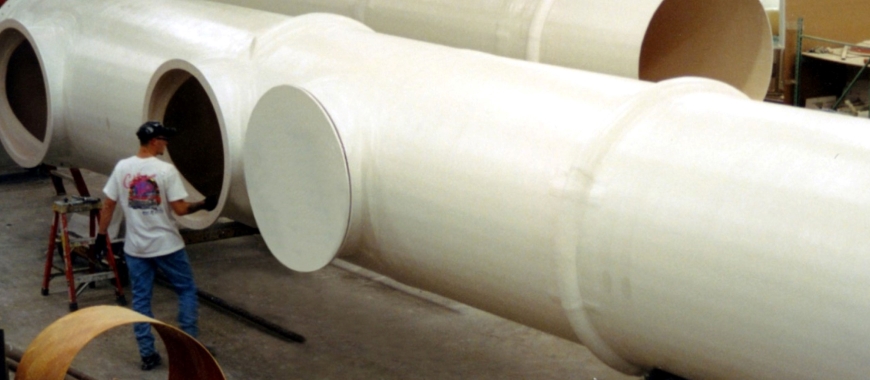
FRP pipe life expectancy varies; FRP pipe last 30-40 years, while bleach pipes may last 10-15 years, depending on conditions. One of the key factors contributing to this long lifespan is the material’s inherent corrosion resistance and UV stability, which makes it ideal for use in harsh environments. Unlike traditional materials that can degrade quickly when exposed to chemicals, saltwater, or extreme temperatures, FRP maintains its structural integrity for decades. With proper maintenance, including regular inspections and cleaning, the frp pipe life expectancy can be extended even further, offering a durable and cost-effective solution for industrial applications across various sectors.
Simplifying Your Life: Key Functionalities
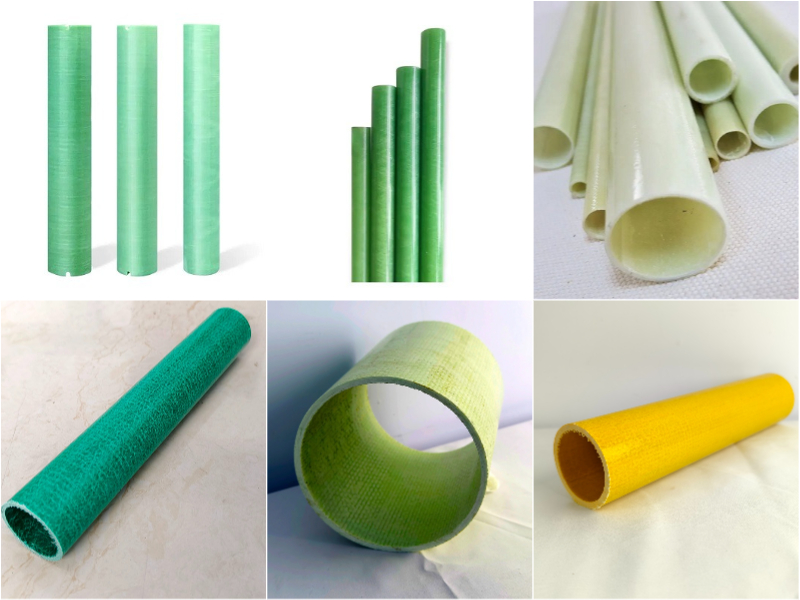
Attributes | Details |
---|---|
Place of Origin | Hebei, China |
Brand Name | GangLong Fiberglass |
Product Name | FRP Pipe |
Material | Fiberglass Reinforced Plastic |
Technology | Reeling, Cutting Process, Pultrusion |
Surface Treatment | Smooth Paint or Customer Requirement |
Processing Services | Uncoiling, Forming, Welding, Punching, Cutting |
Color | Customized Color |
Shape | Customized Shape |
Size | Customized Size |
Thickness | Customized Thickness |
Length | Customized Length |
Density | 1.7-1.9 g/cm3 |
OEM | OEM Accepted |
Absolute Roughness Range | 0.008 mm |
Features | Durable, Lightweight, High Strength, Flame Retardant |
Tensile Strength | >550 MPa |
Certificate | ISO9001 |
Application | Construction, Industry, Housing |
Supply Capacity | 10000 kg/kg/month |
Port | All Major Ports |
Packing Details | As per Customer Requirement |
Sales Unit | Single Item |
The Key of FRP Pipe Life Expectancy
FRP pipe life expectancy refers to the anticipated operational lifespan of Fiberglass Reinforced Plastic pipes used in industrial and commercial applications. Known for their durability, FRP pipes are a popular choice due to their corrosion resistance, UV stability, chemical compatibility, and suitability for harsh environments. With proper care and maintenance, FRP pipes can offer reliable performance for decades, providing long-term value in fluid transport systems.
Primary Factors Affecting FRP Pipe Life Expectancy
The life expectancy of FRP (Fiberglass Reinforced Plastic) pipes depends on various factors, including the materials used, environmental conditions, operational parameters, and maintenance practices. Understanding these factors is essential for ensuring the longevity and optimal performance of FRP pipes in various applications, from industrial chemical transport to wastewater management. Below are the key aspects that influence the lifespan of FRP pipes.
Corrosion Resistance
One of the primary advantages of FRP pipes is their exceptional corrosion resistance. Unlike traditional metal pipes, which are vulnerable to chemical reactions that cause rust and corrosion, FRP pipes are designed to resist chemical attacks from a variety of harsh substances, including acids, alkalis, solvents, and other corrosive fluids. This resistance makes FRP pipes particularly suited for industries dealing with aggressive chemicals, such as chemical processing and wastewater treatment. By preventing corrosion, FRP pipes maintain their structural integrity and extend their life expectancy, offering a long-term solution for fluid transport in chemically demanding environments.
UV Stability
FRP pipes are engineered to withstand UV degradation, making them ideal for outdoor applications exposed to sunlight. Over time, UV rays can cause certain materials to become brittle, lose strength, and deteriorate. However, FRP pipes are specially designed with UV-resistant resins, ensuring that they maintain their strength and durability when exposed to sunlight. This UV stability is particularly crucial for applications in industries like agriculture, water treatment, and outdoor infrastructure projects where pipes are exposed to harsh weather conditions and direct sunlight for extended periods. The UV resistance of FRP pipes prevents premature aging and degradation, significantly enhancing their lifespan.
Chemical Compatibility
The type of resin used in the manufacture of FRP pipes plays a significant role in their chemical compatibility and overall life expectancy. FRP pipes can be made from various resin types, including polyester, vinyl ester, and epoxy resins, each offering different levels of protection against chemical corrosion. For example, vinyl ester resins provide superior chemical resistance, particularly against harsh acids and solvents, making them ideal for industries dealing with aggressive chemicals. Proper selection of resin type ensures that FRP pipes can handle the specific chemical environments they are exposed to, thus extending their service life.
Environmental Conditions
Environmental factors such as temperature fluctuations, humidity, and exposure to external elements significantly affect the performance of FRP pipes. These pipes are designed to withstand extreme conditions, such as coastal areas with high humidity or industrial environments with fluctuating temperatures. For example, FRP pipes used in coastal regions are resistant to the corrosive effects of saltwater, which can significantly degrade other pipe materials. Additionally, FRP pipes can handle temperature variations and moisture, making them versatile and durable for a wide range of applications. The ability of FRP pipes to withstand environmental stressors contributes to their long lifespan and reliability.
Mechanical Stress
Mechanical stresses, such as those caused by internal fluid flow, external forces, or pressure changes, can impact the longevity of FRP pipes. These stresses can lead to wear and tear, which, over time, may cause pipe failure if not properly managed. Proper installation practices, including the use of correct support systems and pipe alignment, are essential for minimizing mechanical stress on FRP pipes. Additionally, ensuring that the pipes are sized and installed according to industry standards helps prevent excessive pressure buildup and other stresses that could shorten the life of the system. By reducing mechanical wear, the overall lifespan of FRP pipes can be extended, ensuring the longevity of the piping system.
Temperature and Thermal Cycling
Temperature fluctuations, particularly in high-temperature environments, can affect the structural integrity of FRP pipes. Prolonged exposure to extreme thermal cycling, where the pipes undergo repeated heating and cooling, can cause gradual degradation over time. This is especially true for high temperature FRP pipe used in industries such as power generation, chemical processing, or oil and gas. Proper material selection, including the choice of resin and reinforcement types designed to withstand thermal cycling, is essential to maintaining the performance of FRP pipes in such conditions. FRP pipes that are designed to handle thermal expansion and contraction can avoid premature failure and contribute to the overall lifespan of the piping system.
Preventive Maintenance
Regular preventive maintenance is crucial in extending the life expectancy of FRP pipes. Over time, even the most durable pipes may experience wear or damage due to factors like chemical exposure, physical stress, or UV degradation. Routine inspections, cleaning, and monitoring of the piping system ensure that any potential issues are identified and addressed before they lead to significant damage or failure. Proper maintenance practices, such as ensuring that gaskets and seals are in good condition and that pipes are free from blockages or stress points, help preserve the integrity of the system and extend the lifespan of FRP pipes.
How Materials and Methods Used in FRP Manufacturing Affect FRP Pipe Life Expectancy
In addition to environmental and operational factors, the materials and methods used to fabricate FRP equipment have a significant impact on its lifespan. The composition of the resin, the type and quantity of reinforcement materials, and the lamination process all contribute to the overall durability and performance of FRP pipes and equipment. Below is an expanded discussion of the key factors that influence the longevity of FRP equipment:
Type of Resin
The type of resin used in the manufacturing of FRP pipes plays a critical role in their longevity. Polyester, vinyl ester, and epoxy resins are commonly used, each offering different levels of resistance to chemicals, temperature fluctuations, and mechanical stress. Epoxy resins, for example, provide superior resistance to aggressive chemicals and high temperatures, making them ideal for demanding applications in industries such as chemical processing and oil and gas. On the other hand, polyester resins are more cost-effective and are suitable for less aggressive environments. The choice of resin directly affects the FRP pipe life expectancy, as more durable resins enhance the performance and extend the lifespan of the equipment.
Type and Quantity of Initiators, Promoters, and Other Chemicals
The addition of initiators, promoters, and other chemicals to the resin formulation can influence the curing process and, ultimately, the mechanical properties of the FRP pipes. Initiators help start the polymerization process, while promoters and accelerators control the rate of curing. The type and quantity of these additives must be carefully balanced to ensure that the resin cures properly and develops the desired strength and chemical resistance. Too much or too little of these chemicals can result in inconsistent curing, reducing the overall quality and lifespan of the FRP equipment.
Type and Quantity of Reinforcement Materials
The reinforcement materials, typically fiberglass, play a vital role in the strength, stiffness, and durability of FRP pipes. The type of fiberglass, such as E-glass or S-glass, and the amount used, significantly affect the mechanical properties of the final product. For example, S-glass provides greater strength and resistance to environmental degradation than E-glass, making it suitable for high-performance applications. The right choice and quantity of reinforcement materials ensure that the FRP equipment can withstand mechanical stresses, environmental factors, and operational conditions, ultimately extending the lifespan of the equipment.
Laminate Design
The design of the FRP laminate also affects the strength and longevity of the equipment. Laminate design refers to the arrangement and layering of the fiberglass and resin materials, which influence the overall mechanical properties of the FRP pipes. A well-designed laminate structure will ensure that the equipment can handle the stresses it will encounter during use, including internal pressure, external loads, and temperature fluctuations. The number of layers and their arrangement in the laminate determine the FRP pipe life expectancy by providing resistance to cracking, delamination, and other forms of failure.
Method of Lamination
The method used to laminate the FRP materials is another critical factor that impacts the performance and lifespan of the equipment. Common lamination techniques include hand lay-up, spray-up, filament winding, and pultrusion. Each method has its advantages and is suited to specific applications. For example, filament winding is often used for making pipes and pressure vessels, as it allows for precise control of fiber orientation and thickness, leading to stronger and more durable products. The proper lamination technique ensures the consistency of the FRP pipes and improves their resistance to mechanical stress and environmental degradation.
Fiber Orientation
The orientation of the fibers within the FRP laminate is a crucial determinant of the material’s strength and durability. Fibers aligned in the direction of the load (longitudinal fibers) provide the greatest strength and resistance to tensile forces, while fibers arranged at angles can improve the material’s resistance to shear stresses. The design of the fiber orientation should match the expected loads and stress points within the system. By optimizing fiber orientation, manufacturers can enhance the performance of FRP pipes, making them more resistant to cracking, bending, and other forms of failure.
Void Content
Void content refers to the amount of air or other gases trapped in the resin during the manufacturing process. High void content can weaken the bond between the resin and reinforcement fibers, reducing the overall mechanical strength of the FRP pipes. It can also create potential sites for moisture infiltration, which can lead to degradation over time. Ensuring low void content during production is essential for maximizing the FRP pipe life expectancy, as it improves the integrity of the material and its resistance to environmental stressors.
Cure Characteristics
The curing process is a critical factor that influences the properties of FRP pipes. The cure characteristics, such as temperature, time, and pressure, determine how well the resin hardens and bonds with the fiberglass reinforcement. Insufficient curing can lead to a weakened material, while over-curing can cause brittleness. Proper curing is essential for achieving optimal chemical resistance, strength, and durability. Additionally, the curing process affects the material’s FRP pipe life expectancy, as improperly cured pipes are more prone to cracking, wear, and chemical degradation over time.
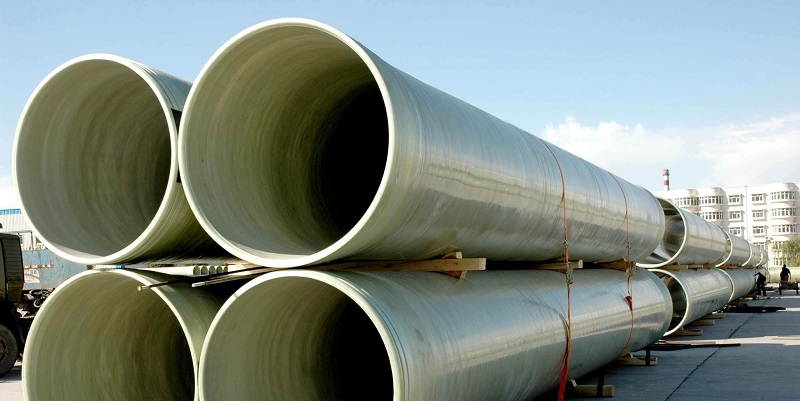
Maximizing FRP Pipe Life Expectancy: Maintenance, Monitoring, and Installation Best Practices
Regular maintenance and monitoring are essential for ensuring that FRP pipes perform optimally throughout their lifespan. While FRP pipes require low maintenance, routine inspections and minor maintenance can significantly extend their service life by identifying potential issues early and addressing them before they become major problems. Additionally, the use of FRP pipe shields can provide extra protection, helping to prevent mechanical damage, UV exposure, and chemical attacks, further contributing to the longevity of the pipes.
Maintenance and Monitoring
Regular Inspections
Conducting regular inspections is key to identifying any potential issues with FRP pipes. Inspections can reveal signs of wear, damage, or changes in the pipe’s condition, allowing for timely repairs or replacements. Scheduling inspections on a routine basis ensures the pipes are functioning properly and helps maximize their life expectancy.
Preventive Maintenance
Preventive maintenance, such as cleaning and checking for leaks, helps extend FRP pipe life expectancy. Regular cleaning removes debris and buildup from the interior, ensuring the flow of fluids remains unobstructed and reducing stress on the system. Checking for small leaks or cracks can prevent larger issues from developing, thus prolonging the operational life of the piping system.
Monitoring Environmental Conditions
Monitoring environmental conditions around FRP pipes is important for maximizing their longevity. Changes in temperature, humidity, or exposure to chemicals can all affect pipe performance. By tracking these conditions and making necessary adjustments, industries can ensure their FRP piping systems remain in optimal condition over time.
Maintenance Practices to Extend FRP Pipe Life Expectancy
While FRP pipes are low-maintenance, regular inspections and preventive maintenance are still essential to maximize their life expectancy. Routine tasks like visual inspections, pressure testing, and leak monitoring help ensure long-term performance. Additionally, cleaning the pipes periodically to prevent blockages and applying protective coatings or liners can further enhance their durability and resistance to environmental factors like UV radiation and chemical attacks.
The Key of Installation in FRP Pipe Life Expectancy
Proper installation is crucial to ensuring the FRP pipe life expectancy. Incorrect installation methods, such as poor alignment, improper joint connections, or inadequate support, can lead to stress points and premature failure. By following best practices during installation, the lifespan of FRP pipes can be significantly extended.
Joint Integrity
Ensuring proper joint connections is essential for maintaining the structural integrity of FRP pipes. Using compatible fittings and seals that can withstand the operating conditions of the system is vital to prevent leaks and weak spots that can reduce the durability of the pipe system.
Support Systems
Proper support of FRP pipes during installation is crucial. Adequate support prevents sagging or bending, which can cause stress fractures over time. Using appropriate hangers and brackets ensures the pipes maintain their structural integrity and perform reliably over their intended lifespan.
Alignment and Positioning
Correct alignment during installation prevents unnecessary stress on the FRP pipes, reducing the likelihood of cracks or damage during operation. Proper alignment and positioning ensure that the pipes perform optimally, extending their life expectancy.
The Role of Installation in FRP Pipe Life Expectancy
Installation is a critical factor in maximizing the life expectancy of FRP pipes. Incorrect installation, such as improper alignment or joint sealing, can lead to undue mechanical stress and premature failure. Following manufacturer guidelines and working with experienced professionals ensures that FRP pipes perform optimally over their service life.
By prioritizing correct installation practices, using appropriate joining methods, and ensuring proper handling and support during transportation, industries can significantly extend the life of their FRP pipe systems. Proper joint installation is vital for preventing leaks and stress, ensuring the system performs reliably for decades.
Selecting the Right FRP Pipe Spacers for Your System
Applications and Industries Benefiting from FRP Pipe Life Expectancy
FRP pipes are used across a wide range of industries due to their versatility and long lifespan. Industries that benefit from frp pipe life expectancy include chemical processing, oil and gas, water treatment, and marine applications.
Applications and Industries
Chemical Processing
The chemical resistance of FRP pipes makes them an ideal choice for transporting aggressive fluids in chemical processing plants. The long lifespan and low maintenance requirements of FRP pipes ensure reliable performance, even in environments with harsh chemicals.
Oil and Gas
In the oil and gas industry, frp pipe life expectancy is highly valued for transporting fluids under high pressure and temperature conditions. FRP pipes can withstand the demanding conditions of oil and gas operations, providing long-term performance without the need for frequent maintenance or replacement.
Water Treatment
FRP pipes are commonly used in water treatment facilities due to their resistance to corrosion and chemical degradation. The long lifespan of FRP pipes ensures that they can handle the continuous flow of water and wastewater, making them a reliable choice for both municipal and industrial water treatment applications.
Marine Applications
The resistance of FRP pipes to saltwater and harsh marine environments makes them a popular choice for offshore and coastal installations. Their ability to withstand the corrosive effects of seawater ensures that FRP pipes maintain their performance for decades, reducing the need for frequent replacements in marine environments.
From water treatment to chemical processing and offshore installations, FRP pipes are increasingly the material of choice for industries seeking durability and reliability over the long term. The FRP pipe life expectancy in these demanding environments, along with FRP pipe stiffness, is a key reason why FRP is the material of choice for many operators.
The Advantages of FRP Over Traditional Materials
FRP pipes offer numerous advantages over traditional materials such as steel or concrete, particularly in terms of longevity and cost-effectiveness. Understanding these advantages helps industries make informed decisions when it comes to selecting materials for their piping systems.
Cost-Effectiveness
FRP pipes offer long-term cost savings due to their low maintenance requirements and extended lifespan. Although the initial investment in FRP piping systems may be higher than other materials, the reduced need for repairs and replacements makes them a more economical option over time. With lower operational costs, FRP pipes provide excellent value for industries seeking durable and cost-efficient solutions.
Low Maintenance
One of the most significant advantages of FRP pipes is their low maintenance requirements. Unlike metal pipes, which are prone to rust and corrosion, FRP pipes do not require frequent maintenance or protective coatings to prevent deterioration. This low maintenance aspect contributes to the overall frp pipe life expectancy and reduces the need for costly repairs or replacements.
Ease of Installation
FRP pipes are lightweight compared to traditional materials, making them easier to transport and install. This ease of installation reduces labor costs and shortens the installation timeline, providing additional cost savings for industries. Additionally, the flexibility of FRP pipes allows for easier handling, which further simplifies the installation process.
Long-Term Performance
The long-term performance of FRP pipes, such as uv resistant frp pipe, is one of the key reasons they are chosen for industrial applications. Their resistance to environmental factors such as UV radiation, chemical exposure, and extreme temperatures ensures that FRP pipes maintain their structural integrity over time. This durability makes FRP pipes a reliable choice for industries seeking long-lasting piping solutions.
FRP Resistance Properties
FRP pipes are known for their versatility and resistance to a wide range of environmental factors. The frp pipe life expectancy is greatly enhanced by the material’s resistance to corrosion, temperature extremes, and mechanical stress. In addition to these features, FRP offers several other resistance properties that contribute to its long lifespan.
FRP pipes are flame-retardant, which means that they can be used safely in environments where fire hazards are a concern. This property is particularly important in industries such as oil and gas, where fire safety is a top priority. GangLong Fiberglass produces FRP pipes with flame-retardant coatings that meet industry standards, ensuring safe and durable performance in fire-prone environments.
Another important feature of FRP pipes is their non-conductive nature, which makes them ideal for applications where electrical conductivity could pose a risk. In industries such as power generation or telecommunications, the use of FRP pipes ensures that there is no risk of electrical interference or conduction, further increasing the safety and life expectancy of the system.
FRP’s resistance to environmental factors such as saltwater, acids, and other aggressive chemicals also plays a significant role in the frp pipe life expectancy. FRP pipes are commonly used in marine environments, where exposure to saltwater can quickly degrade traditional metal piping systems. The inherent resistance of FRP to these elements allows it to maintain its structural integrity over time, even in the most challenging environments.
FRP Strength and Durability Over Time
FRP pipes maintain their strength and durability over long periods, providing industries with a reliable piping solution. The combination of glass fibers and resin in FRP construction gives these pipes their high strength-to-weight ratio, which allows them to withstand significant pressure and stress.
Maintaining Structural Integrity
Over time, FRP pipes retain their structural integrity better than many traditional materials. The fibers within the resin matrix provide reinforcement that resists mechanical wear and tear, even in demanding conditions. This feature is particularly important in industries where pipes are subject to continuous pressure, vibration, or temperature fluctuations. By maintaining their mechanical properties, FRP pipes can continue functioning effectively for decades, contributing to a longer frp pipe life expectancy.
Durability in Corrosive Environments
FRP’s durability in corrosive environments sets it apart from other materials. Unlike steel, which can rust or corrode when exposed to moisture or chemicals, FRP is immune to such degradation. This resistance ensures that FRP pipes do not weaken over time, allowing them to maintain their durability in the long run. Industries that deal with corrosive substances, such as chemical plants and wastewater treatment facilities, particularly benefit from this characteristic, as it leads to fewer repairs or replacements.
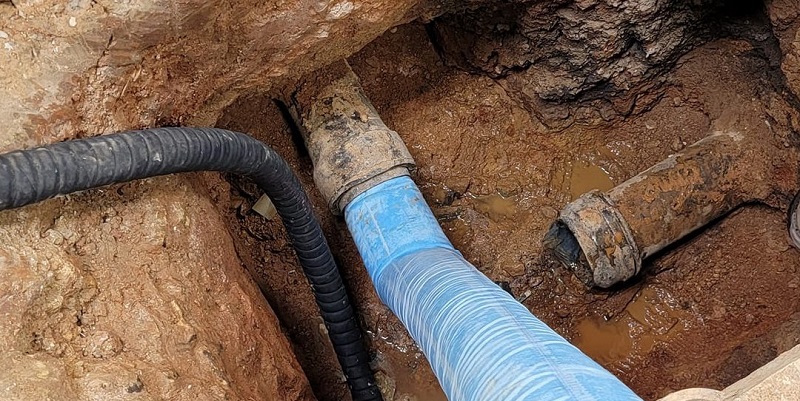
Importance of FRP Pipe Span Charts in Industrial Piping
Future Trends Impacting FRP Pipe Life Expectancy
Future Trends
Advancements in materials science and manufacturing techniques are continuously enhancing the FRP pipe life expectancy, enabling these pipes to perform better in increasingly challenging environments. As industries demand more durable and specialized piping systems, innovations in FRP technology are helping to extend the useful life of these products. Below are some of the key trends that are expected to shape the future of FRP pipes:
Developments in Resin Formulations
One of the most significant areas of innovation in FRP pipes is the development of new resin formulations that offer enhanced resistance to specific chemicals, temperatures, or environmental conditions. These improved resins are designed to make FRP pipes more resistant to aggressive substances, extreme temperatures, and UV exposure. For example, advanced epoxy and vinyl ester resins provide exceptional protection against chemical attacks and are increasingly used in industries such as chemical processing and oil and gas. As these formulations evolve, FRP pipes will be able to meet the needs of even more specialized applications, further extending their lifespan.
Improvements in Coating Technologies
Coatings play a crucial role in enhancing the durability of FRP pipes by providing an additional layer of protection against external environmental factors. The latest advancements in coating technologies have improved FRP pipe protection from UV radiation, abrasion, and mechanical damage. For example, new UV-resistant coatings are designed to prevent degradation from prolonged exposure to sunlight, while abrasion-resistant coatings help protect the pipes from wear and tear in environments where they may be exposed to physical impact. By using these advanced coatings, FRP pipes can maintain their integrity and functionality over a longer period, especially in harsh operating conditions.
Advanced Manufacturing Techniques
As manufacturing techniques continue to improve, FRP pipes are becoming more reliable and durable. Advances in filament winding and pultrusion methods, for example, allow for greater precision in the construction of FRP pipes, ensuring higher consistency and strength. These methods allow manufacturers to create pipes with improved structural integrity, tailored to meet the exact specifications required for particular applications. Additionally, automation and better quality control in manufacturing processes are reducing the likelihood of defects, leading to longer-lasting FRP pipes and fewer issues related to system failure or repair needs.
The Growing Role of FRP in Industrial Applications
As industries continue to evolve, the need for more efficient, durable, and cost-effective piping systems is increasing. FRP technology is becoming an essential part of modern infrastructure, with applications expanding beyond traditional use in water treatment and chemical processing to new industries, such as renewable energy, offshore oil and gas, and waste management. The ability of FRP pipes to withstand harsh environments, including high pressure, corrosive chemicals, and extreme temperatures, positions them as a key component of future industrial systems. At GangLong Fiberglass, we are at the forefront of these advancements, providing high-quality FRP pipes that meet the stringent requirements of modern industrial applications.
Planning for Long-Term Performance
The life expectancy of FRP pipes is a critical factor when planning and designing fluid transport systems. Engineers, procurement specialists, and project managers must carefully select the right materials, configurations, and installation practices to ensure optimal performance over the long term. FRP pipes are a significant investment, and ensuring that they function efficiently throughout their service life requires careful planning and proactive management.
Key Considerations for Long-Term FRP Pipe Performance
To ensure the long-term performance of FRP piping systems, several factors must be considered during the planning and design stages:
- Environmental Exposure: It is essential to assess the environmental conditions to which the pipes will be exposed. For instance, FRP pipes installed in coastal areas will need enhanced protection against saltwater corrosion, while pipes in chemical processing facilities will need resistance to specific chemicals.
- Material Selection: Choosing the right resin and reinforcement material based on the operating conditions is crucial for maximizing the lifespan of FRP pipes. Advanced resin formulations and high-strength reinforcement fibers are ideal for aggressive applications.
- Proper Installation Techniques: Correct installation practices are vital to avoid issues such as poor alignment, improper joint connections, and insufficient support, which can all reduce the life expectancy of FRP pipes.
- Ongoing Maintenance: Regular inspections and preventive maintenance should be a part of the operational schedule. While FRP pipes require low maintenance, periodic inspections for leaks, cracks, and other damage can help extend their lifespan and prevent costly repairs.
Working with Experienced Suppliers
Partnering with experienced suppliers like GangLong Fiberglass ensures that you receive guidance on material selection, installation best practices, and maintenance recommendations that will optimize the FRP pipe life expectancy. We provide high-quality products and expert support, ensuring that the FRP pipes you choose meet the specific demands of your project and perform efficiently throughout their lifecycle.
Reducing Downtime and Maintenance Costs
Planning for the long-term performance of FRP pipes helps reduce downtime and lowers maintenance costs. By selecting the right materials, ensuring proper installation, and committing to regular maintenance, industries can extend the operational life of their FRP piping systems. Proper planning also leads to enhanced operational efficiency, making FRP pipes a cost-effective solution for industrial and commercial applications.
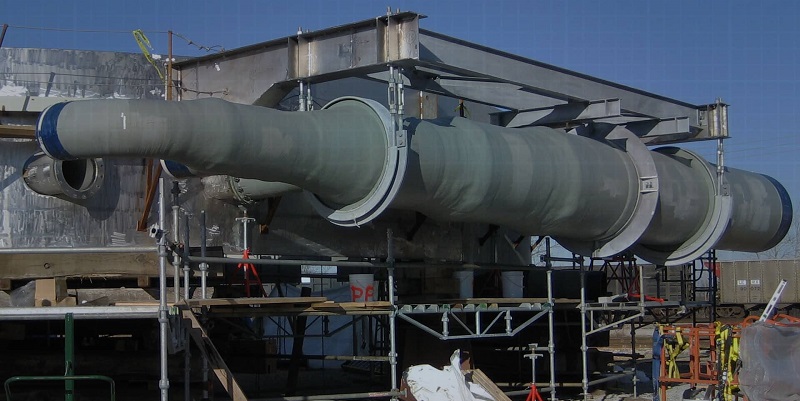
Know FRP’s Coefficient of Thermal Expansion
Ensuring Maximum FRP Pipe Life Expectancy: Responsibilities of Manufacturers and Owners
The life expectancy of FRP (Fiberglass Reinforced Plastic) equipment is greatly influenced by both the manufacturer and the owner, with specific responsibilities for each party in ensuring the equipment’s longevity. Proper materials, design, installation, and maintenance practices all play a role in maximizing the FRP pipe life expectancy and equipment lifespan. Below is an expanded overview of the responsibilities of both the manufacturer and the owner in achieving optimal FRP equipment performance.
Manufacturer’s Role in Maximizing FRP Equipment Life
The original equipment manufacturer (OEM) is responsible for selecting the right materials, engineering the equipment design, and ensuring quality fabrication. To achieve maximum product life, the manufacturer must focus on the following key areas:
Design and Engineering
The manufacturer must design the FRP equipment in accordance with industry standards and the specific service conditions. Professionals specializing in FRP corrosion equipment design should be involved to ensure that the equipment is engineered to handle the expected service environment, which helps extend its lifespan. Proper design not only enhances durability but also minimizes manufacturing costs.
Compliance with Specifications
Manufacturers must fully comply with the specifications provided for each part of the equipment. If the specifications are not available, the manufacturer should work with FRP engineers or external specialists to create them, ensuring that the equipment is built to withstand the anticipated chemical and environmental conditions.
Use of Quality Materials
Only high-quality materials should be used in manufacturing FRP pipes. Using substandard materials can significantly reduce the lifespan of the equipment, making it crucial to avoid cost-cutting in this area. Quality materials ensure that the pipes can handle corrosive substances, high pressures, and temperature variations without degrading prematurely.
Manufacturing Methods
FRP equipment should be fabricated according to high industry standards. Using established techniques for fiberglass fabrication, such as those outlined in RTP-1 (Resin and Thermoset Plastic) guidelines, ensures that the pipes and equipment are durable, reliable, and safe. Manufacturers should be experienced and certified in producing FRP equipment similar to the customer’s needs.
Owner’s Responsibility in Maintaining FRP Equipment
While the manufacturer plays a significant role in designing and fabricating FRP equipment, the owner is responsible for proper installation, operation, and maintenance. The following are key responsibilities to maximize the service life of FRP equipment:
Transportation
The equipment should be transported to the job site using carriers who understand fiberglass. Although FRP is durable, it can still be damaged more easily than materials like steel, and such damage may not always be visible. Proper inspection during transportation ensures that no damage occurs before installation.
Installation
The equipment should be installed by technicians knowledgeable about fiberglass. FRP parts damaged during installation are likely to have a shorter lifespan than undamaged parts. Before installation, each FRP part should be visually inspected for damage to ensure that it is in good condition before being used.
UV Protection
If FRP equipment is installed outdoors, particularly in sunny areas, additional UV protection may be necessary. While most reputable manufacturers provide UV protection, applying a light-colored gelcoat can offer extra protection. This will help prevent UV degradation and prolong the lifespan of the equipment.
Maintenance
Though FRP is low maintenance, it is not maintenance-free. Regular inspections and care can significantly extend the life of the equipment. Annual inspections are especially important in highly corrosive environments, as they help identify issues before they lead to significant damage. In less corrosive environments, inspections can be scheduled less frequently, but it is essential that knowledgeable and qualified inspectors carry out the checks.
Service Modifications
The owner should avoid altering the service conditions from those described in the manufacturer’s specifications. Changing factors like chemical composition, temperature, pressure, or turbidity can shorten the lifespan of FRP equipment. If such modifications are necessary, it is crucial to consult with the manufacturer to determine if modifications to the equipment are recommended to accommodate the changes.
FAQs about FRP Pipe Life Expectancy
The life expectancy of a FRP water tank can be quite long, typically ranging from 20 to 40 years or more, depending on the operating environment and maintenance. FRP water tanks are particularly valued for their corrosion resistance, which makes them ideal for storing various liquids, including water, chemicals, and wastewater. The life expectancy is influenced by factors like the tank’s exposure to UV light, the temperature of the liquid being stored, and the level of maintenance it receives over time. In most cases, well-maintained FRP water tanks can meet or exceed their expected lifespan, providing a reliable storage solution for decades.
FRP is known for its exceptional durability and resistance to harsh conditions, making it a versatile material in many industries. Its durability is derived from its composite structure, which includes high-strength glass fibers and a durable resin matrix. This combination makes FRP resistant to corrosion, chemicals, and weathering. Its lightweight nature does not compromise its strength, and it can withstand significant stress and pressure over long periods. The durability of FRP makes it an ideal choice for applications in chemical processing, water treatment, and industrial infrastructure, ensuring that it remains operational for decades without significant degradation.
The design life of FRP typically ranges from 30 to 50 years, depending on the specific application and environmental conditions it is exposed to. Engineers often select FRP for its ability to meet long-term performance requirements in corrosive and demanding environments. FRP is designed to maintain its mechanical strength and structural integrity over extended periods without requiring significant maintenance or repair. Factors that can impact the design life of FRP include UV exposure, chemical interactions, mechanical loads, and temperature variations. However, with proper care and the right application, FRP often meets or exceeds its expected design life, providing reliable service in critical infrastructure.
The shelf life of FRP (Fiber Reinforced Plastic) materials, including FRP pipes, depends on storage conditions and resin types. Under optimal conditions—cool, dry, and protected from UV exposure—FRP materials can last for several years before deterioration begins. Typically, the shelf life of FRP resin can range from 1 to 5 years, depending on the resin used and environmental factors. Proper storage can help maintain the integrity of the materials, ensuring they perform as expected when installed. However, once exposed to elements, the lifespan may be reduced.
The lifespan of a GRP (Glass Reinforced Plastic) pipe, a type of FRP, typically ranges from 50 to 100 years. Factors such as installation environment, the type of fluid transported, and maintenance routines can affect this range. GRP pipes are highly resistant to corrosion, chemical damage, and abrasion, contributing to their long service life. In favorable conditions, these pipes can easily exceed 50 years without significant degradation, making them a cost-effective choice for infrastructure.
FRP tanks, used for storage or chemical processing, can last anywhere from 20 to 50 years, depending on usage, environmental conditions, and maintenance. The lifespan of an FRP tank is influenced by factors such as chemical exposure, UV radiation, temperature fluctuations, and the structural integrity of the resin. In ideal conditions, with proper maintenance and periodic inspections, FRP tanks can offer a long-term solution. However, harsh conditions (e.g., exposure to aggressive chemicals or extreme weather) may shorten their lifespan.
Flexible PVC pipes typically last around 25 to 40 years under normal conditions. The material’s lifespan is influenced by environmental factors, chemical exposure, UV radiation, and mechanical stress. Flexible PVC is more prone to damage from extreme temperatures and UV degradation compared to rigid PVC pipes. However, proper installation and maintenance can help maximize its lifespan. When used indoors or in protected environments, flexible PVC pipe can perform for decades without major issues.
While FRP (Fiber Reinforced Plastic) pipes have a high strength-to-weight ratio, they are not stronger than steel in terms of raw tensile strength. Steel has a higher inherent strength, but FRP pipes are more lightweight and corrosion-resistant, which makes them suitable for many applications where traditional materials like steel might fail due to rust or wear. In structural applications, FRP may not always match the strength of steel but offers significant advantages in corrosion resistance, making it ideal for chemical processing and outdoor environments.
FRP (Fiber Reinforced Plastic) materials can last for several decades, with typical lifespans ranging from 20 to 50 years, depending on the application and environmental conditions. FRP pipes and tanks are highly resistant to corrosion, UV radiation, and chemical damage, which contributes to their long service life. With proper installation, maintenance, and protection from extreme conditions, FRP materials can exceed their expected lifespan and continue to provide reliable service. In aggressive environments, such as wastewater treatment or chemical processing, FRP can last for decades with minimal degradation.
FRP (Fiber Reinforced Plastic) and fiberglass are often used interchangeably, but there are distinctions. Fiberglass is a type of FRP where glass fibers are used as the reinforcing material. FRP, however, is a broader term that refers to any composite material where fibers (glass, carbon, aramid, etc.) are embedded in a resin matrix. FRP tends to be stronger, more versatile, and available in different grades depending on the fiber type used, whereas fiberglass is specifically designed for applications requiring high strength, durability, and light weight. The choice between FRP and fiberglass depends on the application requirements.
FRP (Fiber Reinforced Plastic) and GRP (Glass Reinforced Plastic) pipes are both types of composite materials made by embedding reinforcing fibers in a resin matrix, but the key difference lies in the type of fibers used. GRP pipes specifically use glass fibers as the reinforcing material, while FRP can use a variety of fibers (including glass, carbon, or aramid). GRP pipes are known for their superior corrosion resistance, especially in aggressive environments like wastewater treatment or chemical processing. The term “FRP” is more general and can refer to a variety of composites, while “GRP” specifically refers to glass fiber composites.
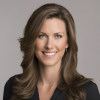
As the editor of GangLong Fiberglass, I have years of experience and in-depth research, focusing on cable tray products, fiberglass solutions, and grille systems. I incorporate years of industry insights and practical experience into every content, committed to promoting the progress of the industry. At GangLong Fiberglass, my commitment is reflected in every product, from innovative cable trays to durable fiberglass solutions and sturdy grille systems. As an authoritative voice in the industry, my goal is to provide valuable information to professionals and businesses and promote forward-looking solutions.