reinforcement in composite materials, while FRP refers to the finished product that results from combining fiberglass with a polymer resin. The fiberglass fibers in FRP provide strength and durability, while the resin binds the fibers together and provides the shape and additional properties such as chemical resistance, flexibility, or heat resistance.
Fiberglass is a key component of FRP, but FRP itself is a composite material. Fiberglass can be used independently for certain applications (such as in insulation or as a standalone reinforcement material), but when combined with resins, it forms FRP, which can be molded into different shapes and sizes for a wide range of applications. Essentially, fiberglass serves as the reinforcing agent in the FRP composite, while the resin provides the structural integrity and additional performance features.
Is fiberglass a fire retardant?
Fiberglass itself is inherently non-combustible, which means it will not catch fire under normal circumstances. However, fiberglass alone is not necessarily a fire retardant. The fire-resistance of fiberglass depends on the type of resin used in the composite material. While fiberglass strands are not flammable, the resins, such as polyester or vinyl ester, can be combustible. In the event of a fire, fiberglass will typically act as a passive barrier, slowing the spread of flames but not entirely preventing them. For applications where fire resistance is critical, fire-retardant additives can be mixed into the resin to enhance the fire-resistance of the entire FRP structure.
In summary, fiberglass is not a fire-retardant material on its own, but it can be treated with fire-resistant resins or additives to improve its fire safety.
Are FRP panels combustible?
Yes, FRP panels can be combustible depending on the type of resin used in their composition. While the fiberglass fibers themselves are non-combustible, the resins, such as polyester, vinyl ester, or epoxy, can catch fire under certain conditions. Polyester and vinyl ester resins are particularly vulnerable to combustion at high temperatures. However, fire-resistant FRP panels are available by incorporating fire-retardant resins or additives into the composite material. These panels are designed to resist ignition and slow the spread of fire. The fire resistance of FRP panels is often classified according to their fire rating, with some panels meeting Class A fire ratings, which indicates they offer the highest level of fire resistance.
In any environment where fire safety is a concern, it’s essential to select FRP panels that are designed to meet the necessary fire-resistance standards and are treated with appropriate fire-retardant additives to prevent combustion.
What are the hazards of FRP materials?
The hazards associated with FRP materials mainly stem from their manufacturing, handling, and disposal processes. One significant hazard is the release of toxic fumes and dust when cutting, sanding, or grinding FRP materials. The resins used in FRP, such as polyester and vinyl ester, contain volatile organic compounds (VOCs) that can be harmful when inhaled, leading to respiratory issues, skin irritation, and headaches.
Another risk is the brittleness of FRP over time. FRP materials can become more fragile and prone to cracking or breaking when exposed to UV radiation and temperature fluctuations, which can pose a physical hazard if the material fails in a structural application.
Improper disposal of FRP materials is also a concern, as these materials are non-biodegradable and can contribute to environmental pollution when discarded in landfills. Additionally, burning FRP can release toxic fumes, including carbon monoxide and other hazardous chemicals.
Finally, while FRP is resistant to corrosion, it can be susceptible to damage from physical impacts, and once damaged, it can degrade rapidly, compromising its strength and safety.
What is the maximum temperature for FRP?
The maximum temperature for FRP largely depends on the type of resin used in the composite. Standard polyester-based FRP is typically rated for use up to temperatures around 250°F (121°C), while vinyl ester and epoxy resins can handle slightly higher temperatures. FRP with specialized heat-resistant resins can withstand temperatures up to 500°F (260°C) or more. However, prolonged exposure to temperatures exceeding the material’s rated tolerance can lead to the degradation of the resin and the weakening of the entire composite structure.
When selecting FRP for high-temperature environments, it is crucial to ensure that the resin and fiberglass combination is specifically designed to withstand the expected thermal conditions. In high-heat applications such as industrial settings, choosing a fire-resistant or heat-resistant variant of FRP is recommended to prevent material failure.
Is FRP fire resistant?
FRP is not inherently fire-resistant. The fiberglass itself is non-combustible, but the resin used in the composite material can catch fire. However, fire-resistant FRP panels and materials are available, which are treated with fire-retardant additives to improve their resistance to ignition. These fire-resistant resins can significantly delay the spread of flames and reduce the heat transfer through the material.
In high-risk fire environments, it is essential to choose FRP products with specific fire ratings. For instance, some FRP panels and grating materials can achieve a Class A fire rating, which indicates the highest level of fire resistance. When using FRP in situations where fire safety is critical, selecting fire-resistant FRP products and ensuring they meet the relevant fire codes and standards is crucial to ensure safety.
What does FRP stand for in fire?
In fire-related contexts, FRP stands for Fire-Resistant Panel or Fire-Resistant Plastic. It refers to a composite material made from fiberglass and resin that is designed to resist flames and heat. When used in fire-resistant applications, FRP panels are specifically engineered to provide protection against the spread of fire. FRP products can be treated with fire-retardant chemicals to improve their fire resistance, making them suitable for use in industrial, commercial, and other high-risk fire environments. The fire rating of FRP products is typically determined by how well they perform in fire tests, and it is essential to choose materials that meet the necessary fire-safety standards for the application.
Is Class A FRP fire rated?
Yes, Class A FRP is fire-rated. The Class A fire rating is the highest level of fire resistance according to the National Fire Protection Association (NFPA) standards. FRP materials that achieve a Class A fire rating are highly resistant to ignition and have low flame spread characteristics. These materials are ideal for use in applications where fire safety is critical, such as in commercial buildings, industrial facilities, and transportation systems.
Class A fire-rated FRP is specifically treated with fire-retardant additives or made from inherently fire-resistant resins, ensuring that the material can withstand high temperatures and resist the spread of fire for a longer period compared to non-rated FRP products.
Is FRP bad for the environment?
FRP has several environmental considerations, especially in terms of its disposal and manufacturing processes. While FRP materials are durable and offer long lifespans, they are non-biodegradable, meaning they do not break down naturally in the environment. When disposed of improperly, such as in landfills, FRP can contribute to long-term waste accumulation. Additionally, the production of FRP requires energy-intensive processes and can release pollutants, including VOCs and greenhouse gases, into the atmosphere.
That being said, efforts are underway to reduce the environmental impact of FRP by developing more sustainable manufacturing methods, improving the recyclability of FRP, and using eco-friendly resins. Despite these advances, it remains important for industries and consumers to be mindful of the environmental impact of FRP and seek out responsible disposal methods.
What is the fire rating of FRP grating?
FRP grating is available with different fire ratings depending on its composition. For example, FRP grating made from polyester resins typically achieves a Class C fire rating under the ASTM E84 test, which measures flame spread and smoke development. However, FRP grating made from fire-resistant resins can achieve Class A or Class B ratings, indicating a higher level of fire resistance.
Class A FRP grating is highly fire-resistant, offering low flame spread and reduced smoke emissions in the event of a fire. This makes it suitable for applications where fire safety is critical, such as in chemical plants, oil rigs, and industrial settings.
Is FRP stronger than steel?
FRP can be stronger than steel in certain applications due to its high strength-to-weight ratio. While steel is undeniably strong and durable, it is much heavier than FRP. This makes FRP an ideal material for applications where strength is required but weight needs to be minimized.
In terms of specific strength, some types of FRP can be engineered to exceed the strength of steel in certain configurations. For example, FRP used in construction, aerospace, and automotive applications can be designed to outperform steel in terms of tensile strength while being much lighter.
However, FRP has its limitations when compared to steel. While it is strong and corrosion-resistant, it is more prone to damage under impact and may not offer the same long-term durability in all environments. The choice between FRP and steel ultimately depends on the specific needs of the application, including weight, strength, corrosion resistance, and cost considerations.
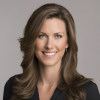
As the editor of GangLong Fiberglass, I have years of experience and in-depth research, focusing on cable tray products, fiberglass solutions, and grille systems. I incorporate years of industry insights and practical experience into every content, committed to promoting the progress of the industry. At GangLong Fiberglass, my commitment is reflected in every product, from innovative cable trays to durable fiberglass solutions and sturdy grille systems. As an authoritative voice in the industry, my goal is to provide valuable information to professionals and businesses and promote forward-looking solutions.